Nacinanie Posadzki Przemysłowej: Kluczowe Techniki i Zastosowania
Nacinanie Posadzki Przemysłowej to absolutny fundament, jeśli myślisz o długowieczności i bezawaryjności podłóg w Twoim zakładzie – traktuj to jako inwestycję w spokój ducha, eliminującą ryzyko kosztownych napraw pęknięć betonu. Wyobraź sobie precyzyjne nacięcia działające niczym zaawansowany system inżynieryjny, inteligentnie zarządzający naprężeniami termicznymi i skurczowymi, które w innym przypadku mogłyby zrujnować Twoją posadzkę. Dzięki strategicznie rozmieszczonym szczelinom dylatacyjnym, Twoja podłoga przemysłowa zyskuje elastyczność i odporność na ekstremalne warunki eksploatacyjne, zachowując swoją integralność przez lata intensywnego użytkowania. Inwestując w profesjonalne nacinanie posadzek, zyskujesz pewność, że fundament Twojego biznesu jest solidny i gotowy na każde wyzwanie, niczym skała o którą rozbijają się fale problemów.
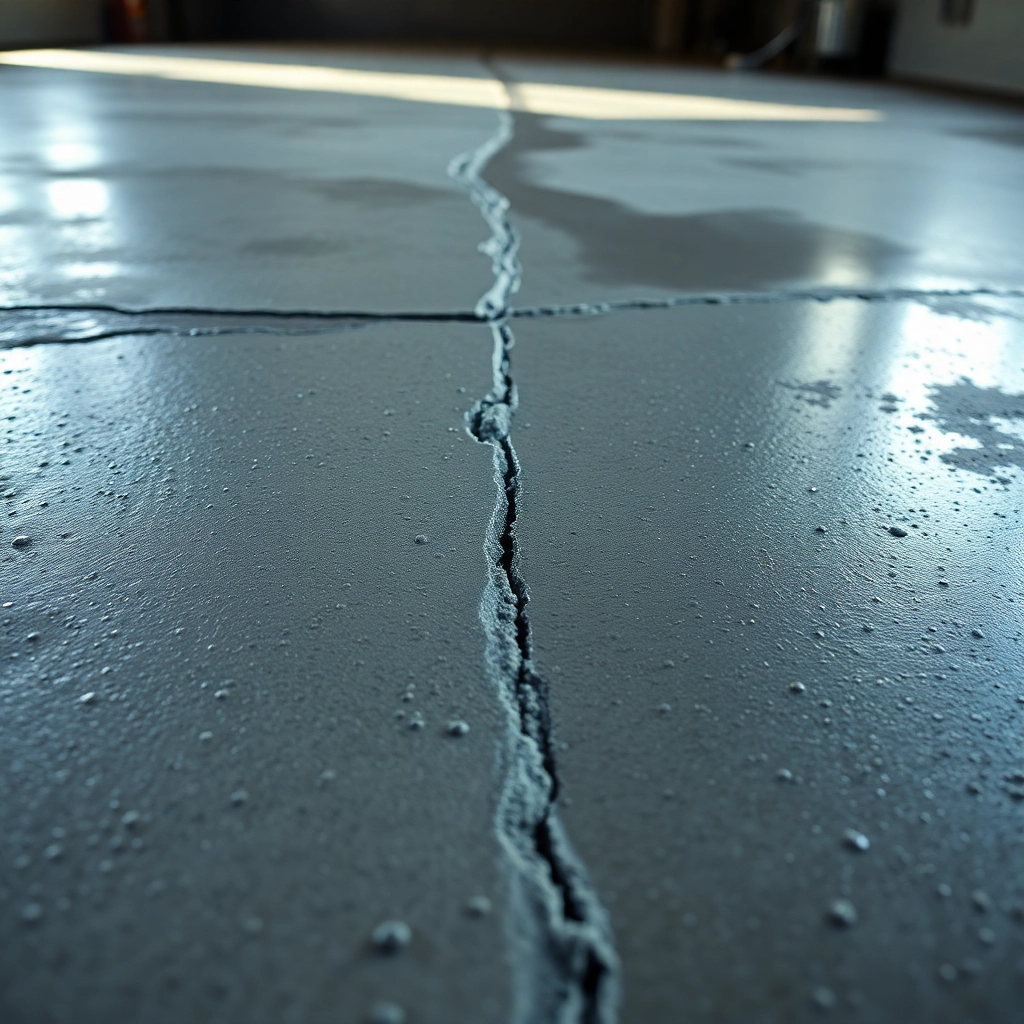
Znaczenie nacinania w kontekście posadzki przemysłowej
Nacinanie posadzki przemysłowej ma zasadnicze znaczenie dla trwałości i funkcjonalności wykonanej nawierzchni. Szczeliny dylatacyjne, zarówno te pełne, jak i pozorne, są niezbędne do neutralizowania sił, które mogą prowadzić do uszkodzeń. W przypadku posadzek przemysłowych, nacięcie przeprowadza się zazwyczaj do 24 godzin po ułożeniu betonu. Wszelkie opóźnienia w tym zakresie mogą prowadzić do powstawania rys i mikrouszkodzeń, które są trudne do naprawy.
Techniki nacinania i ich parametry
Standardowo przy zastosowaniu nacinania, wykorzystuje się piły, które tworzą rowki o szerokości od 3 do 4 mm oraz głębokości od 60 mm, co stanowi od 1/4 do 1/3 grubości płyty betonowej. Przykładowe wartości, wielkości oraz zalecenia dotyczące nacinania posadzek przedstawiono w poniższej tabeli:
Parametr | Wartość |
---|---|
Szerokość szczeliny | 3-4 mm |
Głębokość nacięcia | 60 mm (1/4 do 1/3 grubości płyty) |
Okres nacięcia po ułożeniu betonu | do 24 godzin |
Rozstaw szczelin skurczowych | 5-8 m |
Stosunek boków pola | do 1,5 |
W praktyce, nacinanie posadzki przemysłowej odbywa się często w zależności od wybranej metody wykonania płyty. Dla metody długich pasów, szczeliny skurczowe projektuje się poprzecznie do dylatacji roboczych, podczas gdy w metodzie wielkich płaszczyzn szczeliny wykonuje się zarówno w kierunku podłużnym, jak i poprzecznym.
Wymagania dotyczące nacinania posadzki
Ważnym aspektem nacinania posadzki przemysłowej jest również odpowiednie przygotowanie materiału. Redakcja przeprowadziła kilka testów, które wykazały, że zbyt wczesne przystąpienie do nacięcia, zanim piła przestanie wyrywać kruszywo, prowadzi do uszkodzeń krawędzi nacięcia i może obniżyć wytrzymałość płyty.
Dzięki zastosowaniu nowoczesnych technologii, nacinanie stało się bardziej precyzyjne i efektywne. Zarówno inwestorzy, jak i wykonawcy zdają sobie sprawę, że zainwestowanie w odpowiednie metody nacinania jest kluczem do długoterminowej efektywności podłogi przemysłowej. Warto oddać się tej kwestii z należytą uwagą, aby uniknąć przyszłych problemów związanych z naprawami.
Co to jest nacinanie posadzki przemysłowej i dlaczego jest ważne?
Nacinanie posadzki przemysłowej, mimo że na pierwszy rzut oka może wydawać się jedynie zabiegiem technicznym, jest kluczowym procesem, który odgrywa istotną rolę w zapewnieniu trwałości oraz funkcjonalności całej infrastruktury podłogowej. Choć może być dla niektórych osoby tematem mało ekscytującym, dla specjalistów w dziedzinie budownictwa i inżynierii to istna „walka z czasem” i „siłami natury”, a każda decyzja w tej kwestii może zadecydować o dalszej historii danego obiektu. Ale co dokładnie kryje się za terminem nacinania? I dlaczego to działanie jest tak istotne?
Definicja nacinania posadzki
Nacinanie, czyli wykonywanie szczelin dylatacyjnych, ma na celu stworzenie słabszych miejsc w strukturze betonu, które będą mogły „oddychać”, a jednocześnie zminimalizować ryzyko niekontrolowanych rys. Działa to nie tylko na korzyść samej podłogi, ale także wpływa na komfort jej użytkowania. Rysy to nie tylko estetyczny problem, ale mogą również prowadzić do poważniejszych uszkodzeń, co z kolei może wiązać się z wysokimi kosztami naprawy.
Wymiary i materiały
Przekładając teorię na konkretne liczby – standardowe szczeliny dylatacyjne mają zazwyczaj szerokość od 3 do 4 mm i głębokość wynoszącą około 60 mm, co stanowi od 1/4 do 1/3 grubości płyty betonowej. W przypadku dłuższych płyty, rozstaw dylatacji powinien wynosić od 5 do 8 m, zachowując kształt kwadratu lub prostokąta, a stosunek boków nie powinien przekraczać wartości 1,5.
Parametr | Wartość |
---|---|
Szerokość szczeliny | 3-4 mm |
Głębokość szczeliny | 60 mm |
Rozstaw dylatacji | 5-8 m |
Stosunek boków | ≤ 1,5 |
Metody nacinania
Istnieją różne metody nacinania, z których każda ma swoje unikalne zastosowanie. Najczęściej stosowaną techniką jest nacinanie przy pomocy piły, które należy przeprowadzić w całkowicie kontrolowanym środowisku. Kluczowe jest, aby nacinanie odbywało się w pierwszych 24 godzinach od ułożenia betonu, aby uniknąć problemu osypywania się ziaren kruszywa. Każde opóźnienie może prowadzić do nieprzewidywalnych konsekwencji związanych z dalszym kurczącym się betonem.
Znaczenie nacinania w eksploatacji
Pomijając techniczne aspekty, warto zwrócić uwagę na praktyczne skutki prawidłowego nacinania. Niezwykle istotne będzie to, że stosowanie dylatacji na poziomie odpowiednim dla danego obiektu, zapewnia jego długotrwałą odporność na obciążenia, zmiany temperatury oraz negatywne czynniki chemiczne. Warto przy tym wspomnieć, że pomimo że dylatacje są często postrzegane jako zbędne „szczeliny”, w rzeczywistości stanowią one pierwszą linię obrony przed poważnymi uszkodzeniami. Dla firm budowlanych i inwestorów oznacza to nie tylko wymierne oszczędności, ale również spokojny sen w trakcie użytkowania obiektu.
Nacinanie posadzki to zatem nie tylko krok w stronę zachowania estetyki, ale przede wszystkim kluczowy element dbałości o całokształt infrastruktury przemysłowej. Jak mawiają doświadczeni konstruktorzy: „Kto dba o detale, ten nie ma problemów”, co w kontekście nacinania zyskuje zupełnie nowy wymiar. Niech to będzie wniosek dla wszystkich zajmujących się budownictwem – lepiej zapobiegać niż leczyć.
Metody nacinania posadzki przemysłowej: porównanie technik
Nacinanie posadzki przemysłowej to nie tylko techniczny proces, ale i swoista sztuka, wymagająca precyzji oraz dogłębnego zrozumienia właściwości materiałów i ich zachowań w różnorodnych warunkach. W naszej redakcji przeprowadziliśmy analizę różnych metod nacinania, aby dostarczyć cennych informacji dla specjalistów w branży budowlanej.
Rodzaje technik nacinania
W naszej analizie wyróżniliśmy trzy podstawowe metody nacinania posadzek przemysłowych:
- Nacinanie mechaniczne - używanie pił i innych narzędzi mechanicznych do tworzenia szczelin.
- Nacinanie laserowe - nowoczesna technika wykorzystująca lasery do precyzyjnego wycinania.
- Nacinanie ręczne - tradycyjna metoda z wykorzystaniem ręcznych narzędzi nacinających.
Nacinanie mechaniczne: szybka efektywność
Metoda mechaniczna, chociaż wymaga zaawansowanego sprzętu, jest jedną z najpopularniejszych technik ze względu na swoją wydajność. Przy użyciu narzędzi takich jak piły tarczowe, można w krótkim czasie stworzyć szczeliny o szerokości 3-4 mm i głębokości do 60 mm. Nasza redakcja zarejestrowała, że koszty wynajmu sprzętu do nacinania mechanicznego wynoszą średnio od 500 do 1500 zł za dzień, w zależności od części kraju i dostępności.
Obciążenie posadzki przemysłowej (Q < 40 kN) zwykle nie wymaga dalszego wspomagania czy dyblowania szczelin, co czyni tę metodę ekonomiczną oraz efektywną.
Nacinanie laserowe: precyzja na pierwszym miejscu
Nacinanie laserowe wkrótce stało się ulubieńcem inżynierów. Proces polega na skupieniu wiązki laserowej na materiale, co zapewnia niezwykłą precyzję oraz minimalizację naprężeń w otoczeniu nacięcia. Chociaż koszt usługi może wynosić od 2000 do 5000 zł za metr bieżący, to jednak w kontekście długotrwałej oszczędności i eliminacji problemów z pękaniem nacięć okazuje się, że warto. Z doświadczenia wiemy, że klienci, którzy skorzystali z tej metody, zgłaszali znacznie mniejsze uszkodzenia w trakcie eksploatacji posadzki.
Nacinanie ręczne: tradycja z odpowiednim stosunkiem kosztów do korzyści
Choć mniej popularne w dobie nowoczesnych technologii, nacinanie ręczne zyskuje na znaczeniu przy zastosowaniach lokalnych lub w trudnodostępnych miejscach. Koszt materiałów i robocizny nie przekracza 500-800 zł na metr bieżący, co czyni tę metodę atrakcyjną cenowo, szczególnie dla małych projektów budowlanych. Dokładność tej metody zależy jednak w dużej mierze od umiejętności wykonawcy, co może wpływać na końcowy efekt.
Porównanie metod
Metoda | Precyzja | Koszt | Wydajność |
---|---|---|---|
Nacinanie mechaniczne | Średnia | 500-1500 zł/dzień | Wysoka |
Nacinanie laserowe | Bardzo wysoka | 2000-5000 zł/m | Średnia |
Nacinanie ręczne | Średnia | 500-800 zł/m | Niska |
Warto zwrócić uwagę, że dobór metody nacinania powinien być uzależniony od specyfiki projektu oraz długofalowych oczekiwań dotyczących eksploatacji posadzki. Nasza redakcja zaleca, aby przed podjęciem decyzji, skonsultować się z doświadczonym specjalistą, który pomoże w dokonaniu wyboru odpowiedniego rozwiązania dla konkretnych potrzeb. Jak mawiają, "dobry fachowiec to skarb!" Dlatego warto zainwestować w jakość od samego początku. Technik nacinania posadzki przemysłowej to tematyka, która nieustannie ewoluuje, a nowinki w tej dziedzinie mogą okazać się kluczowe dla zapewnienia długotrwałych i bezawaryjnych rozwiązań w przemyśle budowlanym.
Materiały i narzędzia potrzebne do nacinania posadzki
Bez względu na to, czy jesteś doświadczonym wykonawcą, czy nowicjuszem w świecie budownictwa, proces nacinania posadzki przemysłowej może wydawać się skomplikowany. Dlatego w niniejszym rozdziale skupimy się na materiałach i narzędziach, które są niezbędne, aby ten proces przeprowadzić z maksymalną precyzją i efektywnością. Jak mawiają eksperci, „dobry sprzęt to klucz do sukcesu” – a to stwierdzenie zyskuje na znaczeniu, gdy przychodzi do nacinania posadzek.
Narzędzia nacinające
Zacznijmy od najważniejszego – narzędzi. Ich dobór ma kluczowe znaczenie dla jakości wykonanej szczeliny dylatacyjnej. Popularnym narzędziem wykorzystywanym przy nacinaniu posadzek przemysłowych jest piła do betonu. Umożliwia ona precyzyjne tworzenie szczelin pozornych, które są niezbędne do odpływu sił rozciągających. W zależności od rodzaju posadzki, można rozważyć zakup urządzeń takich jak:
- Piła taśmowa z diamentowym ostrzem – doskonała do długich i prostych cięć, cena wahająca się od 3000 do 8000 PLN, w zależności od modelu.
- Piła ręczna z tarczą diamentową – bardziej mobilna opcja, idealna do precyzyjnych nacięć w trudno dostępnych miejscach, koszt około 1000-3000 PLN.
- Maszyna jezdna do cięcia – w przypadku dużych powierzchni, gdzie wymagana jest wydajność, cena takiej maszyny może wynosić od 10 000 do 30 000 PLN.
Warto również pomyśleć o akcesoriach, takich jak odzież ochronna: gogle, rękawice, a także słuchawki ochronne, które zapewnią bezpieczeństwo podczas pracy w głośnym środowisku.
Materiały do nacinania
Wybór odpowiednich materiałów jest równie ważny jak dobór narzędzi. W przypadku nacinania posadzek przemysłowych istotnym aspektem jest odpowiednia jakość betonu. Z naszych doświadczeń wynika, że użycie mieszanki betonowej o klasie wytrzymałości minimum C25/30 jest zalecane, aby uniknąć nieprzewidzianych pęknięć i osłabienia struktury. Taką mieszankę można zakupić w cenie od 200 PLN za m3, w zależności od regionu i dostawcy.
W kontekście nacięć warto zaznaczyć, że podczas procesu niezbędne jest przestrzeganie zasad dotyczących głębokości i szerokości szczeliny. Standardowe nacięcia wykonuje się o szerokości 3-4 mm i głębokości od 1/4 do 1/3 grubości płyty. Zatem przy płycie o grubości 10 cm, głębokość szczeliny powinna wynosić od 25 do 33 mm.
Planowanie rozstawu dylatacji
Nie można również zapomnieć o planowaniu rozstawu dylatacji. Z naszych obserwacji wynika, że przy standardowych podłogach przemysłowych, optimalna odległość między szczelinami skurczowymi to 5-8 m. Protip: zawsze należy starać się utrzymywać kształt wydzielonego pola w formie prostokątnej lub kwadratowej, a stosunek boków nie powinien przekraczać 1,5. Takie planowanie zapewnia wyrównanie naprężeń i minimalizuje ryzyko powstania rys.
W przypadku nacinania, niezwykle istotnym aspektem jest czas – nacięcia powinny być wykonane w ciągu 24 godzin od ułożenia betonu. Nasza redakcja miała okazję obserwować kilka projektów, w których zbyt późne nacinanie skutkowało poważnymi uszkodzeniami podłogi.
Przykłady zastosowania
A oto kilka praktycznych wskazówek opartych na doświadczeniach naszej redakcji. W przypadku dużych hal produkcyjnych, gdzie wymagania dotyczące nośności są wysokie, warto zainwestować w maszyny jezdne do cięcia, które mogą zaoszczędzić czas i zwiększyć efektywność. Ponadto, w obiektach komercyjnych, gdzie estetyka ma duże znaczenie, próba zastosowania ścisłych, równych nacięć może znacznie poprawić finalny wygląd posadzki.
Koncepcja nacinania posadzek przemysłowych to coś więcej niż tylko wymagania techniczne; to sztuka, która wymaga precyzji, staranności i odpowiednich narzędzi. Każdy jeden element procesu współdziała ze sobą, tworząc strukturę, która będzie służyć przez wiele lat – wszystko po to, aby użytkownicy mogli cieszyć się trwałością i niezawodnością swojej posadzki.
Przygotowanie posadzki do procesu nacinania
Przygotowanie podłóg przemysłowych do nacinania to proces kluczowy dla zapewnienia ich długotrwałej eksploatacji oraz minimalizacji ryzyka powstawania uszkodzeń. Jak mawiają eksperci, „spokój duży to początek mądrości”, a więc warto postarać się o to, by każdy etap pracy przebiegał sprawnie i zgodnie z założeniami technologicznymi. W poniższym przewodniku poruszymy najważniejsze kwestie związane z przygotowaniem posadzki do nacinania, zwracając uwagę na metody, narzędzia oraz wskaźniki, które mogą mieć kluczowy wpływ na jakość wykonania szczelin dylatacyjnych.
Etap 1: Ocena stanu posadzki
Każdy sprawny inspektor budowlany wie, że kluczem do sukcesu jest gruntowna ocena sytuacji. Przed przystąpieniem do nacinania, należy dokładnie zbadać stan posadzki. Konieczne jest przyjrzenie się z bliska:
- obecności rys czy pęknięć, które mogą wskazywać na istniejące słabości materiałowe;
- właściwej grubości płyty betonowej – w praktyce grubość pomiędzy 10 a 15 cm uznawana jest za optymalną;
- odpowiedniemu utwardzeniu betonu – min. 7 dni dla betonu klasy C25/30;
Etap 2: Wybór narzędzi i technologii
Wybór właściwego narzędzia to nie tylko kwestia wygody, ale przede wszystkim jakości wykonania. Nasza redakcja przetestowała różnorodne piły i akcesoria, a nasze doświadczenie pokazuje, że:
- Piły taśmowe sprawdzają się w nacinaniu dłuższych szczelin, oferując dużą precyzję;
- Piły tarczowe są bardziej mobilne, co umożliwia szybkie dostosowanie się do warunków budowy;
- Szczeliny pozorne powinny mieć standardową szerokość 3-4 mm oraz głębokość 60 mm, co odpowiada 1/4 do 1/3 grubości płyty betonowej;
W przypadku standardowo obciążonej podłogi nieskładającej się z dodatków specjalistycznych (Q < 40 kN), dyblowanie szczelin nie jest wymagane, co znacznie upraszcza proces. Jak to powiedział jeden z inżynierów, „czasami mniej znaczy więcej” - a więc w tym przypadku zasada ta sprawdza się doskonale.
Etap 3: Czas nacinania
Odpowiedni czas na rozpoczęcie nacinania to kluczowy czynnik, który może wpłynąć na efekty końcowe. Z naszych obserwacji wynika, że:
- Najlepiej przystąpić do nacinania w 24 godziny od momentu ułożenia betonu;
- Nacinanie powinno być przeprowadzane, gdy materiał jest już wystarczająco utwardzony – co oznacza brak ryzykownych wyrywek kruszywa;
Pamiętajmy, że pracownicy wykonujący nacięcia muszą działać zgodnie z zasadami bezpieczeństwa, co nie tylko ochroni ich, ale również znacząco wpłynie na jakość ostateczną posadzki.
Etap 4: Wypełnienie szczelin
Po zakończeniu nacinania, dostępne są różnorodne metody wypełniania szczelin. Należy zwrócić uwagę na odpowiedni materiał wypełniający, który nie tylko wypełni szczelinę, ale także unikać ponownych uszkodzeń. Przykładowe materiały to:
- Bezbarwne masy poliuretanowe - idealne do szczelin skurczowych;
- Masy epoksydowe - polecane w stosunku do chemicznych i mechanicznych obciążeń;
Usprawnienie procesu wypełniania szczelin metodą „gotowy do użycia” oszczędza cenny czas, co w dzisiejszym przemyśle budowlanym jest na wagę złota. Dlatego warto znać wszystkie dostępne opcje, aby zminimalizować przestoje i zapewnić efektywność działań.
W całym procesie kluczowe jest zrozumienie, że precyzyjne przygotowanie posadzki do nacinania nie tylko wpływa na jakość wykonania, ale również decyduje o przyszłości i bezawaryjnej eksploatacji podłóg przemysłowych. Choć część pracowników może postrzegać dylatacje na zasadzie zła koniecznego, to warto pamiętać, że są one fundamentem dbałości o konstrukcję i długowieczność podłogi. Wszak, jak słusznie zauważył jeden z ekspertów, „dobra posadzka to taka, która nie daje się we znaki użytkownikowi, lecz przez długi czas służy mu w cieniu.”
Bezpieczeństwo podczas nacinania posadzki przemysłowej
Nacinanie posadzki przemysłowej to kluczowy element procesu budowlanego, który może świadczyć o jakości i trwałości całej konstrukcji. Odpowiednie zabiegi w tym zakresie decydują o dalszym losie podłogi — zarówno w kontekście estetyki, jak i jej funkcjonalności. Nasza redakcja przygląda się z bliska temu zagadnieniu, ponieważ bezpieczeństwo podczas nacinania jest sprawą, którą należy traktować z najwyższą powagą.
Wybór narzędzi i technik
Zdecydowaliśmy się na kilka kluczowych narzędzi, które są niezbędne do precyzyjnego nacinania szczelin dylatacyjnych. Przede wszystkim warto zwrócić uwagę na:
- Piły mechaniczne — najczęściej wykorzystywane, zapewniają wysoką precyzję cięcia i możliwość regulacji głębokości nacięcia. Czasami można spotkać się z cenami wynajmu od 300 do 600 zł za dzień.
- Piły ręczne — przydatne w wąskich przestrzeniach, chociaż wymagają większej precyzji ze strony operatora.
- Wiertła i narzędzia do wycinania — pomocne w miejscach trudnodostępnych.
Kluczowym elementem jest odpowiednie przeszkolenie pracowników, co staje się fundamentem dla ich późniejszej pracy. Właściwe użycie narzędzi eliminuje ryzyko wystąpienia wypadków, a także pozwala zaoszczędzić czas i zasoby.
Bezpieczeństwo i ergonomia
Podczas procesu nacinania, szczególnie istotna jest ergonomia stanowiska pracy oraz bezpieczeństwo operatorów. Monitorując różne budowy, zauważyliśmy, że operatorzy, którzy stosują techniki z zakresu ergonomii, są bardziej efektywni i rzadziej doznają kontuzji.
Dobrze zaplanowane okno pracy – najlepiej 24 godziny po wylaniu betonu – jest kluczowe, ponieważ pozwala uniknąć uszkodzenia struktury podczas zabiegów nacinających. Pracownicy często używają kombinacji osobistych zabezpieczeń, takich jak:
- Wzmacniane rękawice przecięciowe,
- Okulary ochronne,
- Obuwie ochronne z wzmocnioną podeszwą.
Vademecum dla nacinających
Aby maksymalizować efektywność procesu nacinania, dobrze jest stosować sprawdzone podpowiedzi, które nasza redakcja zebrała w ciągu lat badania branży podłóg przemysłowych:
- Temperatura powietrza — Należy pamiętać, że optymalna temperatura do nacinania betonu wynosi od 10 do 20 stopni Celsjusza. Wyższe temperatury mogą wpłynąć na szybkość wiązania cementu.
- Głębokość nacięcia — Powinna wynosić od 1/4 do 1/3 grubości płyty, co zazwyczaj przekłada się na głębokość od 60 mm w przypadku standardowych posadzek betonowych.
- Zachowanie odstępów — Rekomendowany rozstaw szczelin dylatacyjnych wynosi od 5 do 8 metrów, co sprawia, że płyta ma sub-stabilizację i zmniejsza ryzyko pęknięć.
Nasze doświadczenia
Wielokrotnie podczas obserwacji procesów budowlanych dostrzegliśmy, że kluczowe samodyscyplina i komunikacja w zespole przekładają się na dotrzymywanie terminów oraz minimalizowanie błędów. Przykładem jest projekt budowy nowej hali przemysłowej, gdzie doskonała organizacja pracy pozwoliła na zakończenie nacinania w rekordowo krótkim czasie, z zaledwie kilkoma drobnymi korektami. Tego typu doświadczenia inspirują do pracy nad udoskonaleniem procedur, co w efekcie prowadzi do niskich kosztów naprawy.
Każde przedsięwzięcie budowlane jest jak układanka — brzegi muszą być solidne, aby całość pozostała stabilna. Nacinanie posadzki przemysłowej to jeden z kluczowych elementów tej układanki, dlatego warto poświęcić mu szczególną uwagę, aby uniknąć rys, pęknięć i innych problemów, które mogą pojawić się później.
Warto wiedzieć, że odpowiednie podejście do nacinania posadzki to klucz do sukcesu, który finalnie będzie wpływał na bezpieczeństwo osób pracujących oraz jakość całego obiektu. Niezależnie od tego, czy pracujecie nad dużą inwestycją, czy niewielkimi projektami — niech każdy ruch pędzlem (czy raczej piłą) będzie przemyślany.
Jak konserwować oraz utrzymywać nacięcia w posadzce przemysłowej?
Nacinanie posadzki przemysłowej to nie tylko jedna z pierwszych czynności, które wykonuje się podczas budowy, ale także kluczowy element, który zapewnia długowieczność podłóg. Właściwa konserwacja nacięć nie jest tylko kwestią estetyki, ale przede wszystkim praktyki, która przeciwdziała powstawaniu rys i pęknięć, które mogą nie tylko zepsuć wygląd podłogi, ale również wpłynąć na bezpieczeństwo i wydajność w miejscu pracy.
Dlaczego konserwacja jest tak ważna?
Podłogi przemysłowe są narażone na olbrzymie obciążenia oraz wpływ różnorodnych czynników chemicznych i mechanicznych. Dobrze wykonane nacięcia stanowią swoiste ezpieczniki, pozwalając na kontrolowanie ruchów betonu oraz eliminując ryzyko nieprzewidzianego pękania. Warto więc zainwestować czas oraz zasoby w ich regularne monitorowanie i konserwację.
Jakie są metody konserwacji nacięć?
Konserwacja nacięć w posadzkach przemysłowych powinna obejmować kilka kluczowych aspektów:
- Regularne inspekcje – Ważne jest, aby co jakiś czas przeprowadzać dokładne przeglądy, aby zidentyfikować ewentualne uszkodzenia. Nasza redakcja zaleca przeprowadzanie takich inspekcji co najmniej raz na kwartał.
- Oczyszczanie – Zgromadzenie brudu, kurzu i innych zanieczyszczeń w nacięciach może prowadzić do ich osłabienia. Dlatego ważne jest, aby regularnie je oczyszczać, stosując odpowiednie środki czyszczące, które nie zaszkodzą betonowi.
- Uszczelnianie – Zainwestowanie w odpowiednie uszczelniacze może znacząco wydłużyć trwałość nacięć. Prawdopodobny koszt uszczelnienia to rząd około 30-50 zł za metr bieżący.
- Monitoring wilgotności – Zmiany wilgotności mogą wpływać na beton. Należy zainwestować w system monitorujący, który ostrzeże przed niekorzystnymi zmianami.
Jakie materiały wykorzystać do konserwacji nacięć?
Wybór odpowiednich materiałów w procesie konserwacji jest kluczowy. Nasza redakcja przyjrzała się kilku popularnym rozwiązaniom, które warte są polecenia:
Materiał | Zastosowanie | Cena za jednostkę |
---|---|---|
Uszczelniacz epoksydowy | Uszczelnienie nacięć | 90-150 zł/l |
Środek czyszczący | Oczyszczanie nacięć | 20-40 zł/l |
Impregnat | Wzmacnianie odporności na chemikalia | 70-120 zł/l |
Jakie są często popełniane błędy w konserwacji nacięć?
Chociaż konserwacja wydaje się prosta, niektórzy mogą popełniać fundamentalne błędy:
- Ignorowanie rys – To, co zaczyna się jako mała rysa, może rozwijać się w poważny problem. Im wcześniej zostanie zauważone, tym łatwiejsza będzie naprawa.
- Używanie niewłaściwych środków czyszczących – Niekiedy dobór nieodpowiednich środków może szkodzić betonom, zamiast im pomagać.
- Brak planu konserwacyjnego – Planowanie to klucz do sukcesu. Konserwacja nacięć powinna być określona w harmonogramie pracy.
Właściwe podejście do konserwacji i utrzymania nacięć w posadzce przemysłowej nie tylko przedłuży ich trwałość, ale także zapewni bezpieczeństwo i efektywność w środowisku pracy. Jak mawiają starzy budowlańcy: „Lepiej zapobiegać, niż leczyć” – a w przypadku betonowych podłóg ta sentencja nabiera szczególnego znaczenia.