Jak przygotować posadzkę pod ogrzewanie podłogowe – poradnik 2025
Wyobraź sobie ciepło otulające stopy, subtelnie rozchodzące się po całym pomieszczeniu – to obietnica ogrzewania podłogowego. Aby jednak ta wizja stała się rzeczywistością bez przykrych niespodzianek, kluczowe jest zrozumienie, jak przygotować posadzkę pod ogrzewanie podłogowe. W największym skrócie, ten proces wymaga idealnie przygotowanego, suchego podłoża, właściwej izolacji przeciwwilgociowej i termicznej, precyzyjnego ułożenia instalacji grzewczej oraz poprawnego wykonania warstwy jastrychu z dylatacjami.
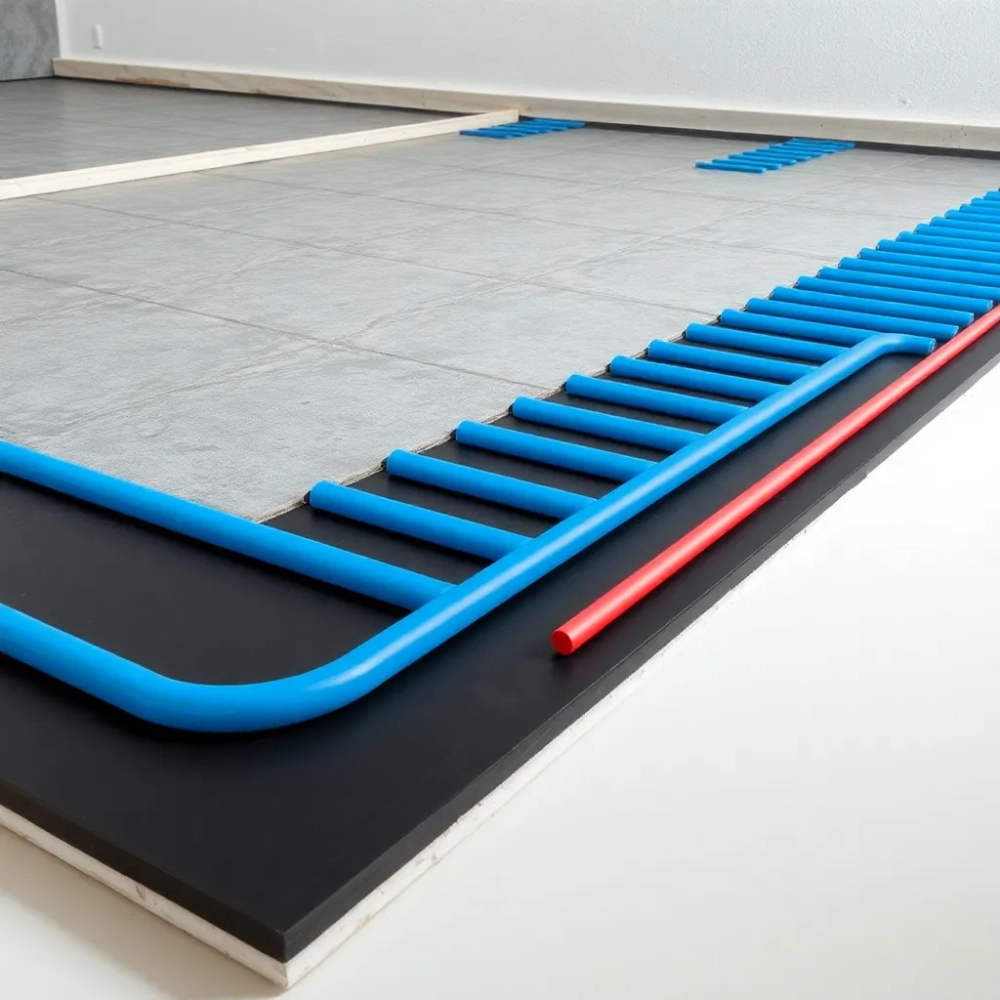
Z perspektywy kompleksowej analizy wyzwań związanych z instalacją ogrzewania podłogowego, kluczowe etapy przygotowania podłoża jawią się jako fundament sukcesu całego przedsięwzięcia. Problemy napotkane na tym wczesnym etapie – jak niedostateczna suchość czy brak odpowiedniej izolacji – mogą prowadzić do poważnych konsekwencji, od strat ciepła po uszkodzenia samej konstrukcji podłogi czy nawet rozwój mikroorganizmów. Dostępne dane z placów budowy i audytów energetycznych konsekwentnie wskazują, że precyzyjne przestrzeganie norm i zaleceń technologicznych na etapie przygotowania podłoża jest znacznie bardziej kosztowo efektywne niż późniejsze naprawy.
Ta skrupulatność w przygotowaniu podłoża to nie tylko kwestia uniknięcia potencjalnych kosztów, ale przede wszystkim zapewnienia optymalnej wydajności i długowieczności systemu grzewczego. Właściwie zaizolowana i wyrównana posadzka pozwala ciepłu wędrować dokładnie tam, gdzie chcemy – w górę, do pomieszczenia, a nie uciekać w głąb ziemi czy konstrukcji stropu. To detale, takie jak precyzyjne połączenie warstw izolacyjnych czy dbałość o każdy milimetr poziomu, decydują o tym, czy ogrzewanie będzie komfortowe i ekonomiczne, czy stanie się źródłem frustracji i rachunków, które przyprawiają o zawrót głowy.
Wyrównanie i oczyszczenie podłoża
Przygotowanie posadzki pod system ogrzewania podłogowego to fundament, na którym zbudowana jest cała, późniejsza wygoda cieplna domu. Pierwszym i absolutnie krytycznym krokiem jest idealne wyrównanie i skrupulatne oczyszczenie podłoża. Bez tego etapu, nawet najlepsza izolacja czy rury najwyższej klasy nie zagwarantują prawidłowego działania instalacji.
Wyrównanie podłoża ma na celu uzyskanie powierzchni o minimalnej tolerancji odchylenia od płaszczyzny. Normy budowlane często precyzują, że nierówności nie powinny przekraczać kilku milimetrów na metr bieżący. Zbyt duże wgłębienia czy wybrzuszenia pod warstwą izolacji termicznej mogą prowadzić do naprężeń, uszkodzenia płyt izolacyjnych lub nierównomiernego rozkładu rur grzewczych, co w efekcie przekłada się na „zimne” i „ciepłe” strefy na podłodze – a przecież tego chcemy uniknąć jak ognia.
Ocena stanu istniejącego podłoża jest punktem wyjścia. Często mamy do czynienia ze stanem surowym – płytą fundamentową na gruncie lub stropem wylewanym na budowie. Niezależnie od typu, taka powierzchnia rzadko bywa idealnie gładka i płaska „prosto spod kielni”. Zdarzają się resztki betonu, wystające kamienie, fragmenty drewna szalunkowego, a także wyraźne fałdy czy spadki.
Do oceny równości powierzchni najlepiej użyć długiej poziomicy (minimum 2 metry) lub lasera liniowego. Przykładamy poziomicę do podłoża w różnych miejscach i kierunkach, obserwując szczelinę między narzędziem a powierzchnią. Lasery pozwalają na szybkie wyznaczenie płaszczyzny odniesienia w całym pomieszczeniu, co jest szczególnie przydatne na większych metrażach. To nie wyścigi, to precyzyjna chirurgia budowlana.
Jeśli nierówności są znaczące, rzędu centymetrów, konieczne może być zastosowanie warstwy wyrównującej. Może to być wylewka cementowa, z tą różnicą, że kładziona z większą starannością niż pierwotna płyta. Grubość tej warstwy zależy od skali problemu; przy mniejszych nierównościach wystarczy nawet kilka centymetrów.
W przypadku mniejszych nierówności (np. do 20-30 mm), doskonałym rozwiązaniem są specjalistyczne wylewki samopoziomujące. Materiały te charakteryzują się bardzo dobrą rozpływnością, co sprawia, że po wylaniu i rozprowadzeniu specjalną raką czy pacą zębatą, samoczynnie tworzą gładką i równą powierzchnię. Ważne, by pamiętać o odpowiednim zagruntowaniu podłoża przed ich aplikacją.
Wylewki samopoziomujące są zazwyczaj szybkowiążące, co przyspiesza prace, ale wymagają ścisłego przestrzegania proporcji wody i materiału podanych przez producenta. Dodanie zbyt dużej ilości wody co prawda ułatwi rozprowadzanie, ale znacznie osłabi parametry wytrzymałościowe jastrychu, co może mieć katastrofalne skutki pod obciążeniem końcowej posadzki i mebli.
Jeśli problemem są pojedyncze, wystające elementy lub niewielkie, ale ostre wybrzuszenia, często najprostszym rozwiązaniem jest mechaniczne szlifowanie lub kucie. Używa się do tego szlifierek do betonu ze specjalnymi tarczami lub lekkich młotów udarowych z dłutem. Pamiętajmy o masce przeciwpyłowej i okularach ochronnych – zdrowie jest najważniejsze.
Po etapie wyrównywania, niezależnie od zastosowanej metody, kluczowe jest dokładne oczyszczenie powierzchni. Pozostałości gruzu, pyłu, starej zaprawy, drewna czy innych zanieczyszczeń to potencjalne zagrożenie dla integralności kolejnych warstw. Mogą stanowić mostki termiczne, osłabiać przyczepność kolejnych warstw folii czy klejów, a w skrajnych przypadkach perforować cienkie membrany.
Czyszczenie rozpoczyna się od zamiecenia większych odpadów. Następnie konieczne jest usunięcie drobnego pyłu – najlepiej zrobić to za pomocą odkurzacza budowlanego lub przemysłowego. Zwykły odkurzacz domowy może nie poradzić sobie z drobnym pyłem i ulec uszkodzeniu. Czasem warto umyć podłoże, ale tylko pod warunkiem, że mamy możliwość szybkiego i dokładnego jego osuszenia.
Prawidłowo przygotowane podłoże pod warstwę izolacji powinno być twarde, stabilne, równe i absolutnie czyste. To trochę jak malowanie – nikt rozsądny nie zaczyna malować ściany, zanim nie usunie starej, łuszczącej się farby i nie oczyści jej z kurzu. W budownictwie to jeszcze ważniejsze, bo błędy trudniej ukryć, a ich konsekwencje są daleko poważniejsze i droższe w usunięciu.
Przykład z życia: Znajomy opowiadał o problemie z nierównomiernym nagrzewaniem podłogi w nowym domu. Po długich poszukiwaniach okazało się, że przyczyną była stara deska szalunkowa pozostawiona pod warstwą styropianu. Tworzyła ona most termiczny, który zaburzał przepływ ciepła w tym fragmencie pętli grzewczej. Niby drobiazg, a tyle kłopotu!
Podsumowując ten etap: zainwestowanie czasu i uwagi w solidne wyrównanie i oczyszczenie podłoża to inwestycja, która zwraca się w bezproblemowej eksploatacji ogrzewania podłogowego. To nie jest miejsce na kompromisy czy pójście na skróty. Precyzja jest tutaj naszą najlepszą przyjaciółką, a pośpiech – wrogiem.
Czysta i równa baza to gwarancja, że kolejne etapy – układanie izolacji i rur – przebiegną sprawnie i zgodnie z projektem. Pamiętajmy, że każda wylewka, czy to wyrównująca czy samopoziomująca, wymaga odpowiedniego czasu na związanie i wyschnięcie, zanim przejdziemy do dalszych prac. Niedotrzymanie przerw technologicznych to kolejny często popełniany błąd, który mści się w przyszłości. Cierpliwość w budownictwie jest cnotą, która naprawdę popłaca.
Nawet drobne kamyki czy resztki zaprawy pozostawione na podłożu mogą uszkodzić folię przeciwwilgociową lub dociskane płyty styropianowe. To małe dziurki, niewidoczne gołym okiem podczas montażu, które z czasem mogą stać się ścieżkami dla wilgoci. Trochę to jak chodzenie po szkle w cienkich skarpetkach – nie chcesz tego robić, prawda? Tak samo nie chcesz zostawiać ostrych niespodzianek pod drogą warstwą izolacji.
Warto rozważyć wynajęcie profesjonalnego sprzętu do szlifowania i odkurzania przemysłowego, jeśli powierzchnia jest duża lub bardzo zanieczyszczona. Koszt takiego wynajmu to ułamek kosztów naprawy źle wykonanej podłogi grzewczej. Dbajmy o to, by pierwszy krok był solidny i przemyślany. Równa i czysta płaszczyzna to nasz punkt zero, z którego startuje cała podłogowa instalacja.
Gładkie wykończenie podłoża ma także znaczenie dla późniejszego komfortu pracy. Łatwiej układa się rolki folii, płyty styropianowe leżą stabilniej i bez naprężeń, a folia z siatką do mocowania rur lepiej przylega. To przekłada się na szybszą i bardziej precyzyjną instalację samego ogrzewania.
Podsumowując z przymrużeniem oka: jeśli twoje podłoże przypomina powierzchnię Księżyca, a nie stołu operacyjnego, to masz problem. Ale każdy problem ma rozwiązanie, trzeba tylko wybrać odpowiednie narzędzia i poświęcić czas na jego realizację. Wyrównanie i oczyszczenie to ta mniej ekscytująca część budowy, ale równie ważna jak dobór pompy ciepła czy kolektorów słonecznych. Nuda, ale kluczowa nuda!
Nierzadko podczas przygotowania podłoża odkrywane są ukryte niespodzianki, np. przebieg instalacji hydraulicznych czy elektrycznych pod wylewką. Należy je odpowiednio zabezpieczyć, np. osadzając w rurach ochronnych, aby uniknąć uszkodzeń podczas dalszych prac. Czyste i równe podłoże daje nam pełen obraz sytuacji i pozwala na zaplanowanie kolejnych kroków bez nagłych awarii.
Ocena wilgotności i suszenie
Można powiedzieć, że suche podłoże to sucha robota, a wilgotne podłoże to przepis na problemy. Ocena wilgotności i dokładne suszenie podłoża przed dalszymi etapami instalacji ogrzewania podłogowego to etap o znaczeniu wręcz strategicznym. Niedostateczna suchość może zniweczyć wysiłek włożony w pozostałe prace i wygenerować koszty, o których wolelibyśmy zapomnieć.
Dlaczego wilgoć jest takim wrogiem ogrzewania podłogowego? Przede wszystkim wilgoć w podłożu (betonowej płycie czy wylewce cementowej) stwarza idealne warunki do rozwoju pleśni i grzybów. Te mikroorganizmy nie tylko negatywnie wpływają na jakość powietrza w pomieszczeniach (problemy zdrowotne, alergie), ale mogą także niszczyć materiały budowlane, w tym izolację termiczną czy strukturalną podłogę.
Po drugie, obecność wilgoci może opóźnić lub wręcz uniemożliwić montaż wrażliwych na nią materiałów wykończeniowych, takich jak drewniane deski czy panele laminowane. Wielu producentów podłóg drewnianych wprost odrzuca roszczenia gwarancyjne, jeśli wilgotność podłoża przekroczyła dopuszczalny limit w momencie montażu.
Jak zatem sprawdzić wilgotność? Istnieje kilka metod, od prostych, domowych sposobów po precyzyjne pomiary laboratoryjne lub profesjonalne mierniki. Najbardziej powszechna i zalecana w przypadku podłoży pod podłogi wrażliwe na wilgoć (np. drewno, parkiet) jest metoda karbidowa (CM). Pomiaru dokonuje się specjalnym aparatem, w którym próbka pobrana z podłoża reaguje z karbidem, a powstały acetylen powoduje wzrost ciśnienia, odzwierciedlający ilość wilgoci. Ta metoda wymaga pobrania próbki z głębi wylewki, co czyni ją inwazyjną, ale jest bardzo wiarygodna.
Elektroniczne mierniki wilgotności to szybsza, ale zazwyczaj mniej precyzyjna opcja. Działają na zasadzie pomiaru przewodności elektrycznej lub dielektrycznej materiału. Mogą być pomocne do wstępnej oceny lub monitorowania procesu schnięcia wylewki, ale rzadko wystarczają jako jedyne narzędzie akceptacji podłoża, zwłaszcza dla podłóg drewnianych. Trochę jak termometr do ciała – daje ogólny obraz, ale do postawienia diagnozy potrzeba czegoś więcej.
Jakie są dopuszczalne poziomy wilgotności? Dla wylewek cementowych pod płytki ceramiczne czy kamienne często akceptuje się wilgotność resztkową do około 2,5-3% CM. Jednak dla posadzek drewnianych, paneli laminowanych czy żywic epoksydowych, wymagania są znacznie ostrzejsze – zazwyczaj poniżej 2% CM, a dla jastrychów anhydrytowych (które schną inaczej i są bardziej wrażliwe) nawet poniżej 0,3-0,5% CM (jeśli jest ogrzewanie podłogowe) lub 0,5% CM (bez ogrzewania). Zawsze należy sprawdzić zalecenia producenta wybranej posadzki!
Czas schnięcia wylewki cementowej to temat rzeka, często budzący frustrację na budowie. Przyjmuje się orientacyjną zasadę, że 1 cm wylewki schnie około 1 tygodnia w optymalnych warunkach (temperatura około 20°C, dobra wentylacja, wilgotność powietrza około 60%). Powyżej 4 cm grubości czas schnięcia wydłuża się, bo wilgoć musi pokonać dłuższą drogę do powierzchni. Jastrych o grubości 5 cm na ogrzewaniu podłogowym może schnąć nawet 6-8 tygodni naturalnie.
Sztuczne przyspieszanie procesu schnięcia, np. przez używanie nagrzewnic bez odpowiedniej wentylacji, może prowadzić do powierzchniowego przeschnięcia i spękań, podczas gdy głębsze warstwy wciąż pozostają mokre. To pozorne suszenie, które tylko maskuje problem. Wentylacja jest kluczowa – usuwa wilgotne powietrze z powierzchni i pozwala wilgoci z wnętrza odparować.
Kiedy naturalne schnięcie trwa zbyt długo, można zastosować tzw. wygrzewanie wylewki z ogrzewaniem podłogowym. Jest to kontrolowany proces podnoszenia temperatury w rurach, który wymusza szybsze odparowywanie wilgoci z jastrychu. Protokół wygrzewania jest zazwyczaj dostarczany przez producenta systemu grzewczego lub dostawcę wylewki i musi być ściśle przestrzegany. Zazwyczaj zaczyna się od niskiej temperatury (np. 20-25°C) i stopniowo podnosi ją o kilka stopni dziennie, utrzymując temperaturę maksymalną (np. 45-55°C, zależnie od wylewki i materiałów) przez kilka dni, a następnie stopniowo obniżając. To wymaga energii, ale oszczędza tygodnie czekania.
Podczas wygrzewania kluczowa jest ciągła, intensywna wentylacja pomieszczeń. Otwieranie okien (nawet uchylenie) jest niezbędne, aby usunąć parującą wodę. Niektóre systemy zarządzania budową potrafią zautomatyzować ten proces, kontrolując zarówno temperaturę w rurach, jak i wentylację.
Ignorowanie etapu suszenia i pomiaru wilgotności to prosta droga do katastrofy. Wyobraźmy sobie ułożenie drogiego drewnianego parkietu na wylewce o wilgotności 4% CM. W najlepszym wypadku parkiet zacznie puchnąć i wypaczać się; w najgorszym – pojawi się grzyb, którego usunięcie będzie wymagało zerwania całej podłogi i dezynfekcji. To nie jest scenariusz, który chciałbyś przeżyć po zainwestowaniu w system ogrzewania podłogowego.
Innym aspektem jest wilgoć kapilarna, która może podnosić się z gruntu. Właśnie dlatego izolacja przeciwwilgociowa jest umieszczana zazwyczaj pod izolacją termiczną, aby zablokować tę drogę wilgoci. Ale nawet przy najlepszej izolacji, wylewka wciąż ma własną wilgoć zarobową, która musi odparować. To trochę jak pieczenie chleba – musi się wystudzić, zanim go pokroisz, bo inaczej będzie zakalec. Tutaj „zakalcem” jest mokra wylewka.
Warto zainwestować w wynajem profesjonalnego miernika CM na czas końcowej oceny wilgotności lub zlecić pomiar niezależnemu specjaliście. Koszt takiego pomiaru (kilkaset złotych) jest nieporównywalnie niski w stosunku do potencjalnych strat wynikających z wilgotnej wylewki.
Studium przypadku: W jednym z domów jednorodzinnych, pośpiech w oddaniu budynku spowodował ułożenie paneli podłogowych na wylewce, której naturalne schnięcie nie zostało zakończone, a protokół wygrzewania skrócono. Po kilku miesiącach użytkowania paneli, zaczęły się wybrzuszać w narożnikach i między deskami. Pomiar CM wykazał nadal podwyższoną wilgotność resztkową wylewki. Konieczne było zerwanie paneli, dodatkowe suszenie wylewki i ponowne ułożenie podłogi – podwójny koszt i stracony czas.
Kontrola wilgotności i cierpliwość w procesie suszenia wylewki to absolutna konieczność. Nie ulegaj presji czasu ani pozorom suchej powierzchni. To co na wierzchu, często nie odzwierciedla stanu w środku. Pamiętaj, że posadzka pod ogrzewanie podłogowe pracuje pod wpływem temperatury, co dodatkowo uwidacznia i potęguje problemy wynikające z wilgoci.
Rynek oferuje także specjalne przyspieszacze schnięcia dodawane do jastrychów, jednak ich stosowanie i efektywność bywają różne i zawsze należy postępować ściśle z zaleceniami producenta wylewki i dodatków. Nigdy nie zastąpią one podstawy: odpowiedniej wentylacji i czasu. Czasami stare, sprawdzone metody są po prostu najlepsze, a w tym przypadku – pozwolić wylewce swobodnie oddychać i pozbyć się nadmiaru wody, przy odpowiednim wspomaganiu wymiany powietrza.
Zakończenie tego etapu z sukcesem, czyli uzyskanie wymaganej wilgotności resztkowej potwierdzonej pomiarem CM, daje nam zielone światło do kolejnych prac i spokój ducha. To jak zakończenie kwarantanny z negatywnym wynikiem testu – można bezpiecznie iść dalej. Przygotowana w ten sposób wylewka stanowi stabilną i trwałą bazę pod warstwy izolacji i samą instalację grzewczą.
Niektórzy mówią: "A tam, na oko jest sucha". Ale oko potrafi mylić. Wylewka, zwłaszcza cementowa, może wyglądać na suchą na powierzchni, a w środku skrywać spore ilości wody. Ta wilgoć potem wędruje do góry pod wpływem temperatury z rur grzewczych. Pomyśl o tym jak o gąbce – z zewnątrz może wydawać się sucha, ale w środku wciąż jest wilgotna. Dopiero mocne ściśnięcie (czyli w przypadku wylewki, ogrzanie) wyciska tę wodę na zewnątrz. Dlatego dokładny pomiar jest nieodzowny.
Izolacja przeciwwilgociowa
Stawiając dom na gruncie, czy nawet remontując podłogę na parterze, musimy liczyć się z potencjalnym zagrożeniem: wilgocią pochodzącą z ziemi. W tym miejscu do gry wkracza izolacja przeciwwilgociowa, strażnik, który chroni nasz system ogrzewania podłogowego i całą konstrukcję podłogi przed niechcianą wodą. Jej prawidłowe ułożenie to absolutna podstawa, zwłaszcza w przypadku, gdy płyta betonowa ma bezpośredni kontakt z gruntem.
Głównym zadaniem izolacji przeciwwilgociowej jest stworzenie szczelnej bariery, która uniemożliwi przenikanie wilgoci kapilarnej z niższych warstw, czyli po prostu z gruntu, w głąb konstrukcji podłogi i do warstw izolacji termicznej oraz jastrychu grzewczego. Ta wilgoć, niczym woda po nitce, potrafi wspinać się w materiałach porowatych, a beton czy jastrych do takich należą.
Najczęściej stosowanym materiałem na izolację przeciwwilgociową pod podłogą na gruncie jest folia budowlana o dużej grubości, zazwyczaj minimum 0,2 mm (200 mikronów). Ważne, aby była to folia oznaczona jako izolacyjna lub hydroizolacyjna, a nie zwykła folia ochronna o mniejszej gramaturze, która łatwo ulega uszkodzeniu i nie daje gwarancji szczelności. Czasami stosuje się specjalistyczne membrany hydroizolacyjne o jeszcze lepszych parametrach.
Folia układana jest bezpośrednio na wyrównanym i oczyszczonym podłożu betonowym (płycie fundamentowej lub chudziaku). To pierwsza warstwa nad betonem. Pamiętajmy, że podłoże betonowe pod folią powinno być w miarę równe i pozbawione ostrych krawędzi, które mogłyby ją przebić podczas montażu kolejnych warstw lub pod obciążeniem. Dziura w izolacji przeciwwilgociowej to tak jak dziura w parasolu podczas deszczu – mija się z celem.
Kluczowym elementem zapewnienia szczelności jest prawidłowe łączenie arkuszy folii. Nie wystarczy po prostu położyć ich na styk. Konieczne jest wykonanie odpowiedniego zakładu, czyli ułożenie jednego arkusza na drugim na szerokości minimum 15-20 cm. To jak łuski u ryby – każde zakrywa kawałek sąsiedniego.
Same zakłady nie wystarczą, aby zagwarantować pełną szczelność. Należy je starannie skleić specjalną taśmą budowlaną lub butylową, która zapewni trwałe i wodoszczelne połączenie. Zwykła taśma pakowa czy malarska nie nadaje się do tego celu, bo szybko ulegnie degradacji w środowisku budowlanym.
Niezwykle ważne jest również wyprowadzenie folii na ściany. Powinna być ona zagięta w górę wzdłuż wszystkich ścian i elementów pionowych (jak słupy, przejścia instalacyjne) na wysokość przekraczającą poziom planowanego jastrychu grzewczego. Po wylaniu i związaniu jastrychu nadmiar folii jest docinany równo z poziomem posadzki lub pod jej wykończenie, w zależności od detalu. Dzięki temu wilgoć jest skutecznie blokowana również na styku podłogi i ścian.
To zagięcie na ścianę jest krytyczne. Bez niego wilgoć mogłaby "obejść" barierę i przedostać się do murów, a następnie do warstw podłogi. Trochę jak płot bez furtki – nie zatrzyma niczego, co potrafi się przez niego przecisnąć. Zagięta folia działa jak szczelne wiaderko, w którym zamykamy kolejne warstwy podłogi.
Miejsca przejść instalacji przez płytę betonową (np. rury kanalizacyjne, wodne) wymagają szczególnej uwagi. Folię należy dookoła tych elementów starannie obkleić, stosując uszczelniacze lub mankiety z folii, aby stworzyć wodoszczelne przejście. Każdy otwór to potencjalny przeciek, którego musimy pilnować.
Częstym błędem jest niedostateczny zakład folii lub brak sklejenia zakładów. Innym błędem jest przypadkowe przedziurawienie folii podczas kolejnych prac budowlanych – chodzenia po niej w ostrych butach, upuszczania narzędzi, przenoszenia materiałów. Dlatego po ułożeniu izolacji przeciwwilgociowej należy obchodzić się z nią bardzo ostrożnie, a w razie potrzeby zabezpieczyć dodatkową warstwą, np. tektury falistej, jeśli prace wymagają intensywnego ruchu.
W niektórych systemach podłóg na gruncie, oprócz folii na betonie, stosuje się również izolację poziomą ścian fundamentowych (tzw. papę fundamentową), która jest łączona z izolacją podłogi, tworząc wodoszczelną "wannę". Systemowe rozwiązania izolacyjne często wymagają zastosowania kompatybilnych materiałów – folii, taśm klejących i uszczelniaczy od jednego producenta.
W przypadku podłóg na piętrze czy międzykondygnacyjnych izolacja przeciwwilgociowa ma nieco inne zadanie. Układana jest zazwyczaj nad izolacją termiczną, bezpośrednio pod jastrychem grzewczym. Jej rolą jest wtedy głównie zapobieżenie przenikaniu wody zarobowej z mokrego jastrychu w głąb konstrukcji stropu i izolacji termicznej podczas procesu wylewania i schnięcia. W tym przypadku również ważne są zakłady i klejenie.
Grubość folii 0,2 mm (200 µm) to minimum. Często zaleca się stosowanie folii o grubości 0,3 mm (300 µm) lub specjalistycznych membran, które dają większą pewność szczelności. To niewielki dodatkowy koszt, który znacząco podnosi bezpieczeństwo całej konstrukcji. Warto dopytać dostawcę materiałów lub projektanta o rekomendowaną grubość i rodzaj folii dla konkretnego zastosowania.
Studium przypadku: W piwnicy adaptowanej na cele mieszkalne zapomniano o połączeniu izolacji przeciwwilgociowej podłogi z istniejącą izolacją ścian. Po kilku latach na dole ścian i podłogi pojawił się grzyb. Okazało się, że wilgoć z gruntu podnosiła się po ścianach, a następnie przesiąkała w dolne partie podłogi, wędrując pod jastrych. Konieczne było zerwanie części podłogi, wykonanie nowego połączenia izolacji i osuszanie ścian.
Prawidłowe wykonanie izolacji przeciwwilgociowej to jeden z tych "niewidocznych" etapów, którego znaczenie doceniamy dopiero wtedy, gdy coś pójdzie nie tak. Dbając o każdy zakład, każde połączenie, o wyprowadzenie folii na ściany i zabezpieczenie przejść, minimalizujemy ryzyko kosztownych problemów w przyszłości. To trochę jak ubezpieczenie – płacimy za nie, mając nadzieję, że nigdy go nie będziemy potrzebować, ale jego brak w sytuacji kryzysowej potrafi złamać kręgosłup finansowy.
Niektórzy producenci systemów izolacji termicznej pod ogrzewanie podłogowe oferują płyty styropianowe laminowane fabrycznie folią. Choć to wygodne rozwiązanie, należy upewnić się, czy zastosowana folia ma odpowiednią grubość i czy producent zaleca ją jako jedyną warstwę przeciwwilgociową na danym podłożu. W wielu przypadkach wymagana jest dodatkowa, gruba folia położona bezpośrednio na betonowym podłożu, poniżej izolacji termicznej, szczególnie na gruncie.
Na koniec – drobny detal, który robi różnicę: folia nie powinna być ułożona idealnie napięta. Warto zostawić jej lekki luz, aby nie uległa pęknięciu podczas pracy kolejnych warstw lub pod wpływem niewielkich ruchów konstrukcji. Nie szpanujemy gładkością folii jak przy pakowaniu prezentów – ma być szczelna, a nie estetyczna.
Izolacja termiczna
Myśląc o ogrzewaniu podłogowym, naszym głównym celem jest, aby ciepło trafiało tam, gdzie tego chcemy – czyli do góry, do pomieszczenia, ogrzewając powietrze i nasze stopy. Aby tak się stało, konieczne jest zastosowanie skutecznej izolacji termicznej. To ona tworzy barierę, która minimalizuje straty ciepła w dół, w głąb podłoża lub stropu, i kieruje całą energię w stronę użytkowników. Bez tej izolacji ogrzewalibyśmy z równym zapałem fundamenty, piwnicę czy sąsiada pod nami, a nasze rachunki za energię by szybowały.
Głównym materiałem używanym do izolacji termicznej podłóg z ogrzewaniem podłogowym są twarde płyty styropianowe lub płyty z polistyrenu ekstrudowanego (XPS). Nie można tutaj zastosować zwykłego, miękkiego styropianu fasadowego, który jest znacznie mniej odporny na ściskanie. Posadzka wraz z wylewką grzewczą i wykończeniem może ważyć kilkaset kilogramów na metr kwadratowy, a do tego dochodzą obciążenia użytkowe (meble, ludzie). Materiał izolacyjny musi to wytrzymać bez odkształceń.
Parametrem kluczowym dla płyt izolacyjnych podłogowych jest ich wytrzymałość na ściskanie przy 10% odkształceniu, oznaczana jako CS(10) lub EPS XX, gdzie XX to wartość CS(10) w kPa podzielona przez 10. Minimalna wymagana wartość to zazwyczaj EPS 100 (co oznacza 100 kPa, czyli 10 ton/m²) dla typowych obciążeń mieszkalnych, ale często zaleca się EPS 150 (150 kPa / 15 ton/m²) lub nawet EPS 200 (200 kPa / 20 ton/m²) w przypadku większych obciążeń, garaży czy pomieszczeń technicznych. XPS ma z natury lepszą wytrzymałość na ściskanie (często >300 kPa) i lepszy współczynnik przewodzenia ciepła (lambda), ale jest też droższy.
Równie ważny jest współczynnik przewodzenia ciepła Lambda (λ) wyrażany w W/(m*K). Określa on, jak dobrze dany materiał przewodzi ciepło – im niższa wartość Lambda, tym lepsza izolacja termiczna. Typowe wartości dla styropianu podłogowego to ok. 0,036-0,040 W/(m*K), a dla XPS ok. 0,033-0,036 W/(m*K).
Grubość warstwy izolacji termicznej powinna wynikać z projektu budowlanego i być zgodna z aktualnymi wymaganiami Warunków Technicznych dotyczącymi energooszczędności budynków. Dla podłóg na gruncie, w zależności od strefy klimatycznej i wymagań WT, minimalna grubość izolacji ze styropianu EPS 100/150 to często 10-15 cm, a nawet więcej w domach pasywnych. Na stropach między ogrzewanymi kondygnacjami izolacja może być cieńsza (np. 3-5 cm), ale pod stropami nieogrzewanych piwnic czy garaży grubość będzie podobna jak na gruncie.
Izolacja termiczna jest układana na warstwie izolacji przeciwwilgociowej (na gruncie) lub bezpośrednio na oczyszczonym i wyrównanym stropie (na piętrze/pomiędzy kondygnacjami). Płyty układa się na tzw. mijankę, ze spoinami przesuniętymi względem siebie w kolejnych rzędach, tak jak murarze układają cegły. Minimalizuje to ryzyko powstania mostków termicznych na połączeniach płyt.
W przypadku układania kilku warstw płyt izolacyjnych (np. łącznie 15 cm z dwóch warstw 7,5 cm), spoiny w warstwie górnej powinny być przesunięte względem spoin w warstwie dolnej. Płyty powinny być docięte precyzyjnie i ściśle przylegać do siebie oraz do ścian i innych elementów konstrukcyjnych. Każda szczelina między płytami lub między płytą a ścianą to potencjalny mostek termiczny – miejsce, przez które ciepło będzie uciekać w dół lub w bok.
Szczeliny między płytami styropianu można w przypadku wątpliwości dodatkowo wypełnić niskorozprężną pianką poliuretanową, dedykowaną do styropianu, lub zakleić taśmą. Dbałość o szczelność połączeń płyt izolacyjnych jest równie ważna co grubość samej izolacji. To jak dziurawy płaszcz zimą – nawet gruby, nie ochroni nas przed zimnem, jeśli wiatr będzie hulał przez szczeliny.
Na rynku dostępne są również specjalistyczne płyty systemowe do ogrzewania podłogowego. Są to zazwyczaj płyty styropianowe (EPS) lub XPS ze specjalnie uformowanymi wypustkami lub rowkami, które ułatwiają i przyspieszają montaż rur grzewczych, utrzymując je we właściwych rozstawach. Choć droższe, potrafią znacząco ułatwić i usprawnić pracę, zwłaszcza na dużych powierzchniach.
W niektórych systemach, szczególnie tam, gdzie zależy na maksymalnej minimalizacji wysokości warstw, stosuje się płyty termoizolacyjne o bardzo wysokiej wytrzymałości na ściskanie i bardzo niskim współczynniku Lambda, np. z pianki poliuretanowej PIR/PUR. Są one znacznie droższe, ale pozwalają uzyskać odpowiednią izolację przy mniejszej grubości. Lambda PIR/PUR może wynosić nawet poniżej 0,025 W/(m*K).
Koszt materiałów izolacyjnych to znacząca pozycja w budżecie na podłogę. Płyty styropianowe EPS 100/150 o grubości 10 cm kosztują orientacyjnie od 30 do 50 zł/m², w zależności od producenta i regionu. XPS jest droższy, cena może wynosić 50-80 zł/m² dla porównywalnej grubości. Płyty systemowe z wypustkami bywają jeszcze droższe, np. 60-100 zł/m².
Przykład z życia: Deweloper w pewnym budynku z oszczędności zastosował cieńszy styropian, niż wynikało z projektu energetycznego. Mieszkańcy parteru po włączeniu ogrzewania podłogowego narzekali na wysokie rachunki i wolne nagrzewanie pomieszczeń. Termowizja pokazała znaczne straty ciepła w dół. Poprawa izolacji była niemożliwa bez skuwania całej podłogi. Klasyczny przykład, jak oszczędność w złym miejscu mści się przez lata użytkowania.
Instalatorzy systemów grzewczych często zwracają uwagę, że solidna warstwa izolacji termicznej nie tylko zmniejsza straty ciepła, ale także poprawia komfort użytkowania ogrzewania podłogowego. Podłoga nagrzewa się szybciej i jest bardziej responsywna na zmiany temperatury, co przekłada się na lepszą sterowalność systemu. Można porównać to do termosu – im lepsza izolacja, tym dłużej ciepło pozostaje w środku, zamiast uciekać na zewnątrz.
Podczas układania izolacji termicznej należy zachować ostrożność, aby nie uszkodzić położonej niżej folii przeciwwilgociowej. Ciężkie narzędzia, ostre krawędzie płyt – wszystko to może stanowić zagrożenie. Pracę należy wykonywać starannie, krok po kroku, upewniając się, że każda płyta leży stabilnie i szczelnie.
Na koniec tego etapu, przed ułożeniem kolejnych warstw (często folii z nadrukiem siatki montażowej i samej instalacji rur), warto jeszcze raz upewnić się, że powierzchnia izolacji jest równa i czysta. Niewielkie odpady styropianu, pył – wszystko to warto usunąć, aby kolejne warstwy dobrze przylegały.
Podsumowując ten etap: izolacja termiczna to mięsień ogrzewania podłogowego, który sprawia, że działa ono wydajnie i ekonomicznie. Nie oszczędzajmy na jej jakości i grubości. Pamiętajmy o odpowiedniej wytrzymałości na ściskanie i niskim współczynniku Lambda. Solidnie ułożona, szczelna warstwa izolacji to inwestycja w komfort cieplny i niskie rachunki przez lata. Niech ciepło idzie do góry, a nie w ziemię!
Dobór odpowiedniej grubości i typu izolacji powinien być poprzedzony analizą cieplną budynku. Inna grubość będzie wymagana w budynku o słabych parametrach izolacyjności ścian i dachu, a inna w nowoczesnym, energooszczędnym domu. Projektant systemów grzewczych powinien wziąć pod uwagę te aspekty. Pamiętaj, że im lepiej zaizolujesz podłogę, tym mniejsze będą koszty eksploatacji ogrzewania w przyszłości. To czysta matematyka w praktyce.
Upewnij się, że wybrany przez ciebie styropian ma atesty i deklaracje zgodności potwierdzające jego parametry, w szczególności wytrzymałość na ściskanie. Na rynku pojawiają się materiały, które nie spełniają deklarowanych norm, co w przypadku tak kluczowego elementu konstrukcyjnego jak izolacja podłogi pod ogrzewanie może być bardzo problematyczne.
Układanie taśmy brzegowej
Choć może wydawać się drobnym elementem w skomplikowanej strukturze podłogi z ogrzewaniem, układanie taśmy brzegowej pełni absolutnie kluczową rolę. To taśma dylatacyjna, miękka opaska umieszczana na styku przyszłego jastrychu grzewczego ze ścianami i innymi elementami konstrukcyjnymi. Można o niej myśleć jak o zbroi rycerza, która musi być elastyczna na stawach, by nie pękła przy ruchu – tutaj tym „ruchem” jest rozszerzalność termiczna wylewki pod wpływem ciepła.
Głównym zadaniem taśmy brzegowej jest umożliwienie swobodnej, poziomej rozszerzalności termicznej jastrychu betonowego lub anhydrytowego pod wpływem zmieniającej się temperatury od pracującego ogrzewania podłogowego. Jastrych, nagrzewając się, zwiększa swoją objętość. Gdyby na jego drodze znajdowały się sztywne ściany, powstałyby ogromne naprężenia. Mogłyby one doprowadzić do wybrzuszenia posadzki, spękania jastrychu, a nawet uszkodzenia konstrukcji ścian.
Taśma brzegowa, wykonana zazwyczaj z elastycznej pianki polietylenowej zamkniętokomórkowej, działa jak poduszka powietrzna (choć wypełniona pianką, a nie powietrzem), która ugina się pod naporem rozszerzającego się jastrychu, amortyzując naprężenia. Pozwala to jastrychowi "oddychać" i poruszać się bez ryzyka uszkodzenia. To trochę jak szczeliny dylatacyjne w mostach – chronią konstrukcję przed siłami wynikającymi ze zmian temperatury.
Inną ważną funkcją taśmy brzegowej jest izolacja akustyczna. Oddziela ona sztywny jastrych od ścian, które są elementem przenoszącym dźwięki (tzw. mostki akustyczne). Dzięki temu ogranicza przenoszenie dźwięków uderzeniowych (kroki, upadki przedmiotów) do niższych kondygnacji czy sąsiednich pomieszczeń. W przypadku ogrzewania podłogowego może również redukować przenoszenie ewentualnych szumów przepływającej w rurach wody, choć jest to zazwyczaj zjawisko marginalne.
Taśma brzegowa jest układana wzdłuż całego obwodu pomieszczenia, w którym wykonywane jest ogrzewanie podłogowe, na styku ścian i posadzki. Powinna być ułożona na styku z wszystkimi pionowymi elementami konstrukcyjnymi, które będą stykać się z jastrychem, czyli także wokół filarów, słupów, a nawet wokół ościeżnic drzwiowych, jeśli jastrych do nich dochodzi.
Standardowa grubość taśmy dylatacyjnej to 8-10 mm. Ta grubość zazwyczaj wystarcza do skompensowania rozszerzalności termicznej typowej wylewki grzewczej. Ważne jest, aby taśma miała odpowiednią wysokość – powinna wystawać ponad planowany poziom jastrychu o kilka centymetrów. Dopiero po wylaniu i związaniu jastrychu nadmiar taśmy jest odcinany ostrym nożykiem równo z poziomem posadzki lub nieco poniżej, w zależności od materiału wykończeniowego podłogi.
Montaż taśmy brzegowej jest stosunkowo prosty, ale wymaga staranności. Taśma jest zazwyczaj sprzedawana w rolkach, często z samoprzylepnym paskiem na jednym z brzegów lub z foliowym fartuchem, który można rozłożyć na izolacji termicznej. Przykleja się ją lub po prostu dociska do ścian, upewniając się, że przylega na całej wysokości od podłoża (izolacji termicznej) aż ponad poziom przyszłego jastrychu.
Należy zadbać o ciągłość taśmy na całym obwodzie. W narożnikach taśmę można zagiąć lub dociąć i połączyć na styk, upewniając się, że nie ma żadnych przerw. W miejscach, gdzie przez podłogę przechodzą rury (np. do grzejników, jeśli występują), taśma również powinna być starannie ułożona wokół nich, odcinając jastrych od rury.
Dodatkowe dylatacje (szczeliny separacyjne) w samym jastrychu są konieczne w większych pomieszczeniach (zazwyczaj powyżej 30-40 m² lub o długim kształcie), w pomieszczeniach o nieregularnych kształtach, w progach drzwiowych (zwłaszcza jeśli podłoga z ogrzewaniem styka się tam z podłogą bez ogrzewania lub o innym systemie grzewczym), oraz wszędzie tam, gdzie układ pętli grzewczych się zmienia. W tych miejscach, zamiast taśmy brzegowej, stosuje się specjalne profile dylatacyjne lub po prostu na czas wylewania umieszcza się w jastrychu dodatkową taśmę dylatacyjną o odpowiedniej grubości, która potem tworzy szczelinę.
Koszt taśmy brzegowej jest niewielki w porównaniu do kosztów całej instalacji podłogowej – metr bieżący to zazwyczaj kilka złotych (np. od 1 zł do 5 zł/mb). Jest to jednak element, na którym absolutnie nie warto oszczędzać ani go pomijać. Niewykonanie dylatacji brzegowej to jeden z najczęstszych błędów przy ogrzewaniu podłogowym, prowadzący wprost do pęknięć jastrychu.
Przykład z życia: Budynek biurowy, gdzie w dużym pomieszczeniu open space zainstalowano ogrzewanie podłogowe. Wykonawca jastrychu "zapomniał" o dylatacjach obwodowych, a w środku pomieszczenia, mimo dużej powierzchni (ok. 60m²), nie wykonano żadnych dylatacji pośrednich. Po uruchomieniu ogrzewania, wylewka popękała w kilku miejscach, a na styku ze ścianami pojawiły się nieestetyczne wybrzuszenia. Naprawa wymagała częściowego skucia i ponownego wykonania jastrychu z uwzględnieniem dylatacji – kosztowna i uciążliwa lekcja.
Warto też zwrócić uwagę na to, że taśma brzegowa powinna być ułożona przed wylewaniem jastrychu, ale po ułożeniu izolacji termicznej. Jej prawidłowe przyleganie do ścian i izolacji jest kluczowe dla jej funkcji. Niektóre taśmy posiadają na spodzie „fartuch”, czyli przedłużenie folii, które rozkłada się na izolacji termicznej pod rurami. Ułatwia to układanie folii z siatką i dodatkowo chroni przed zawilgoceniem bocznych krawędzi izolacji termicznej przez wodę zarobową z jastrychu.
Pamiętajmy również, że nadmiar taśmy wystający ponad jastrych nie powinien być usuwany zbyt wcześnie, tj. przed pełnym związaniem i wyschnięciem jastrychu. Chroni on górną krawędź jastrychu przed uszkodzeniem mechanicznym na etapie prac wykończeniowych. Dopiero przed samym montażem podłogi wykończeniowej (np. płytek, paneli), taśma jest precyzyjnie odcinana.
Wyobraź sobie jastrych grzewczy jako wielką, twardą płytę kamienną. Kiedy się nagrzewa, rośnie w każdym kierunku. Bez miejsca na ten "wzrost", zderza się ze ścianą i coś musi pęknąć – zazwyczaj płyta, bo jest twardsza niż miękka pianka, ale mniej elastyczna niż cała ściana. Taśma brzegowa jest jak bufor, który przyjmuje na siebie te siły. To cicha bohaterka instalacji ogrzewania podłogowego.
Grubość 8 mm to minimum dla standardowych zastosowań, ale jeśli planowany jastrych jest wyjątkowo duży lub o niestandardowym składzie, można rozważyć taśmę 10 mm. Warto też sprawdzić, czy taśma posiada niezbędne atesty i czy jest wykonana z materiału o odpowiedniej gęstości i ściśliwości, który nie straci swoich właściwości z czasem.
Zakończenie tego etapu, czyli kompletne oklejenie obwodów pomieszczeń taśmą brzegową i wykonanie niezbędnych dylatacji pośrednich, to zielone światło do wylewania jastrychu. To mały koszt i niewielki wysiłek, który chroni przed poważnymi problemami konstrukcyjnymi i akustycznymi w przyszłości. Nie można tego zignorować, licząc, że jakoś to będzie – bo "jakoś to będzie" w budowlance rzadko kiedy kończy się dobrze.
Orientacyjny koszt materiałów na 1 m² podłogi z ogrzewaniem podłogowym
Poniższa tabela przedstawia orientacyjny koszt materiałów na jeden metr kwadratowy typowej podłogi na gruncie z ogrzewaniem podłogowym w domu jednorodzinnym, z izolacją termiczną 10 cm styropianu EPS 100.
Materiał | Ilość / m² | Jednostka | Orientacyjna cena jednostkowa | Orientacyjny koszt / m² |
---|---|---|---|---|
Folia przeciwwilgociowa (0.2 mm) | ~1.1* | m² | 2.00 PLN / m² | 2.20 PLN |
Styropian EPS 100 (10 cm) | 0.1 | m³ | 450.00 PLN / m³ | 45.00 PLN |
Folia z siatką (pod rury) | ~1.1* | m² | 3.50 PLN / m² | 3.85 PLN |
Taśma brzegowa (10 mm, zakładając 1 mb na 2 m² powierzchni) | 0.5 | mb | 4.00 PLN / mb | 2.00 PLN |
Uchwyty do rur grzewczych (szpilki/tacker) | ~50-100 | szt. | 0.10 PLN / szt. | 5.00 - 10.00 PLN |
Rura grzewcza PE-RT/PEX (fi 16mm, rozstaw co 15 cm) | ~6.7 | mb | 4.00 PLN / mb | 26.80 PLN |
Jastrych cementowy (ok. 6.5-7 cm nad rurą) | ~0.14* | m³ | 400.00 PLN / m³ (materiał workowany lub gotowy beton) | 56.00 PLN |
Dodatki do jastrychu (plastyfikator, włókna) | Wg zużycia | - | ~5.00 PLN | |
SUMA ORIENTACYJNA (materiały) | ~145 - 150 PLN / m² |
*Zakład 10%.
Przeciętny kształt pomieszczenia.
*Grubość jastrychu ok. 4-5 cm + 1.6 cm rura + 6.5-7 cm nad rurą = ~12.1-13.6 cm, ale liczymy zazwyczaj grubość nad rurą. Przy założeniu wylewki 6.5 cm nad rurą fi 16 i styropianu 10cm, całkowita grubość to 10+1.6+6.5 = 18.1cm. Gęstość jastrychu ok 2100 kg/m3. Jastrych 12cm x 2100 kg/m3 = 252 kg/m2. ~0.12 m³ / m².
Powyższe ceny są bardzo orientacyjne i mogą się znacznie różnić w zależności od regionu, dostawcy, marki produktów, a także od konkretnego rozwiązania systemowego i grubości wymaganych warstw. Nie obejmują kosztów robocizny, narzędzi, montażu rozdzielacza, pompy, sterowania, czy innych elementów systemu grzewczego.