Panele SIP: Jak zrobić? Technologia, materiały i produkcja w 2025 roku
Zastanawiasz się, jak powstają te panele SIP, które rewolucjonizują współczesne budownictwo? W istocie, panele SIP jak zrobić sprowadza się do inteligentnego połączenia warstw: to nic innego jak złączenie sztywnego rdzenia izolacyjnego, najczęściej styropianu, XPS lub pianki PUR, z dwiema zewnętrznymi płytami konstrukcyjnymi pod wysokim ciśnieniem za pomocą specjalistycznego kleju poliuretanowego. Ta prosta idea stojąca za Strukturalnymi Panelami Izolacyjnymi tworzy zadziwiająco wytrzymały i efektywny termicznie moduł, gotowy do szybkiego montażu. Domy SIP wyrastają niczym klocki dla dorosłych, pozwalając zamknąć surowy stan budynku w zadziwiająco krótkim czasie.
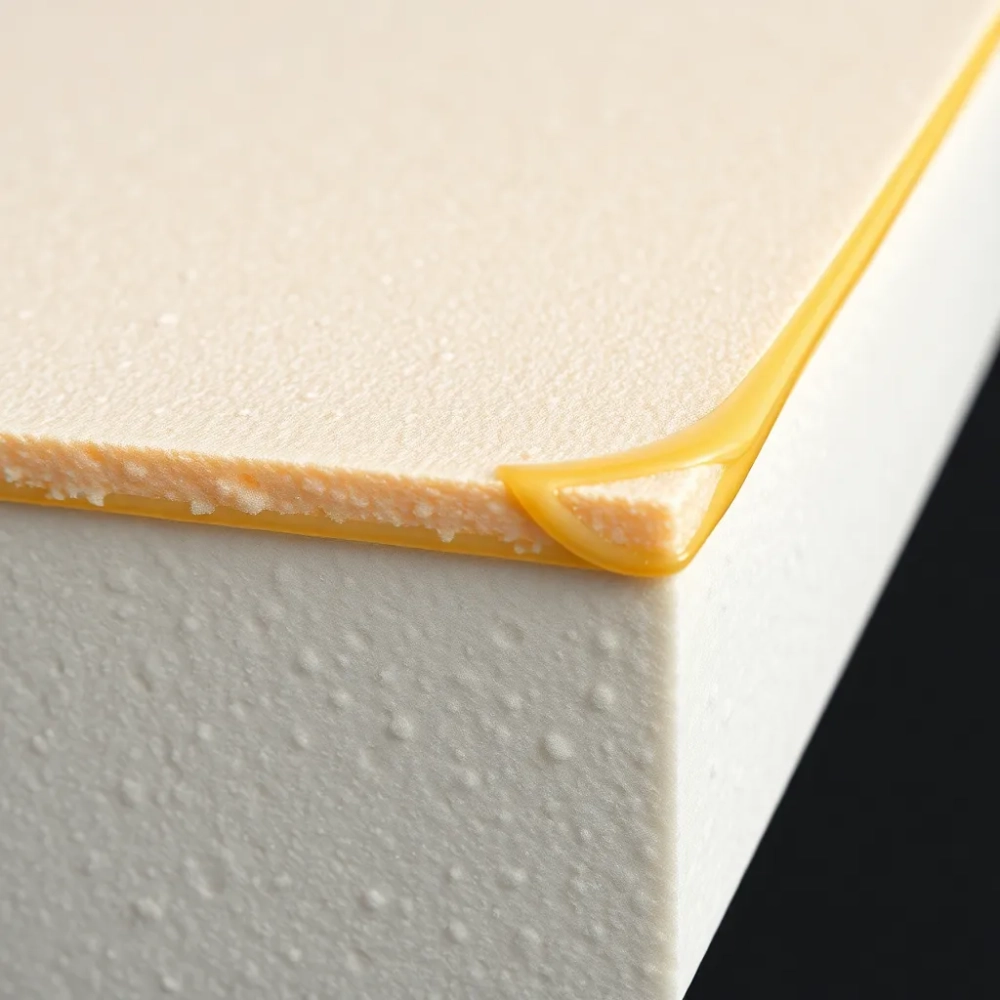
Patrząc na ewolucję technologii budowlanych, panele SIP stanowią znaczący krok naprzód w porównaniu do tradycyjnych metod murowanych czy nawet szkieletowych. Skracają czas realizacji inwestycji, zmniejszają ilość odpadów na budowie i zapewniają doskonałą izolacyjność. Aby zobrazować efektywność tej metody, warto przyjrzeć się danym porównującym kluczowe aspekty. Różne materiały i procesy wpływają na końcowe właściwości, a szczegóły są tu, jak zwykle, kluczowe.
Przyjrzyjmy się bliżej specyfice porównywanych systemów budowlanych, w tym paneli SIP, koncentrując się na trzech istotnych parametrach. Analizując czas budowy, koszt materiałów oraz izolacyjność termiczną, zarysowuje się obraz efektywności. To jak spojrzenie na puzzle z góry – nagle widać, jak wszystkie elementy do siebie pasują lub jak bardzo się różnią.
System Budowy | Przykładowy Czas Budowy (Stan surowy zamknięty 100m²) | Orientacyjny Koszt Materiałów (Współczynnik) | Przykładowy Współczynnik U (dla ściany standardowej) [W/m²K] |
---|---|---|---|
Tradycyjny Murowany (pustak ceramiczny + ocieplenie EPS 15cm) | ~3-4 miesiące | ~1.0 - 1.2 | ~0.18 - 0.22 |
SIP (EPS rdzeń 15cm + OSB 15mm) | ~3-6 tygodni | ~1.1 - 1.3 | ~0.15 - 0.18 |
Szkielet Drewniany (wełna mineralna 20cm) | ~4-8 tygodni | ~1.0 - 1.1 | ~0.16 - 0.19 |
SIP (PUR rdzeń 12cm + OSB 15mm) | ~3-6 tygodni | ~1.3 - 1.5 | ~0.12 - 0.15 |
Zaprezentowane dane, choć uśrednione i zależne od wielu czynników, wyraźnie wskazują na przewagę paneli SIP pod względem czasu realizacji. Krótszy okres budowy to nie tylko szybsze zamieszkanie, ale często również niższe koszty robocizny i mniejsze ryzyko przestojów z powodu pogody. W kontekście izolacyjności termicznej, panele SIP z rdzeniem PUR wyróżniają się, osiągając bardzo niskie współczynniki U przy stosunkowo niewielkiej grubości ściany.
Różnica w koszcie materiałów na korzyść tradycyjnych metod może być początkowo widoczna, jednak należy ją zestawić z niższymi kosztami pracy i fundamentalnie inną strukturą budżetowania. W tradycyjnym budownictwie koszty materiałów są rozłożone w czasie na wiele etapów, w przypadku SIP duża część wydatków przypada na dostawę gotowych paneli. Kluczowe jest także to, że wyższa izolacyjność SIP przekłada się na niższe rachunki za ogrzewanie w przyszłości, co stanowi długoterminową korzyść finansową dla inwestora. Całościowe podejście do budżetu i przyszłych kosztów eksploatacji często pokazuje, że system SIP jest konkurencyjnym, a nawet bardziej opłacalnym wyborem w perspektywie lat. To inwestycja w komfort i portfel.
Dodatkowo, szybkość wznoszenia konstrukcji z SIP pozwala na wcześniejsze zamknięcie budynku, co chroni go przed działaniem niekorzystnych warunków atmosferycznych. Minimalizuje to ryzyko zawilgocenia materiałów, co jest kluczowe dla trwałości i zdrowego klimatu wewnątrz. To przewaga, która nie zawsze jest łatwo przeliczalna na pieniądze, ale ma realny wpływ na jakość i długowieczność inwestycji. W efekcie, pozornie wyższy koszt jednostki materiału, jaką jest panel, jest rekompensowany przez inne, równie ważne czynniki ekonomiczne i jakościowe.
Kluczowe komponenty paneli SIP: Wybór płyt konstrukcyjnych
Pierwszą, wierzchnią warstwą w "kanapce" panelu SIP są płyty konstrukcyjne. Pełnią one funkcję nośną, przyjmując obciążenia i przekazując je na szkielet domu lub bezpośrednio na fundament w zależności od systemu montażu. Są jak twarda skorupa, chroniąca cenne wnętrze.
Najpopularniejszym wyborem na rynku europejskim i północnoamerykańskim są płyty OSB, w szczególności OSB/3 lub OSB/4. OSB (Oriented Strand Board) składa się ze sprasowanych wiórów drzewnych, zorientowanych warstwowo, co nadaje jej dużą wytrzymałość. Grubość najczęściej stosowanych płyt OSB w panelach SIP to 12 mm lub 15 mm, rzadziej 18 mm, w zależności od wymagań projektowych i przeznaczenia elementu.
Alternatywą dla OSB jest płyta MFP (Multi Functional Panel). Charakteryzuje się ona jednorodną orientacją wiórów we wszystkich kierunkach, co zapewnia jej lepszą sztywność i wytrzymałość na zginanie oraz rozciąganie w każdym punkcie. Płyty MFP są często bardziej odporne na wilgoć niż standardowe OSB, co może być istotne na etapie budowy.
Poza drewnopochodnymi płytami, istnieją inne, bardziej specjalistyczne opcje. Płyty cementowe, jak włóknocementowe (np. Cembrit) lub cementowo-wiórowe (np. Velox, Betopan), charakteryzują się wysoką odpornością na ogień, wilgoć i szkodniki. Stosowane są często w panelach przeznaczonych do zastosowań przemysłowych, elewacji wentylowanych, lub w miejscach o podwyższonych wymaganiach ogniowych.
Płyty magnezowe (MgO Board) to kolejna interesująca alternatywa, która zyskuje na popularności. Są lekkie, niepalne, odporne na wodę i pleśń. Oferują dobrą izolację akustyczną i są stosunkowo łatwe w obróbce, choć wymagają odpowiednich narzędzi. Ich cena jest zazwyczaj wyższa niż płyt OSB/MFP.
Wybór płyty konstrukcyjnej zależy ściśle od funkcji danego elementu panelu i specyfiki projektu. Ściany zewnętrzne wymagają innej wytrzymałości i odporności niż wewnętrzne ściany działowe czy panele dachowe. Projektant musi wziąć pod uwagę obciążenia wiatrowe, śniegowe, wymagania statyczne i pożarowe.
Parametry mechaniczne płyt, takie jak moduł sprężystości czy wytrzymałość na ścinanie, są kluczowe dla prawidłowego zaprojektowania budynku z paneli SIP. Producenci paneli ściśle określają, które typy płyt mogą być użyte z danym rdzeniem izolacyjnym i jakiej grubości muszą być do poszczególnych zastosowań. Ignorowanie tych wytycznych prowadzi do osłabienia konstrukcji.
Odporność na wilgoć jest kolejnym ważnym czynnikiem, szczególnie w polskim klimacie. Płyty używane do paneli SIP powinny posiadać odpowiednią klasę wodoodporności. Mimo to, podczas budowy panele należy chronić przed prolonged kontaktem z wodą, np. przez szczelne okrycie na czas przestojów. Z doświadczenia wiemy, że nawet najlepszy materiał źle składowany traci swoje właściwości.
Gęstość i waga płyt wpływają na całkowitą wagę panelu, co ma znaczenie podczas transportu i montażu. Płyty MgO są zazwyczaj lżejsze od cementowych, a OSB/MFP lżejsze od obu tych typów. Lżejsze panele ułatwiają pracę na budowie i mogą redukować potrzebę użycia ciężkiego sprzętu.
Obróbka płyt na etapie produkcji paneli SIP jest precyzyjnym procesem. Cięcie płyt do wymiarów odbywa się zazwyczaj na zautomatyzowanych piłach lub, w bardziej zaawansowanych liniach, na frezarkach CNC, które potrafią wykonać skomplikowane kształty i otwory na okna czy drzwi. Precyzja cięcia ma ogromny wpływ na łatwość montażu gotowych elementów na budowie. Niedokładność rzędu kilku milimetrów na jednym panelu potrafi skumulować się w poważne problemy na całej długości ściany. Wyobraźmy sobie próbę złożenia mebla z niedokładnie dociętymi elementami – podobnie dzieje się na budowie z krzywymi panelami.
Właściwe składowanie płyt przed ich użyciem w produkcji jest równie ważne jak sam proces produkcji. Muszą być chronione przed wilgocią, deformacją i uszkodzeniami mechanicznymi. Producenci paneli zazwyczaj przestrzegają rygorystycznych procedur odbioru i magazynowania surowców. To podstawa utrzymania wysokiej jakości finalnego produktu. Trochę jak pieczenie ciasta – nawet najlepsze składniki nie dadzą rady, jeśli są źle przechowywane.
Estetyka powierzchni płyty ma mniejsze znaczenie, ponieważ zazwyczaj jest ona później pokrywana tynkiem, elewacją wentylowaną, płytą gipsowo-kartonową od wewnątrz. Jednak jakość powierzchni, jej gładkość i jednorodność mogą wpływać na przyczepność kolejnych warstw wykończeniowych lub kleju podczas produkcji.
Analizując rynek, można zauważyć, że dominacja płyt OSB/3 wynika z ich dobrego stosunku ceny do parametrów użytkowych. Są wystarczająco wytrzymałe dla większości zastosowań w budownictwie mieszkaniowym i łatwo dostępne. To sprawia, że produkcja paneli SIP z użyciem OSB jest ekonomicznie uzasadniona dla szerokiego grona odbiorców. Nie oznacza to jednak, że są one zawsze najlepszym wyborem – dla specyficznych projektów, gdzie kluczowa jest np. niepalność czy podwyższona odporność na wilgoć, lepsze będą inne materiały.
Badania i rozwój wciąż przynoszą nowe materiały, które mogą być potencjalnie wykorzystane jako płyty konstrukcyjne w panelach SIP. Naukowcy pracują nad materiałami na bazie włókien roślinnych, materiałami kompozytowymi z recyklingu, czy ulepszonymi formami płyt cementowych. Innowacja w tym obszarze ma na celu poprawę parametrów, obniżenie kosztów lub zwiększenie ekologiczności. Branża budowlana, choć czasem konserwatywna, powoli otwiera się na nowe technologie, jeśli te udowadniają swoją wartość i bezpieczeństwo. A panele SIP są świetnym przykładem adaptacji nowoczesnych materiałów. Pamiętajmy, że świat idzie do przodu, a budownictwo musi nadążać. Czy pięćdziesiąt lat temu ktoś myślał o budowaniu domu z "plastiku i trocin"?
Wnętrze panelu SIP: Rodzaje materiałów izolacyjnych
Serce panelu SIP bije dzięki rdzeniowi izolacyjnemu, który jest wciśnięty pomiędzy dwie płyty konstrukcyjne. To właśnie ten materiał odpowiada za niezwykłe właściwości termiczne całego modułu. Wybór rdzenia ma fundamentalny wpływ na końcowy współczynnik przenikania ciepła U i w konsekwencji na koszty ogrzewania czy klimatyzacji. Domy SIP to prawdziwi mistrzowie w oszczędzaniu energii, a to zasługa właśnie tego wewnętrznego wypełnienia.
Najbardziej powszechnym materiałem stosowanym w rdzeniach paneli SIP jest polistyren ekspandowany, czyli popularny styropian (EPS). Charakteryzuje się on dobrą izolacyjnością termiczną, jest lekki i stosunkowo tani. W produkcji paneli SIP używa się zazwyczaj styropianu o podwyższonej gęstości (np. EPS 100, EPS 150), aby zapewnić odpowiednią sztywność i wytrzymałość na ściskanie, co jest kluczowe dla struktury panelu. Jego typowa gęstość wynosi od 15 do 25 kg/m³.
Innym, bardziej wydajnym termicznie materiałem jest polistyren ekstrudowany (XPS). Wytwarzany w inny sposób niż EPS, posiada zamkniętą strukturę komórkową, co czyni go bardziej odpornym na wilgoć i charakteryzującym się lepszym współczynnikiem przewodzenia ciepła (λ). Choć droższy od EPS, mniejsza grubość XPS pozwala osiągnąć podobną izolacyjność, co może być ważne w projektach z ograniczeniami przestrzeni. Typowa gęstość XPS w panelach SIP waha się od 30 do 40 kg/m³.
Absolutnym liderem pod względem izolacyjności termicznej spośród powszechnie stosowanych rdzeni jest pianka poliuretanowa (PUR), w tym jej odmiana PIR (poliizocyjanurat), która ma lepsze właściwości ogniowe. PUR/PIR ma najniższy współczynnik λ, co oznacza, że dla osiągnięcia tej samej izolacyjności co EPS, potrzebna jest znacznie cieńsza warstwa pianki. To z kolei pozwala na zastosowanie cieńszych, lżejszych paneli o tej samej efektywności energetycznej, lub superizolowanych paneli o standardowej grubości. Gęstość pianki PUR/PIR w rdzeniach paneli SIP to zazwyczaj 30-40 kg/m³.
Wybór grubości rdzenia izolacyjnego jest bezpośrednio powiązany z docelowym współczynnikiem U ściany, dachu czy podłogi, który określony jest w projekcie budynku i normach budowlanych. Typowe grubości rdzenia izolacyjnego w panelach SIP dla ścian zewnętrznych w budownictwie mieszkaniowym wynoszą od 100 mm do 200 mm. Panel o grubości 150 mm rdzenia EPS i 15 mm płyt OSB daje całkowitą grubość około 180 mm, osiągając współczynnik U w okolicach 0.18 W/m²K, co spełnia obecne normy, a często je przewyższa. Panel z rdzeniem PUR 120 mm może osiągnąć U poniżej 0.15 W/m²K.
W produkcji paneli SIP z rdzeniem EPS lub XPS, izolacja dostarczana jest zazwyczaj w postaci dużych bloków lub płyt, które następnie są precyzyjnie cięte. W procesach cięcia używa się drutu oporowego (dla EPS) lub pił i frezarek (dla XPS), aby uzyskać kształt rdzenia idealnie dopasowany do płyt konstrukcyjnych, często z frezowanymi krawędziami dla połączeń. Dokładność cięcia jest krytyczna, aby nie powstawały mostki termiczne w miejscach łączeń paneli.
Rdzeń poliuretanowy (PUR/PIR) jest zazwyczaj wylewany bezpośrednio między dwiema płytami konstrukcyjnymi lub laminowany na płytach w ciągłym procesie. Wylewanie pianki wymaga kontrolowanych warunków temperatury i wilgotności, aby piana odpowiednio spęczniała i przywarła do płyt na całej powierzchni. Proces ten często odbywa się pod ciśnieniem w prasach, co zapewnia ścisłe wypełnienie przestrzeni i dobre połączenie z płytami.
Kluczową właściwością rdzenia, poza izolacyjnością, jest jego wytrzymałość na ściskanie i zginanie. Chociaż płyty konstrukcyjne przenoszą większość obciążeń, rdzeń izolacyjny również ma w tym swój udział, tworząc strukturę kompozytową. Zapobiega wyboczeniu płyt, a także przenosi siły ścinające w płaszczyźnie panelu. Im większa gęstość izolacji, tym z reguły lepsze są jej właściwości mechaniczne, choć nie jest to jedyny czynnik. Na przykład, specyficzna struktura komórkowa XPS daje mu często lepszą wytrzymałość niż EPS o tej samej gęstości.
Paroprzepuszczalność rdzenia izolacyjnego jest ważnym, choć często pomijanym aspektem. EPS i XPS są stosunkowo paroszczelne, co wymaga odpowiedniego projektowania przegrody budowlanej pod kątem dyfuzji pary wodnej, np. przez zastosowanie folii paroizolacyjnych od strony wewnętrznej. Pianka PUR jest jeszcze bardziej paroszczelna. Właściwe zarządzanie wilgocią w ścianie jest kluczowe, aby zapobiec kondensacji wewnątrz struktury panelu, co mogłoby prowadzić do degradacji materiałów.
Izolacja akustyczna to obszar, w którym standardowe panele SIP, zwłaszcza z rdzeniem EPS, mają pewne ograniczenia w porównaniu do cięższych materiałów, jak mur czy beton. Można jednak poprawić parametry akustyczne, np. przez zastosowanie dodatkowych warstw izolacji akustycznej od wewnątrz (np. wełna mineralna) lub przez użycie rdzeni o lepszych właściwościach tłumiących drgania, choć są one rzadziej spotykane w typowej produkcji SIP. Czasami konieczne jest kreatywne podejście do projektu, aby zapewnić komfort akustyczny mieszkańcom.
Aspekty środowiskowe i zdrowotne związane z materiałami izolacyjnymi są coraz ważniejsze. Nowoczesny EPS i XPS produkowane są bez szkodliwych dla warstwy ozonowej freonów. Pianka PUR również stosuje coraz bardziej ekologiczne czynniki spieniające. Recykling materiałów izolacyjnych, choć technicznie możliwy, wciąż stanowi wyzwanie na dużą skalę. Producenci paneli SIP coraz częściej podkreślają zrównoważony charakter swoich produktów, wynikający z energooszczędności budynku i efektywnego wykorzystania drewna i izolacji.
Na koniec, kluczowa jest jednorodność rdzenia. Izolacja musi idealnie wypełniać przestrzeń między płytami, bez pustek, szczelin czy wtrąceń obcych materiałów. W procesie produkcji paneli EPS/XPS, kontrola jakości skupia się na precyzji cięcia i braku uszkodzeń płyt izolacyjnych. W przypadku pianki wylewanej (PUR), kluczowe jest odpowiednie spienienie materiału i jego całkowite przyleganie do obu płyt na całej powierzchni. To właśnie w tym momencie decyduje się o finalnej izolacyjności i wytrzymałości panelu. Wadliwy rdzeń to jak dziurawy sweter w zimie – ciepło po prostu ucieka.
Rola kleju poliuretanowego w produkcji paneli SIP
Jeśli płyty konstrukcyjne są "kromkami chleba", a izolacja "nadzieniem" w naszej analogii kanapki, to klej poliuretanowy jest sosem, który wszystko spaja, nadając całości niezwykłą integralność. Nie jest to jednak byle jaki sos, a specjalistyczny materiał o kluczowym znaczeniu dla wytrzymałości i trwałości paneli SIP. Jego rola wykracza daleko poza proste "sklejenie". Klej tworzy wiązanie strukturalne, przenoszące naprężenia i siły między płytami a rdzeniem. To jak cement w betonie – bez niego całość nie miałaby siły.
Najczęściej stosowanym rodzajem kleju w produkcji paneli SIP jest jednokomponentowy klej poliuretanowy, utwardzany pod wpływem wilgoci. Kleje dwukomponentowe, wymagające mieszania składników, są również stosowane, zwłaszcza w procesach wymagających bardzo szybkiego utwardzania. Wybór zależy od technologii produkcji i wymagań dotyczących czasu prasowania.
Czym ten klej różni się od zwykłego kleju do drewna? Przede wszystkim, kleje poliuretanowe stosowane w SIP charakteryzują się wysoką wytrzymałością wiązania na ścinanie, zginanie i rozciąganie. Potrafią tworzyć bardzo trwałe połączenia pomiędzy różnymi materiałami – drewnopochodnymi płytami a spienionym polistyrenem czy pianką poliuretanową. Co więcej, mają zdolność do delikatnego spieniania podczas utwardzania, co pozwala na wypełnienie drobnych nierówności na powierzchniach łączonych materiałów, zapewniając maksymalną powierzchnię kontaktu i optymalne przyleganie. To jak inteligentna uszczelka, która idealnie dopasowuje się do każdego kształtu.
Proces aplikacji kleju jest precyzyjnie kontrolowany. W nowoczesnych liniach produkcyjnych odbywa się to automatycznie, za pomocą systemów natryskowych lub specjalnych wałków nakładających równomierną warstwę kleju na powierzchnię płyt lub rdzenia. Ilość nakładanego kleju jest ściśle dozowana – zbyt mało może skutkować słabym wiązaniem, zbyt dużo to niepotrzebne koszty i ryzyko wycieków poza obręb panelu. Typowa ilość kleju nakładana na 1 m² powierzchni wynosi od 150 do 300 gramów, w zależności od specyfikacji kleju i porowatości powierzchni.
Wilgoć jest niezbędnym aktywatorem dla jednokomponentowych klejów poliuretanowych. Często przed nałożeniem kleju, powierzchnie materiałów (zwłaszcza płyt OSB) są delikatnie zraszane wodą, aby zapewnić optymalne warunki do utwardzenia kleju. Zbyt niska wilgotność spowolni proces utwardzania, zbyt wysoka może wpłynąć na strukturę spienionego kleju. Kontrola warunków środowiskowych w hali produkcyjnej jest więc istotna. Jak w laboratorium, liczy się każda zmienna.
Po nałożeniu kleju i złożeniu panelu, kluczowy jest proces prasowania. Panel umieszcza się w prasie, która wywiera równomierny nacisk na całą powierzchnię. Ciśnienie to jest niezbędne do zapewnienia pełnego kontaktu kleju z obiema powierzchniami płyt i rdzenia oraz do skompensowania sił rozporu powstających podczas delikatnego spieniania kleju. Typowe ciśnienie prasowania może wynosić od 0.1 do 0.5 bara, choć dokładne wartości zależą od typu kleju i paneli. Czas prasowania, czyli czas, przez który panel pozostaje pod naciskiem w celu utwardzenia kleju, waha się od kilkunastu minut do kilku godzin, zależnie od rodzaju kleju, wilgotności i temperatury.
Systemy prasowania są różne: od prostych pras pneumatycznych czy hydraulicznych, po zaawansowane prasy próżniowe, które usuwają powietrze spomiędzy warstw i zapewniają bardzo równomierne ciśnienie. Prasy próżniowe są szczególnie efektywne, gwarantując doskonałe przyleganie kleju na całej powierzchni i minimalizując ryzyko wystąpienia pustek powietrznych, które mogłyby osłabić wiązanie. Jakość procesu prasowania jest bezpośrednio widoczna w końcowej wytrzymałości paneli. Słabo sprasowany panel jest po prostu... wiotki. A to oznacza kłopoty na budowie.
Temperatura w procesie utwardzania również odgrywa ważną rolę. Ciepło przyspiesza reakcję chemiczną utwardzania poliuretanu. W niektórych liniach produkcyjnych stosuje się podgrzewane prasy lub kontroluje temperaturę w hali produkcyjnej, aby zoptymalizować czas cyklu produkcyjnego. To pozwala na szybsze wytwarzanie gotowych paneli.
Kontrola jakości wiązania klejowego jest etapem, którego żaden szanujący się producent nie może pominąć. Odbywa się to często poprzez wyrywkowe badania próbek paneli, polegające na testowaniu wytrzymałości na rozwarstwianie (delamination test). Specjalistyczne maszyny próbują rozdzielić płyty od rdzenia, a mierzona siła pozwala ocenić jakość wiązania. Normy określają minimalną wymaganą wytrzymałość, której gotowy panel musi sprostać. To swoisty egzamin dojrzałości dla panelu – czy poradzi sobie pod obciążeniem?
Trwałość wiązania poliuretanowego w długim okresie eksploatacji budynku jest bardzo wysoka. Kleje te są odporne na starzenie, zmienne warunki temperaturowe, wilgoć i typowe czynniki chemiczne, z jakimi mają do czynienia w konstrukcji ściany czy dachu. Prawidłowo wykonane połączenie klejowe powinno zachować swoje właściwości przez dziesiątki lat, czyli przez cały okres użytkowania budynku. Producent kleju również dostarcza certyfikaty i testy długoterminowej odporności, ale kluczem jest prawidłowe zastosowanie w fabryce. Nawet najlepszy klej nie zadziała, jeśli jest źle nałożony lub sprasowany. Taka jest proza produkcji.
Zużycie kleju na panel zależy od jego rozmiaru i powierzchni klejenia. Dla panelu o standardowych wymiarach np. 1,2m x 2,8m, powierzchnia do klejenia po obu stronach rdzenia wynosi około 6,72 m². Przy założeniu zużycia 200 g/m², na jeden panel zużywa się około 1,34 kg kleju. W skali produkcji, gdzie dziennie wytwarza się setki takich paneli, zapotrzebowanie na klej jest ogromne. Logistyka dostaw i magazynowania kleju w beczkach czy zbiornikach IBC jest ważną częścią zarządzania produkcją.
Koszt kleju poliuretanowego stanowi znaczącą pozycję w kosztorysie produkcji panelu SIP, obok kosztów płyt i izolacji. Jego cena jednostkowa za kilogram jest znacznie wyższa niż cena bazowych surowców jak styropian czy OSB, dlatego optymalizacja zużycia kleju, przy zachowaniu jakości, jest celem każdego producenta. Jest to jednak koszt uzasadniony, bo bez tego kluczowego spoiwa, panele straciłyby swoje unikalne właściwości strukturalne i izolacyjne. Innymi słowy, na kleju nie warto oszczędzać, jeśli chce się zbudować coś, co przetrwa lata. Jest to jeden z tych "niewidzialnych" komponentów, który decyduje o wszystkim.
Rynek klejów poliuretanowych dla paneli SIP jest zdominowany przez kilku dużych producentów chemicznych, którzy oferują specjalistyczne produkty dopasowane do różnych technologii produkcji i materiałów rdzeniowych. Współpraca z renomowanym dostawcą kleju, który oferuje wsparcie techniczne i pewność jakości partii produkcyjnych, jest ważna dla producenta paneli SIP. Zła partia kleju może zniweczyć cały proces produkcyjny i zagrażać reputacji. To biznes, w którym zaufanie do dostawców surowców buduje się latami, a weryfikuje przy każdym nowym projekcie. Takie partnerstwo to podstawa w świecie produkcji zaawansowanych materiałów budowlanych.
Proces produkcji paneli SIP: Od łączenia do gotowego modułu
Samo wyprodukowanie pojedynczego panelu SIP to dopiero początek drogi do postawienia domu. Klucz do skuteczności systemu SIP tkwi w integracji produkcji paneli z całym procesem budowy. Produkcja panelu w kontrolowanych warunkach fabrycznych to złożony ciąg operacji, gdzie precyzja jest absolutnie krytyczna. Nie ma tu miejsca na "oko metra" czy luźne interpretacje rysunku. W fabryce każde cięcie i każde klejenie musi być wykonane z zegarmistrzowską dokładnością. To proces, w którym nowoczesna technologia spotyka tradycyjne rzemiosło w nowym wydaniu.
Proces rozpoczyna się od przyjęcia i kontroli jakości surowców: płyt konstrukcyjnych (np. OSB), bloków lub płyt izolacyjnych (EPS, XPS) lub chemikaliów do spieniania (PUR/PIR) oraz kleju. Materiały muszą spełniać określone normy i posiadać odpowiednie certyfikaty. Płyty drewnopochodne są sprawdzane pod kątem wilgotności, uszkodzeń mechanicznych i wymiarów. Izolacja kontrolowana jest pod kątem gęstości i regularności kształtu. Klej ma swoją datę ważności i wymaga odpowiednich warunków przechowywania, zazwyczaj w stałej, chłodnej temperaturze, aby zachować swoje właściwości przed użyciem. To etap, na którym "szpiedzy jakości" pracują na pełnych obrotach, wychwytując potencjalne problemy zanim trafią na linię produkcyjną. Czy kiedykolwiek zastanawiałeś się, ile kontroli przechodzi deska zanim trafi do tartaku? Tutaj jest ich o wiele więcej!
Następnie surowce są przygotowywane do dalszej obróbki. Płyty konstrukcyjne są przycinane na wymiar za pomocą pił tarczowych lub paneli frezarek CNC zgodnie z projektem budynku, który jest wprowadzany do systemu sterowania maszyną. Frezarki CNC potrafią wycinać złożone kształty, otwory na okna i drzwi z niezwykłą precyzją, minimalizując odpady. Jednocześnie rdzeń izolacyjny (blok EPS/XPS) jest cięty na mniejsze płyty o odpowiedniej grubości, a następnie formatowany, często z wyfrezowanymi wpustami na krawędziach. W przypadku pianki PUR/PIR przygotowuje się system dozujący składniki chemiczne.
Kluczowym etapem jest aplikacja kleju. Odbywa się to na czystej, odtłuszczonej powierzchni płyt lub rdzenia. W pełni zautomatyzowanych liniach klej jest natryskiwany przez robota lub przechodzi przez system wałków, który nanosi jednolitą warstwę. Równomierne pokrycie jest absolutnie niezbędne dla trwałości wiązania. Niewystarczająca ilość kleju lub nierównomierne pokrycie może prowadzić do tzw. "suchych plam", czyli obszarów, gdzie wiązanie nie jest wystarczająco silne. To prosta, ale niezwykle ważna czynność. Pomyśl o przyklejaniu tapety - jeden bąbel powietrza potrafi zepsuć cały efekt, a tu mowa o wytrzymałości strukturalnej.
Po nałożeniu kleju następuje składanie panelu. Rdzeń izolacyjny jest starannie układany na dolnej płycie konstrukcyjnej, a następnie wierzchnia płyta jest umieszczana na wierzchu, tworząc "kanapkę". W procesie produkcji paneli PUR/PIR, płynne składniki chemiczne są wylewane między płytami, które są już w prasie, a następnie reagują i spieniają się, wypełniając przestrzeń i przywierając do płyt pod ciśnieniem. Montaż musi odbywać się szybko, zanim klej zacznie twardnieć (tzw. czas otwarty kleju).
Złożony panel jest następnie transportowany do prasy. Jak już wspomniano, prasa wywiera stały, równomierny nacisk na całą powierzchnię panelu przez określony czas (czas prasowania/utwardzania). To etap, w którym klej wiąże warstwy, tworząc kompozytową strukturę. Odpowiednie ciśnienie i czas prasowania są kluczowe dla uzyskania pełnej wytrzymałości panelu. W tym czasie personel produkcji często zajmuje się przygotowaniem kolejnych elementów lub obróbką wstępną. To jak poczekalnia dla paneli – cichy moment przed wyjściem w świat budownictwa.
Po wyjęciu z prasy, utwardzony panel może wymagać dodatkowej obróbki. Krawędzie są przycinane na czysto, usuwa się ewentualne wypływki kleju. Na krawędziach paneli przeznaczonych do łączenia ze sobą lub z elementami konstrukcji (drewniane słupki, specjalne splajny) frezuje się odpowiednie rowki. Precyzyjne frezowanie krawędzi gwarantuje idealne spasowanie paneli na budowie, eliminując mostki termiczne i konstrukcyjne. Wyobraź sobie, jak frustrujące byłoby, gdyby panele nie pasowały do siebie podczas montażu! Dlatego ten etap jest tak ważny.
Każdy wyprodukowany panel powinien przejść kontrolę jakości. Obejmuje ona sprawdzenie wymiarów panelu (długość, szerokość, grubość), płaskości powierzchni, jakości frezowania krawędzi, a także wizualną ocenę połączenia klejowego i braków w izolacji. Poważni producenci często numerują panele zgodnie z projektem montażowym, co ułatwia pracę na budowie. Wyrywkowe testy wytrzymałościowe (np. test na rozwarstwianie) są również przeprowadzane regularnie, aby monitorować stałość procesu produkcji. To jak laboratoryjne badanie krwi przed ważnym meczem – trzeba upewnić się, że wszystko jest w najlepszym porządku.
Po przejściu kontroli jakości panele są grupowane zgodnie z projektem, odpowiednio pakowane i przygotowywane do wysyłki. Często stosuje się foliowanie, które chroni panele przed wilgocią i uszkodzeniami podczas transportu. Panel SIP jest produktem gotowym do montażu bezpośrednio na budowie, co znacznie skraca czas realizacji inwestycji. Jest to jedna z największych przewag tej technologii – elementy składowe domu przyjeżdżają w zasadzie gotowe do złożenia. Nie trzeba czekać na wiązanie zaprawy, wysychanie tynków czy układanie każdej cegły osobno.
Automatyzacja odgrywa kluczową rolę w nowoczesnych fabrykach paneli SIP. Zaawansowane maszyny sterowane komputerowo minimalizują błędy ludzkie, przyspieszają produkcję i zapewniają powtarzalną, wysoką jakość. Roboty aplikujące klej, precyzyjne piły i frezarki CNC, automatyczne systemy prasowania – to wszystko elementy współczesnej linii produkcyjnej SIP. Inwestycja w nowoczesny park maszynowy jest znacząca, ale zwraca się poprzez zwiększoną wydajność i niezawodność produktu.
Wydajność typowej, nowoczesnej linii produkcyjnej paneli SIP może sięgać kilkuset, a nawet kilku tysięcy metrów kwadratowych paneli dziennie, w zależności od stopnia automatyzacji i specyfiki produkcji. To pozwala na szybkie zaspokojenie potrzeb rynku i skrócenie czasu oczekiwania na zamówione panele. Logistyka w takim przypadku staje się osobnym wyzwaniem – trzeba efektywnie zarządzać dostawami surowców i wysyłką gotowych produktów na place budowy rozproszone po całym kraju lub kontynencie. To logistyczny taniec precyzji.
Ekologiczne aspekty produkcji obejmują minimalizację odpadów, optymalizację zużycia energii i, w miarę możliwości, wykorzystanie materiałów pochodzących z recyklingu lub odnawialnych źródeł. Odpady z produkcji, np. ścinki płyt OSB czy styropianu, mogą być gromadzone i w niektórych przypadkach poddawane recyklingowi. Wybór materiałów izolacyjnych z bardziej ekologicznymi czynnikami spieniającymi również jest krokiem w kierunku zrównoważonej produkcji. Takie działania nie tylko są korzystne dla środowiska, ale także budują pozytywny wizerunek firmy i odpowiadają na rosnące oczekiwania rynku w zakresie "zielonego" budownictwa. Bo w końcu kto by nie chciał mieszkać w domu, który powstał w sposób przyjazny dla Planety?
Całość procesu produkcyjnego paneli SIP jest stale monitorowana i doskonalona. Technologie materiałowe rozwijają się, pojawiają się nowe rodzaje klejów, udoskonalane są metody aplikacji. Producenci SIP, którzy inwestują w badania i rozwój, utrzymują przewagę konkurencyjną. Testowanie nowych surowców, optymalizacja parametrów prasowania czy wdrażanie innowacyjnych systemów kontroli jakości to ciągła praca. To trochę jak tuningowanie samochodu – zawsze znajdzie się coś do poprawienia, żeby było szybciej, lepiej i efektywniej.
Podsumowując, SIP powstaje bowiem poprzez złączenie starannie dobranych surowców w precyzyjnie kontrolowanym procesie, który zmienia je w zaawansowane moduły budowlane. Od dokładnego cięcia płyt i izolacji, przez precyzyjne nanoszenie kleju, po odpowiednie prasowanie i kontrolę jakości, każdy etap ma znaczenie dla końcowych właściwości paneli. Jest to produkcja przemysłowa, która wymaga inwestycji w technologię i ludzi, ale dostarcza na rynek produkt o rewolucyjnym potencjale. Taki panel, choć prosty w idei "kanapki", jest owocem zaawansowanej myśli technicznej i procesowej. To fascynujące, jak z kilku podstawowych materiałów, dzięki technologii i precyzji, można stworzyć element, który definiuje przyszłość budownictwa energooszczędnego.
Jako ciekawostka, zastanówmy się nad jednym z największych wyzwań produkcji paneli SIP z dużymi otworami na okna lub drzwi. Rdzeń izolacyjny i płyty są odpowiednio wycinane, ale wewnątrz panelu wokół otworu często umieszcza się drewniane elementy szkieletu (np. belkę nadprożową, słupki), które są integralną częścią struktury. Wbudowanie tych elementów w panel w fabryce wymaga precyzyjnego pasowania i klejenia również tych elementów. To dodaje kolejną warstwę złożoności do procesu produkcyjnego i wymaga jeszcze większej dokładności w wycinaniu. Panel z fabrycznie wbudowaną konstrukcją okna to w zasadzie gotowy fragment ściany, co jest niesamowitym ułatwieniem na budowie, ale zwiększa wymagania stawiane producentowi. W końcu każdy "otwór" to potencjalne miejsce na błąd – trzeba je wyprodukować perfekcyjnie.