Ile schnie posadzka przemysłowa w 2025? Sprawdź czas schnięcia
Pytanie Ile schnie posadzka przemysłowa nurtuje każdego, kto planuje inwestycję w nową powierzchnię użytkową, bo przecież czas to pieniądz. Czy można szybko wrócić do normalnej pracy? Krótka odpowiedź brzmi: to zależy od diabelnie wielu czynników, a poznanie ich to klucz do sukcesu i uniknięcia kosztownych błędów. Zanurzmy się w ten złożony świat, gdzie cierpliwość często popłaca, a pośpiech może być zgubny.
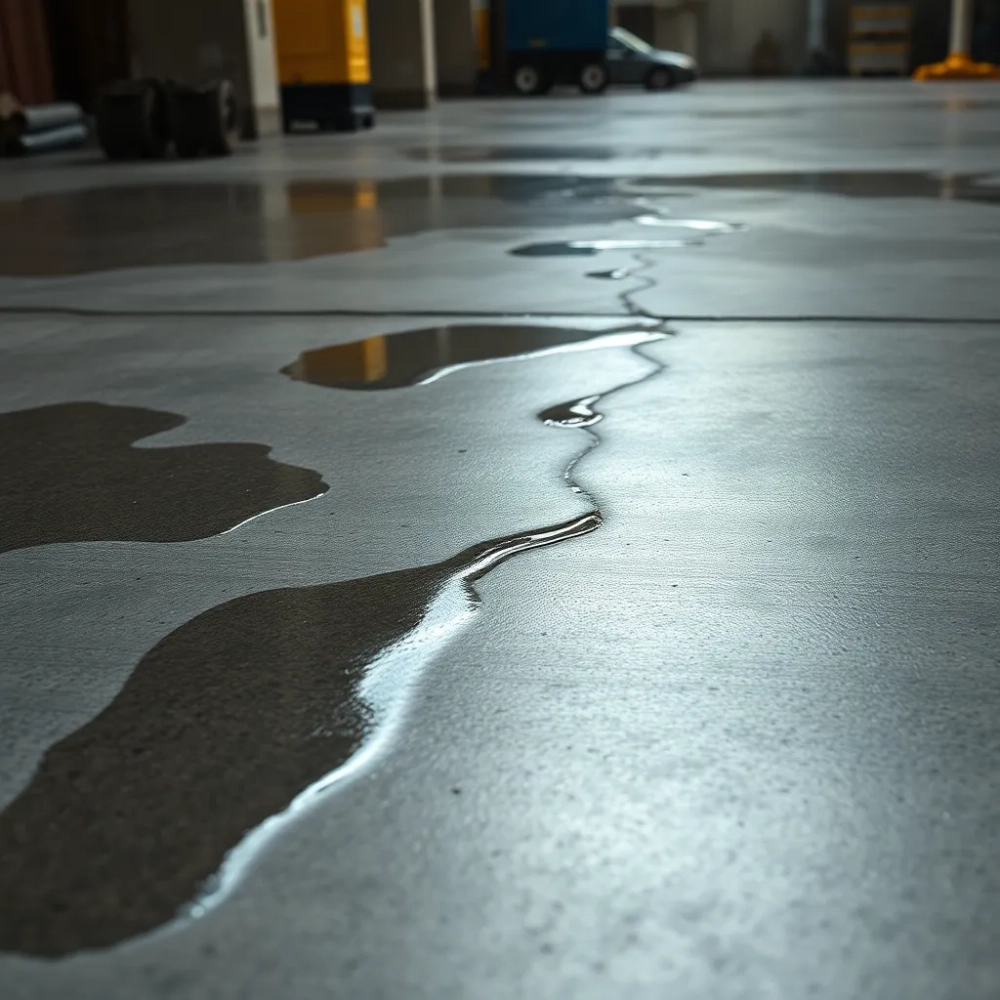
Aby zrozumieć proces schnięcia, spójrzmy na dane zebrane z różnych projektów, które unaoczniają, jak warunki zewnętrzne i specyfika materiału wpływają na czas oczekiwania. Poniższa tabela ilustruje orientacyjne czasy gotowości dla dwóch przykładowych typów posadzek w różnych środowiskach.
Typ Posadzki | Grubość (mm) | Temperatura (°C) | Wilgotność Powietrza (%) | Czas do ruchu pieszego (dni) | Czas do pełnego obciążenia (dni/tygodnie) |
---|---|---|---|---|---|
Cienkowarstwowa posadzka żywiczna (Epoksyd) | 1-2 | 20 | 50 | 1-2 | 7 |
Cienkowarstwowa posadzka żywiczna (Epoksyd) | 1-2 | 10 | 70 | 3-5 | 14 |
Samopoziomujący jastrych cementowy | 30 | 20 | 50 | 2-3 | 28 |
Samopoziomujący jastrych cementowy | 30 | 10 | 70 | 7-10 | 45-60 |
Widzimy wyraźnie, że te same materiały reagują zupełnie inaczej w zależności od otoczenia, a różnice w gotowości do użytku mogą być znaczące, często liczone w dodatkowych dniach czy nawet tygodniach. Temperatura i wilgotność to potężne czynniki, które potrafią przyspieszyć lub drastycznie spowolnić chemiczne procesy utwardzania.
Wpływ rodzaju posadzki przemysłowej na czas schnięcia i utwardzania
W świecie posadzek przemysłowych panuje ogromna różnorodność, a każdy materiał to inna historia jeśli chodzi o tempo, w jakim przechodzi ze stanu płynnego lub plastycznego do trwałej, obciążalnej powierzchni. Beton, żywice epoksydowe, poliuretanowe, czy cementowe wylewki szybkowiążące – każdy z nich ma swój specyficzny rytm schnięcia i utwardzania, podyktowany złożoną chemią wiązań i procesami fizycznymi.
Klasyczna posadzka betonowa, często stanowiąca fundament dla dalszych warstw lub finalną powierzchnię polerowaną, schnie i utwardza się przez długi czas, co jest wynikiem procesu hydratacji cementu – reakcji chemicznej wymagającej wody. Nawet po kilku dniach, kiedy wydaje się twarda, beton osiągnął zaledwie niewielki procent swojej docelowej wytrzymałości; pełne utwardzenie betonu może trwać nawet 28 dni, a w przypadku bardzo grubych płyt i niesprzyjających warunków, jeszcze dłużej.
Posadzki żywiczne, takie jak epoksydowe czy poliuretanowe, utwardzają się poprzez polimeryzację, czyli reakcję chemiczną między różnymi składnikami żywicy. Proces ten nie opiera się na odparowywaniu wody (choć niektóre systemy są na bazie wodnej), lecz na tworzeniu się silnych wiązań molekularnych. Czas utwardzania jest zazwyczaj znacznie krótszy niż betonu, często liczony w godzinach do wstępnego związania i kilku dniach do pełnego obciążenia, ale jest bardzo wrażliwy na temperaturę.
Wylewki cementowe szybkowiążące lub samopoziomujące, popularne przy renowacjach lub jako warstwa wyrównująca, zostały zaprojektowane tak, aby znacznie przyspieszyć tradycyjną hydratację cementu dzięki specjalnym dodatkom chemicznym. Mogą pozwolić na ruch pieszy już po kilku godzinach, a na położenie kolejnej warstwy lub lekkie obciążenie po 24-48 godzinach. Jednakże i one wymagają dłuższego okresu na osiągnięcie pełnej, deklarowanej przez producenta wytrzymałości.
Cementowo-polimerowe powłoki cienkowarstwowe, często stosowane do renowacji zniszczonego betonu lub jako estetyczna nawierzchnia, schną relatywnie szybko dzięki cienkiej warstwie i modyfikacji polimerami. Wiązanie jest kombinacją hydratacji i utwardzania polimeru, co może skrócić czas do użytkowania w porównaniu do czystego betonu czy grubszych wylewek cementowych. Ich tempo schnięcia i utwardzania jest mocno uzależnione od proporcji mieszanki i warunków otoczenia.
Niezależnie od rodzaju, producenci posadzek przemysłowych podają zazwyczaj karty techniczne, w których precyzują minimalny czas do różnych etapów gotowości (ruch pieszy, obciążenie lekkie, pełne obciążenie mechaniczne czy chemiczne) dla standardowych warunków laboratoryjnych (np. 23°C i 50% wilgotności względnej). Jakikolwiek odstęp od tych warunków, co w rzeczywistych warunkach budowy jest normą, spowoduje zmiany w tych czasach – zazwyczaj ich wydłużenie.
Ignorowanie specyfiki schnięcia i utwardzania danego typu posadzki to proszenie się o kłopoty; nałożenie kolejnej warstwy zbyt wcześnie na niedostatecznie suchy podkład lub puszczenie ruchu na powierzchnię, która nie osiągnęła pełnej wytrzymałości, może skutkować delaminacją, pękaniem czy trwałym uszkodzeniem. Diabeł tkwi w szczegółach i chemii materiałów.
Dla przykładu, posadzka epoksydowa na bazie rozpuszczalników może wymagać odpowiednio długiego czasu na odparowanie rozpuszczalników przed pełnym utwardzeniem polimeru, podczas gdy system bezrozpuszczalnikowy skupi się wyłącznie na reakcji chemicznej. W posadzkach cementowych kluczowe jest utrzymanie odpowiedniego nawodnienia betonu w początkowym okresie utwardzania, często poprzez pielęgnację mokrą, aby proces hydratacji przebiegł prawidłowo i osiągnięta została planowana wytrzymałość.
Grubość warstwy materiału ma bezpośredni wpływ na czas schnięcia/utwardzania, ale w różny sposób dla różnych typów posadzek. W przypadku żywic cienkowarstwowych (1-3 mm) utwardzanie następuje w całej objętości jednocześnie dzięki reakcji chemicznej, więc grubość ma mniejsze znaczenie niż w przypadku grubych płyt betonowych, gdzie transport wilgoci z głębi do powierzchni jest kluczowym i czasochłonnym procesem.
Wybór odpowiedniego systemu posadzkowego powinien uwzględniać nie tylko wymagania eksploatacyjne i estetyczne, ale także ramy czasowe projektu i warunki panujące na budowie. Czasem warto zainwestować w materiał szybkowiążący, pomimo wyższej ceny, aby przyspieszyć oddanie obiektu do użytku, ale zawsze z pełną świadomością specyfiki jego schnięcia.
Temperatura, wilgotność i wentylacja – Jak wpływają na schnięcie posadzki?
Pomyśl o posadzce jak o organizmie reagującym na otoczenie – temperatura, wilgotność powietrza i cyrkulacja powietrza (wentylacja) to kluczowe "parametry życiowe", które w dramatyczny sposób wpływają na szybkość i jakość procesu schnięcia i utwardzania. Lekceważenie tych czynników to przepis na katastrofę budowlaną, a w najlepszym wypadku, na znaczne opóźnienia w projekcie.
Temperatura działa jak katalizator dla większości reakcji chemicznych, w tym dla hydratacji cementu i polimeryzacji żywic. Wyższa temperatura oznacza szybsze wiązanie i twardnienie, co jest pożądane, gdy chcemy szybko oddać posadzkę do użytku. Jednak zbyt wysoka temperatura, szczególnie w połączeniu z niską wilgotnością i brakiem pielęgnacji, może prowadzić do zbyt szybkiego odparowania wody z mieszanki cementowej, co zakłóca hydratację i może spowodować skurcz, pękanie i zmniejszenie wytrzymałości docelowej betonu.
Niska temperatura spowalnia reakcje chemiczne, co może znacznie wydłużyć czas schnięcia i utwardzania, czasem nawet do poziomu uniemożliwiającego prawidłowe związanie materiału, zwłaszcza poniżej minimalnych temperatur podanych przez producentów (np. +5°C dla wielu systemów cementowych i żywicznych). Pamiętaj, że temperatura posadzki może być niższa niż temperatura powietrza, zwłaszcza gdy wylewana jest na zimnym gruncie lub podłożu.
Wilgotność powietrza to arcyważny gracz, zwłaszcza w przypadku materiałów opartych na wodzie, jak beton czy jastrychy cementowe. Wysoka wilgotność powietrza spowalnia odparowywanie wody z powierzchni posadzki, co w przypadku betonu jest pozytywne w początkowej fazie (sprzyja hydratacji), ale potem opóźnia wysychanie warstw głębszych, niezbędne przed nałożeniem szczelnych powłok żywicznych lub parkietu. Dla posadzek żywicznych wilgoć na podłożu może uniemożliwić prawidłowe związanie lub spowodować powstawanie pęcherzy czy delaminację, a wysoka wilgotność powietrza może zakłócić utwardzanie niektórych systemów poliuretanowych.
Z kolei zbyt niska wilgotność powietrza, szczególnie w połączeniu z wysoką temperaturą i wiatrem (przeciągiem), może prowadzić do zbyt gwałtownego wysychania powierzchni świeżego betonu. To jak wysuszenie skorupki chleba – środek jest nadal wilgotny, ale powierzchnia jest już twarda i podatna na pękanie skurczowe, tzw. rysy skurczowe, zanim masa zdąży się w pełni ułożyć i związać.
Wentylacja, czyli ruch powietrza, to nasz sprzymierzeniec w walce o optymalne warunki schnięcia. W przypadku materiałów na bazie wody, odpowiednia cyrkulacja powietrza pomaga w odprowadzaniu pary wodnej znad powierzchni, przyspieszając proces schnięcia. W przypadku posadzek żywicznych na bazie rozpuszczalników wentylacja jest wręcz niezbędna do usunięcia tych substancji z pomieszczenia i przyspieszenia utwardzania. Jednak zbyt silny wiatr może, jak wspomniano, spowodować problem zbyt szybkiego wysychania powierzchni wylewek cementowych.
Optymalne warunki do schnięcia i utwardzania większości posadzek przemysłowych to stabilna temperatura w przedziale 15-25°C i wilgotność względna powietrza 40-60%. Stosowanie nagrzewnic czy osuszaczy powietrza musi być bardzo przemyślane i kontrolowane. Nagrzewnice przyspieszają wiązanie (co jest dobre), ale jednocześnie obniżają wilgotność powietrza (co może być złe dla betonu) i przyspieszają odparowanie (co może być dobre, ale musi być skontrolowane). Osuszacze pomagają usunąć nadmiar wilgoci z powietrza i z posadzki, ale ich zbyt wczesne lub zbyt intensywne użycie na świeżym betonie jest błędem, ponieważ usuwają wodę niezbędną do hydratacji. To balansowanie na linie.
Monitorowanie tych warunków za pomocą higrometrów i termometrów to absolutna konieczność, nie żadna fanaberia. Bez kontroli warunków otoczenia nie mamy zielonego pojęcia, w jakim tempie faktycznie zachodzi proces schnięcia i utwardzania, co prowadzi do podejmowania decyzji "na oko", a to rzadko kończy się dobrze w przypadku tak kapryśnej materii budowlanej.
Pamiętajmy, że czas schnięcia betonu do stanu umożliwiającego położenie szczelnej warstwy (np. żywicy) jest często liczony według zasady "centymetr na tydzień" dla płyt grubych, schnących z jednej strony (np. na gruncie), ale to tylko bardzo, bardzo grube przybliżenie dla dobrych warunków. Rzeczywistość zawsze weryfikuje takie szacunki, a kluczowe są pomiary wilgotności w samej posadzce, a nie tylko powietrza. Metody pomiaru, takie jak metoda CM (Karbidowa) czy sondy higrometryczne umieszczane w betonie, są niezbędne do precyzyjnego określenia, kiedy wilgotność spadła do poziomu akceptowalnego dla kolejnych warstw lub użytkowania.
Podsumowując ten wątek, czas, w którym posadzka przemysłowa uzyskuje swoją docelową twardość i suchość, to wynik skomplikowanego tanga chemii materiału z fizyką otoczenia. Zrozumienie tej zależności i aktywne zarządzanie warunkami panującymi na budowie to inwestycja, która procentuje uniknięciem kosztownych błędów i przestojów.
Znaczenie grubości posadzki i składu mieszanki dla procesu schnięcia
Grubość posadzki to parametr absolutnie krytyczny, nie tylko z punktu widzenia jej nośności i odporności na obciążenia, ale również w kontekście tempa, w jakim uwalnia ona wilgoć i osiąga stan pełnego utwardzenia. Projektant konstrukcji dobiera grubość posadzki przemysłowej na podstawie przewidywanych obciążeń i specyfiki podłoża, a każde niedoszacowanie w tym zakresie zemści się w przyszłości w postaci pęknięć, paczenia czy nawet destrukcji posadzki pod wpływem ruchu czy ciężkich maszyn. Jednak z punktu widzenia schnięcia, im grubsza płyta betonowa, tym dłużej będzie trwał proces oddawania wody technologicznej z jej głębi do atmosfery.
W przypadku grubych płyt betonowych (np. 15-25 cm i więcej), woda, która nie została związana chemicznie w procesie hydratacji, musi wyparować. Droga, którą ma do przebycia wilgoć z głębi do powierzchni jest proporcjonalna do grubości. Z prostego powodu fizyki, woda poruszająca się w kapilarach betonu potrzebuje więcej czasu, aby dotrzeć do górnej warstwy i odparować. Dlatego gruba płyta 20 cm będzie schła do poziomu pozwalającego na szczelną powłokę żywiczną znacznie dłużej niż cienka, 5 cm warstwa betonu czy jastrychu. Reguła "centymetr na tydzień" jest tutaj intuicyjnie prawdziwa, choć jak wspomniano, stanowi drastyczne uproszczenie.
Problem grubości dotyczy również systemów wielowarstwowych. Jeśli mamy na przykład gruby podkład betonowy, a na nim cieńszą warstwę wylewki samopoziomującej, czas schnięcia całości będzie zależał od najwolniejszego procesu, czyli wysychania betonu do poziomu, w którym nie będzie już podbijał wilgocią warstwy wierzchniej. Puszczenie ruchu lub nałożenie szczelnej żywicy na zbyt wilgotny podkład to jak zbudowanie domu na ruchomych piaskach – katastrofa gwarantowana, często w postaci odspojenia się warstw.
Skład mieszanki betonowej lub zaprawy cementowej ma równie doniosłe znaczenie. Stosunek wodno-cementowy (w/c ratio) to fundament – im niższy (mniej wody w stosunku do cementu), tym wyższa wytrzymałość betonu (przy prawidłowej hydratacji), ale także mniej wody do odparowania, co potencjalnie może przyspieszyć schnięcie *pozostałej*, niezwiązanej wody. Jednakże, zbyt niski w/c ratio utrudnia urabialność mieszanki, co może prowadzić do problemów z zagęszczeniem.
Rodzaj cementu wpływa na kinetykę hydratacji – cementy szybkowiążące lub wysokowartościowe osiągają znaczną wytrzymałość początkową w krótszym czasie, co przyspiesza proces utwardzania, choć niekoniecznie całkowite wysychanie, ponieważ ilość wody do odparowania pozostaje podobna. Domieszki chemiczne, takie jak przyspieszacze wiązania czy plastyfikatory, również modyfikują te procesy. Przyspieszacze, jak sama nazwa wskazuje, skracają czas do momentu rozpoczęcia twardnienia, ale niekoniecznie drastycznie skracają czas do osiągnięcia docelowej, niskiej wilgotności wewnętrznej niezbędnej do położenia powłok.
Stosowanie włókien stalowych lub polimerowych jako zbrojenia rozproszonego (popularne w płytach posadzkowych zamiast siatek) wpływa przede wszystkim na kontrolę skurczu i nośność betonu. Choć same włókna nie przyspieszają znacząco procesów chemicznych schnięcia i utwardzania w całej masie, pomagają ograniczać powstawanie rys skurczowych w początkowej fazie, co pośrednio wpływa na jakość i trwałość posadzki w okresie twardnienia.
Mądry inwestor wie, że specyfikacja mieszanki betonowej czy zaprawy samopoziomującej to nie miejsce na cięcie kosztów. Dobór odpowiedniego składu, dostosowanego do grubości warstwy, przewidywanych obciążeń i warunków panujących na budowie, a następnie przestrzeganie reżimu technologicznego podczas wylewania i pielęgnacji to inwestycja w przyszłą bezproblemową eksploatację posadzki. Przykładowo, dla płyty o grubości 18 cm na gruncie, gdzie spodziewane są ciężkie wózki widłowe, błędem byłoby zastosowanie betonu klasy niższej niż C20/25 z niewłaściwym w/c ratio, co wpłynęłoby nie tylko na nośność, ale także na czas i jakość utwardzania, czyniąc całe przedsięwzięcie znacznie bardziej ryzykownym.
Zastosowanie wysokiej jakości cementu i odpowiednich domieszek może przyspieszyć osiągnięcie wczesnej wytrzymałości, ale cierpliwość jest nadal cnotą, jeśli chodzi o całkowite wyschnięcie masy betonowej, szczególnie przed aplikacją paroizolacyjnych warstw żywicznych. W praktyce budowlanej, czas do "pełnego schnięcia" betonu pod szczelne powłoki jest często określany przez wymagany minimalny wynik pomiaru wilgotności, a nie tylko przez upływ dni, co podkreśla wagę precyzyjnych badań przed podjęciem dalszych kroków.
Kiedy posadzka przemysłowa jest gotowa do użytku – Ruch pieszy a pełne obciążenie
Określenie momentu, w którym świeżo wylana posadzka przemysłowa jest gotowa do eksploatacji, to jedno z najważniejszych, a zarazem najbardziej stresujących pytań na budowie. "Gotowość" to nie jednorodny stan, lecz seria progów, które materiał musi przekroczyć, zależnie od tego, jaki rodzaj obciążenia ma na nim spocząć. Kluczowe rozróżnienie dotyczy gotowości do ruchu pieszego versus gotowości do pełnego obciążenia, mechanicznego lub chemicznego.
Ruch pieszy to zazwyczaj pierwszy test wytrzymałości dla świeżej posadzki. Oznacza to możliwość bezpiecznego chodzenia po powierzchni bez ryzyka trwałego uszkodzenia, wgnieceń czy zatarcia. Ten próg jest osiągany stosunkowo szybko – dla posadzek żywicznych cienkowarstwowych (np. epoksydowych czy poliuretanowych) może to być już po 12-24 godzinach w optymalnych warunkach temperaturowych (około 20°C). W przypadku wylewek cementowych samopoziomujących, czas ten wynosi zazwyczaj 24-72 godziny. Grubsze posadzki betonowe (płyty) osiągają ten etap po 24-48 godzinach od wylania, o ile proces wiązania przebiega prawidłowo.
Gotowość do ruchu pieszego oznacza jedynie, że posadzka ma już wystarczającą spójność powierzchniową, aby wytrzymać ciężar człowieka. Absolutnie nie oznacza to gotowości na wjazd wózka widłowego, upadek ciężkiego przedmiotu czy długotrwałe składowanie towarów. Przyznanie zgody na ruch pieszy jest często sygnałem dla ekipy do rozpoczęcia prac wykończeniowych, takich jak szlifowanie czy przygotowanie powierzchni pod kolejne warstwy, ale nadal wymaga ostrożności.
Pełne obciążenie to zupełnie inna liga i wymaga osiągnięcia przez posadzkę znaczącej części jej docelowej wytrzymałości mechanicznej i/lub chemicznej. To moment, kiedy po powierzchni mogą swobodnie poruszać się ciężkie maszyny, wózki widłowe z ładunkiem, składowane mogą być palety z towarem, a posadzka jest odporna na substancje chemiczne, dla których została zaprojektowana. Ten etap następuje znacznie później.
Dla posadzek żywicznych czas do pełnego obciążenia mechanicznego i chemicznego wynosi zazwyczaj od 3 do 7 dni od aplikacji w standardowych warunkach. Niektóre specjalistyczne systemy mogą wymagać dłuższego okresu, zwłaszcza gdy kluczowa jest pełna odporność chemiczna na agresywne substancje. Zbyt wczesne narażenie niedostatecznie utwardzonej żywicy na ciężkie obciążenia może prowadzić do deformacji, zarysowań, a nawet pęknięć.
W przypadku posadzek betonowych, czas do osiągnięcia pełnej wytrzymałości (np. klasy C25/30) wynosi standardowo 28 dni. Oznacza to, że przez cały ten okres (a nawet dłużej, jeśli warunki były niesprzyjające) beton wciąż "dojrzewa" i zwiększa swoją nośność. Ruch ciężkich pojazdów czy składowanie bardzo dużych ciężarów przed upływem tego okresu jest ryzykowną grą, która może skutkować trwałym uszkodzeniem strukturalnym płyty, którego naprawa będzie kosztować krocie.
Co więcej, "pełne obciążenie" dla posadzek betonowych wymaga również osiągnięcia odpowiednio niskiego poziomu wilgotności wewnętrznej, jeśli na wierzchu mają być zastosowane szczelne powłoki żywiczne, wykładziny PCV czy parkiety. Jak wspomniano, czas schnięcia betonu pod szczelne powłoki to zupełnie inny proces niż samo utwardzanie i może trwać tygodnie lub nawet miesiące (zasada "centymetr na tydzień" razy grubość w cm, to z grubsza ilość tygodni potrzebnych do wyschnięcia do około 4-5% wilgotności CM). Ignorowanie tego wymagania to najczęstsza przyczyna problemów z powłokami żywicznymi czy innymi szczelnymi wykończeniami, które "oddychają" wilgoć spod spodu, prowadząc do pęcherzy i odspojenia.
Z tego powodu, planowanie harmonogramu prac na hali przemysłowej musi uwzględniać nie tylko czas potrzebny na wykonanie posadzki, ale przede wszystkim realny czas jej schnięcia i utwardzania do wymaganego poziomu gotowości dla planowanej eksploatacji. Pospiech w tym procesie to oszczędność groszy, która może kosztować miliony w przyszłości. Jak mawia stare porzekadło – "kto szybko daje, dwa razy daje", a w budownictwie przemysłowym "kto za szybko wjeżdża, ten płaci podwójnie za naprawy".
Producenci posadzek zazwyczaj jasno określają na kartach technicznych, po jakim czasie od aplikacji dany system osiąga poszczególne etapy gotowości – np. ruch pieszy po X godzinach, ruch lekki (wózki paletowe bez ładunku) po Y godzinach, ruch ciężki (wózki widłowe z ładunkiem) po Z dniach, pełna odporność chemiczna po W dniach. Te dane są jednak podane dla idealnych warunków laboratoryjnych. W realnych warunkach budowy, wahania temperatury i wilgotności, a także specyfika samego podłoża, mogą znacznie wydłużyć te czasy. Zawsze warto pytać wykonawcę i producenta o rekomendacje dla konkretnych warunków panujących na budowie i nie skracać tych okresów "na siłę", nawet pod presją terminów.
Testy wytrzymałości mechanicznej (np. sczepności dla cienkowarstwowych powłok, wytrzymałości na ściskanie dla betonu) oraz pomiary wilgotności są najlepszymi, obiektywnymi metodami oceny faktycznej gotowości posadzki do kolejnych etapów prac lub pełnego użytkowania. Podejmowanie decyzji tylko w oparciu o wizualne oględziny czy czas, który upłynął od wylewania, jest wysoce nierozsądne i często prowadzi do poważnych problemów eksploatacyjnych w niedalekiej przyszłości.