Jak sprawdzić czy panel fotowoltaiczny jest sprawny? Kompletny poradnik 2025
Fotowoltaika, wykorzystująca energię słoneczną do produkcji prądu elektrycznego, stała się jednym z najpopularniejszych rozwiązań w dziedzinie energii odnawialnej. Pozwala ona uniezależnić się od rosnących cen prądu i zadbać o planetę. Naturalnym pytaniem, które się pojawia, jest zatem Jak sprawdzić czy panel fotowoltaiczny jest sprawny w praktyce, w zmieniających się warunkach atmosferycznych? Krótko mówiąc, Jak sprawdzić czy panel fotowoltaiczny jest sprawny - polega na ocenie jego stanu fizycznego, przeprowadzeniu precyzyjnych pomiarów elektrycznych oraz dogłębnej analizie danych z monitoringu instalacji w kontekście wpływu środowiska.
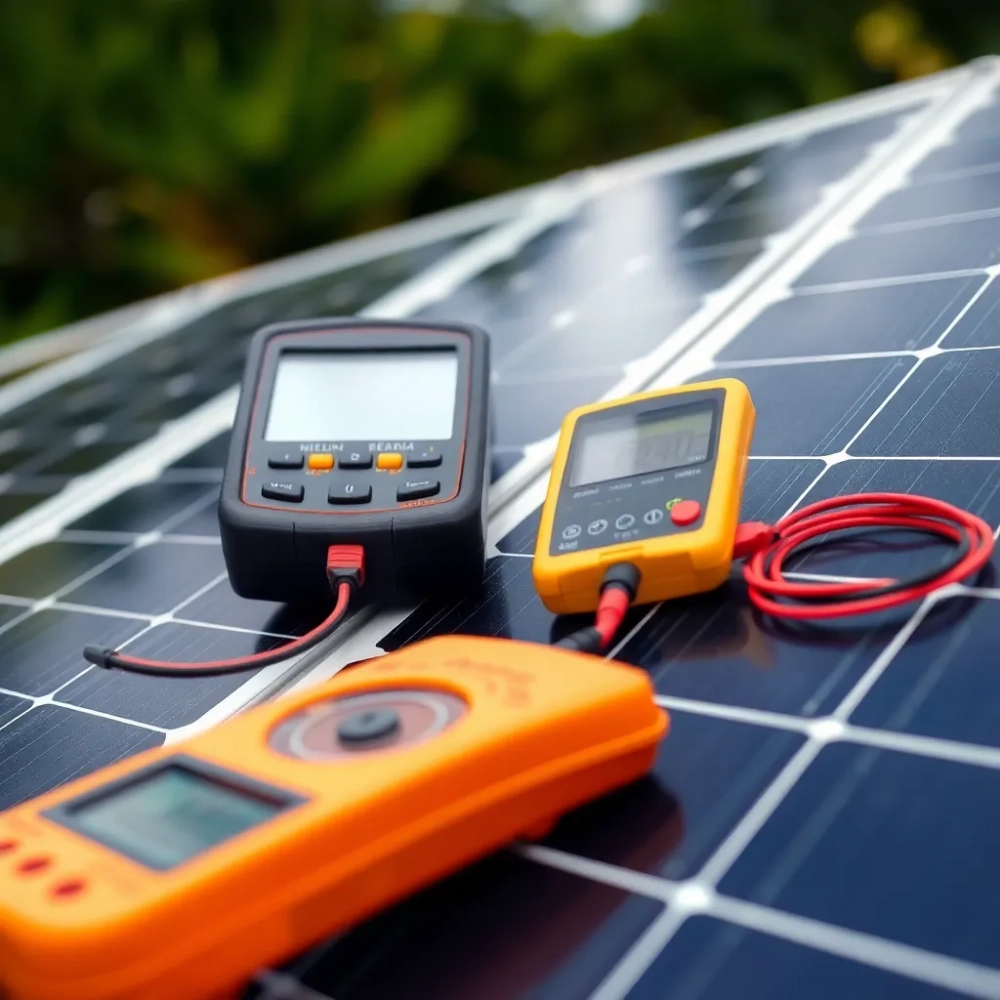
Rozumienie, co wpływa na faktyczną wydajność paneli fotowoltaicznych, jest kluczowe dla oceny ich stanu. To nie tylko idealne warunki laboratoryjne decydują o efektywności w terenie.
Na sprawność, czyli zdolność przetwarzania energii słonecznej, ma wpływ całe spektrum czynników – od detali konstrukcyjnych po zanieczyszczenia. Dane techniczne często podają parametry w standardowych warunkach testowych, które rzadko występują na co dzień.
Wydajność panelu nie jest prostą pochodną jego mocy nominalnej; panel o mocy 550 W może mieć niższą sprawność procentową niż ten o mocy 350 W, ponieważ moc zależy także od fizycznej wielkości modułu. Kluczowe są parametry charakteryzujące zachowanie panelu, takie jak wskaźniki STC i NOCT.
Wskaźnik | Warunki testowe | Znaczenie |
---|---|---|
STC (Standard Test Conditions) | Promieniowanie 1000 W/m², Temperatura ogniwa 25°C, Widmo AM1.5 | Standard laboratoryjny, baza danych technicznych (np. moc nominalna) |
NOCT (Nominal Operating Cell Temperature) | Promieniowanie 800 W/m², Temperatura otoczenia 20°C, Wiatr 1 m/s | Warunki bliższe rzeczywistości (temperatura ogniwa zwykle > 20°C otoczenia), daje lepsze wyobrażenie o typowej pracy |
Analiza powyższych wskaźników i danych jest fundamentem, zanim przejdziemy do fizycznej kontroli czy pomiarów w terenie.
Pozwala zorientować się, czego realistycznie oczekiwać od naszego systemu w konkretnych warunkach pracy, a nie tylko w idealnym laboratorium. Dopiero wtedy można sensownie ocenić, czy panele faktycznie działają prawidłowo, czy też coś nie gra.
Ocena stanu fizycznego panelu fotowoltaicznego
Zacznijmy od najbardziej podstawowej, a często pomijanej czynności – oględzin wizualnych. Panele słoneczne, choć wydają się solidne, są narażone na wiele czynników środowiskowych, które mogą pozostawić widoczne ślady.
Pierwsze na liście kontrolnej powinny być szyba i rama. Poszukujemy pęknięć, odprysków, odkształceń ramy czy problemów z uszczelnieniem. Nawet niewielkie uszkodzenie szyby może prowadzić do zawilgocenia wewnątrz laminatu i nieodwracalnych uszkodzeń ogniw.
Zwróć uwagę na tył panelu – na folię lub szkło tylne (backsheet). Sprawdź, czy nie ma pęcherzyków powietrza, przebarwień (szczególnie brązowych czy żółtych) lub widocznych uszkodzeń mechanicznych, które mogą świadczyć o degradacji materiału.
Obserwuj również puszkę przyłączeniową na tyle panelu. Czy jest szczelnie zamknięta? Czy widać jakiekolwiek ślady przegrzewania, np. topienia się plastiku wokół dławików kablowych lub samych przewodów?
Stan kabli i konektorów (złącz MC4) również jest krytyczny. Izolacja kabli powinna być nienaruszona, a konektory czyste, suche i pewnie połączone. Złe styki to częsta przyczyna strat mocy i potencjalne zagrożenie pożarowe.
Typowym problemem są "ślady ślimaków" (snail trails) – ciemne, smugowate wzory pojawiające się pod szkłem. Choć nazwa sugeruje coś innego, są to często objawy mikropęknięć lub reakcji chemicznych w obrębie ogniw, mogące prowadzić do degradacji.
Poważnym sygnałem ostrzegawczym są hot spoty, czyli przegrzewające się punkty na panelu. Niewidoczne gołym okiem, wymagają kamery termowizyjnej. Mogą być spowodowane zacienieniem pojedynczego ogniwa, mikropęknięciami lub problemami produkcyjnymi i znacząco obniżają wydajność, grożąc nawet pożarem.
Zabrudzenia to najbardziej oczywisty problem fizyczny. Kurz, ptasie odchody, liście, a nawet osady z pyłków roślinnych potrafią zasłonić znaczną część powierzchni aktywnej, blokując dostęp światła słonecznego. Kilogramy kurzu mogą zebrać się na dużych farmach PV, redukując uzysk o zaskakująco duży procent.
Przykładowo, pojedynczy, dobrze wymierzony "prezent" od ptaka na kluczowym ogniwie może obniżyć wydajność całego łańcucha modułów nawet o 20-30% w skrajnych przypadkach. Regularne czyszczenie paneli fotowoltaicznych, zwłaszcza w suchym klimacie, to podstawa.
Zabrudzenia mogą również tworzyć idealne warunki do rozwoju mchu czy porostów na ramie i krawędziach panelu, co może prowadzić do gromadzenia wilgoci i dalszej degradacji strukturalnej. Patrzenie na panele z góry, zwłaszcza tych zamontowanych na dachu, wymaga odpowiednich środków ostrożności, ale daje pełniejszy obraz.
Warto pamiętać, że producenci udzielają gwarancji na panele, często dwutorowych: na wykonanie (np. 10-15 lat) i na uzysk mocy (np. gwarancja liniowa na 25 lat, zapewniająca minimum 80-85% mocy początkowej po tym czasie). Uszkodzenia fizyczne zazwyczaj podpadają pod gwarancję na wykonanie.
Podsumowując wizualną inspekcję – to trochę jak badanie lekarskie. Szukamy widocznych objawów problemów, które mogą wskazywać na głębsze schorzenia wpływające na pracę panelu i całej instalacji. Profesjonalne firmy przeprowadzają takie kontrole w ramach przeglądów, często z użyciem dronów i kamer termowizyjnych.
Pomiary elektryczne: Napięcie, prąd i moc panelu PV
Oględziny to jedno, ale rzeczywistość pracy panelu objawia się w prądzie i napięciu, jakie jest w stanie wygenerować. Pomiary elektryczne są kluczowym krokiem w ocenie sprawności, pozwalającym zajrzeć "pod maskę" systemu.
Najprostsze pomiary wykonuje się zwykłym multimetrem, ale dają one tylko częściowy obraz. Możemy zmierzyć napięcie obwodu otwartego (Voc - Voltage open circuit) oraz prąd zwarcia (Isc - Current short circuit).
Voc mierzymy, gdy panel nie jest podłączony do żadnego obciążenia (np. odpinając go od inwertera). Multimetr pokazuje wtedy maksymalne napięcie, jakie panel jest w stanie wyprodukować. Porównujemy je z danymi na tabliczce znamionowej panelu i w karcie katalogowej, uwzględniając temperaturę – niższa temperatura ogniwa zwiększa Voc.
Isc mierzymy, gdy prąd przepływa przez bardzo niską rezystancję (czyli „zwarcie”). W praktyce używa się specjalnych adapterów lub mierników do PV, które bezpiecznie realizują to "zwarcie" poprzez wbudowany rezystor. Wyższa irradiancja (nasłonecznienie) i niższa temperatura wpływają na Isc.
Należy jednak pamiętać, że ani sam Voc, ani sam Isc nie mówią nam bezpośrednio o mocy, jaką panel może wyprodukować w rzeczywistych warunkach pracy. Pełny obraz daje pomiar punktu mocy maksymalnej (MPP - Maximum Power Point).
Panel fotowoltaiczny działa najbardziej efektywnie w konkretnym punkcie charakterystyki prądowo-napięciowej (krzywa I-V), zwanym punktem mocy maksymalnej. To iloczyn napięcia (Vmpp) i prądu (Impp) w tym punkcie daje maksymalną moc (Pmp = Vmpp * Impp).
Aby zmierzyć MPP, potrzebne jest specjalistyczne urządzenie – analizator charakterystyk I-V (kurwiomierz). Analizator na chwilę obciąża panel zmienną rezystancją, rejestrując napięcie i prąd, tworząc pełną krzywą I-V. Następnie oblicza Pmp.
Zmierzona moc Pmp musi być porównana z wartością nominalną podaną przez producenta, korygując o aktualne warunki pomiaru: temperaturę ogniwa i irradiancję. Dobre analizatory mają czujniki temperatury i promieniowania i automatycznie przeliczają wynik do warunków STC.
Przyjmuje się, że nowy panel powinien produkować moc równą lub nieznacznie wyższą od Pmp STC podanej na tabliczce, gdy zmierzymy go w warunkach bliskich STC (skorygowanych). Spadek mocy w porównaniu do danych katalogowych (skorygowanych) wskazuje na problem z panelem.
Degradacja paneli postępuje z czasem. Typowy panel monokrystaliczny ma gwarancję na spadek mocy liniowy, np. nie więcej niż 0.5% rocznie. Po 10 latach powinien zachować co najmniej 95% mocy nominalnej, a po 25 latach 85%.
Jeśli pomiary elektryczne wykazują, że panel znacznie odbiega od oczekiwanych wartości dla swojego wieku, po uwzględnieniu warunków pomiaru, jest to silny sygnał wskazujący na jego uszkodzenie lub znaczną degradację przekraczającą normy. Może to być podstawą do roszczeń gwarancyjnych.
Pamiętajmy, że pomiary elektryczne powinny być wykonywane przy odpowiednim nasłonecznieniu (minimum 400-500 W/m², najlepiej powyżej 800 W/m²), aby były miarodajne. Mierzenie w pochmurny dzień da niskie wartości prądu, co niekoniecznie świadczy o niesprawności panelu.
Co wpływa na zmierzoną sprawność paneli (Temperatura, zabrudzenie, zacienienie)
Zmierzone parametry elektryczne panelu są jedynie migawką jego wydajności w danej chwili. Ta "chwila" jest pod silnym wpływem otoczenia. Pomyśl o tym jak o sportowcu – jego "sprawność" zmierzona na bieżni zależy nie tylko od jego formy, ale i od temperatury powietrza, wiatru czy nawet jakości nawierzchni.
Temperatura to wróg numer jeden dla krzemu. Wbrew intuicji, panele PV działają lepiej w chłodne, słoneczne dni niż w upalne lato. Gdy temperatura ogniwa przekracza 25°C (warunek STC), moc wyjściowa panelu zaczyna spadać.
Każdy panel ma podany współczynnik temperaturowy mocy (często w %/°C). Typowe wartości dla paneli krystalicznych to od -0.35% do -0.45% na stopień Celsjusza powyżej 25°C. Oznacza to, że wzrost temperatury ogniwa o każde 10°C ponad 25°C spowoduje spadek mocy o 3.5% do 4.5%.
W słoneczny dzień na dachu ogniwo może osiągnąć temperaturę nawet 50-60°C, a w ekstremalnych warunkach więcej. Przy temperaturze ogniwa 55°C (czyli 30°C powyżej STC), panel o współczynniku -0.40%/°C straci około 30 * 0.40% = 12% swojej mocy nominalnej.
Zabrudzenie, choć może brzmi banalnie, to potężny reduktor wydajności. Warstwa kurzu, pyłków z pobliskich pól, liści czy sadzy kominowej działa jak filtr, zmniejszając ilość światła docierającego do ogniw.
Straty mocy z powodu zabrudzenia (soiling) mogą sięgać kilku procent rocznie, a w obszarach przemysłowych, w pobliżu ruchliwych dróg, w klimacie suchym lub na farmach ptactwa nawet 15-20%, jeśli panele nie są regularnie czyszczone.
Zacienienie, nawet częściowe, potrafi być najbardziej destrukcyjnym czynnikiem. Pojedyncze zacienione ogniwo w stringu (szeregu połączonych paneli) zachowuje się jak opornik. Ponieważ prąd w szeregu musi być wszędzie taki sam, inwerter obniża prąd całego stringu do poziomu tego zacienionego ogniwa.
W nowoczesnych panelach stosuje się diody bocznikujące (bypass diodes), które w teorii pozwalają "ominąć" zacienioną sekcję panelu, ratując resztę. Niestety, to rozwiązanie zmniejsza straty, ale nie eliminuje ich całkowicie, a diody bocznikujące mogą stać się źródłem hot spotów, jeśli są nadmiernie obciążone przez długotrwałe zacienienie.
Częściowe zacienienie od komina, drzewa, anteny satelitarnej czy nawet opadłych liści rzucane przez tylko część dnia potrafią obniżyć całkowity uzysk energii w skali roku o zaskakująco dużo. Warto walczyć o każdy promień słońca.
Inne czynniki zewnętrzne to orientacja i kąt nachylenia paneli, które determinują ilość docierającego promieniowania w ciągu dnia i roku. Również jakość i typ paneli (monokrystaliczne są zazwyczaj wydajniejsze i lepiej radzą sobie z temperaturą niż polikrystaliczne czy cienkowarstwowe) ma fundamentalne znaczenie.
Czynniki wewnętrzne, jak solidność producenta i zastosowana technologia ogniw, decydują o nominalnej sprawności i tempie degradacji w czasie. Chiński panel za pół ceny może wyglądać identycznie, ale jego sprawność może być niższa, a degradacja szybsza niż u renomowanego producenta. Czasem płacisz więcej za niewidzialną jakość i trwałość.
Wykres powyżej ilustruje typowy wpływ temperatury na szacowaną moc wyjściową panelu – widzisz, jak szybko może spadać w gorące dni, co pokazuje, że nominalna moc to tylko punkt odniesienia.
Jak interpretować dane z systemu monitorowania instalacji
Większość nowoczesnych instalacji fotowoltaicznych wyposażona jest w system monitorowania. To jest twój najlepszy przyjaciel w codziennym życiu z fotowoltaiką. Dostęp do danych, często przez aplikację mobilną lub platformę webową, pozwala śledzić pracę systemu w czasie rzeczywistym i historycznie.
Co możemy tam zobaczyć? Kluczowe metryki to aktualna moc generowana przez całą instalację lub poszczególne stringi/panele, dzienna, miesięczna i roczna produkcja energii (w kWh), a często także szacowane oszczędności lub uniknięta emisja CO2.
Analiza tych danych pozwala szybko zauważyć odchylenia od normy. Oczekujemy płynnego wykresu produkcji mocy w ciągu dnia, z pikiem w okolicach południa (lub zależnie od orientacji dachu i pory roku). Każde wyraźne załamanie lub spadek mocy na wykresie w idealnie słoneczny dzień to sygnał do zbadania.
Porównanie produkcji z poprzednimi dniami lub z innymi instalacjami w podobnej lokalizacji może wskazać, czy problem leży po stronie pogody (np. chwilowe zachmurzenie), czy czegoś innego.
Nowoczesne inwertery często posiadają monitoring na poziomie stringu. Niektóre systemy, szczególnie z optymalizatorami mocy lub mikroinwerterami, oferują monitoring na poziomie pojedynczego panelu.
Ten panelowy monitoring jest super potężnym narzędziem. Pozwala wskazać konkretny moduł lub kilka modułów, które generują mniej mocy niż sąsiednie w tych samych warunkach. To jak znalezienie "czarnej owcy" w stadzie.
Załóżmy, że monitoring pokazuje, że jeden panel generuje 50W mocy w słoneczne południe, podczas gdy sąsiednie, identyczne panele produkują 350W. Co to może oznaczać? Prawdopodobnie ten konkretny panel ma problem.
Może być zacieniony (przez komin, liść, ptasie gniazdo?), może ma fizyczne uszkodzenie niewidoczne z ziemi, może problem leży w złączu, diodzie bocznikującej lub samym ogniwie. Monitoring kieruje naszą uwagę w konkretne miejsce.
System monitorowania często wysyła alerty e-mailowe lub powiadomienia w aplikacji, gdy wykryje problem, np. awarię inwertera, błąd uziemienia, zbyt niską produkcję. Nie ignoruj tych powiadomień – one ratują uzysk.
Analizując dane długoterminowo, możemy ocenić rzeczywistą wydajność systemu w stosunku do oczekiwań i przewidywanej produkcji. Systemy monitorowania często mają narzędzia do porównywania aktualnego uzysku z modelem teoretycznym.
Ważnym aspektem jest też kontrola napięć i prądów stringów (jeśli monitoring na to pozwala). Nienaturalne wartości mogą wskazywać na problem z połączeniem, uszkodzenie paneli w stringu lub problem z samym inwerterem.
Pamiętaj, że dane z monitoringu to wskaźnik, nie zawsze ostateczna diagnoza. Jeśli dane sugerują problem z konkretnym panelem, konieczna jest weryfikacja na miejscu: inspekcja wizualna i ewentualnie pomiary elektryczne tego panelu. Ale przynajmniej wiesz, gdzie szukać.
Dobrze skonfigurowany system monitorowania i regularne sprawdzanie danych to najlepsza strategia proaktywnego zarządzania instalacją fotowoltaiczną. To tak jak deska rozdzielcza w samochodzie – dostarcza informacji, które pozwalają zapobiegać awariom lub szybko reagować, gdy coś się dzieje.