Jak wybrać najlepszą izolację termiczną pod panele w 2025?
Marzysz o podłodze, która nie tylko będzie wyglądać pięknie, ale też zagwarantuje przyjemne ciepło pod stopami i ciszę domowego ogniska? Wybór odpowiedniego podkładu pod panele to często niedoceniany krok, a przecież to on stanowi niewidzialnego bohatera komfortu termicznego i akustycznego twojego wnętrza; poszukując optymalnego rozwiązania, wielu zastanawia się: jaka jest Najlepsza izolacja termiczna pod panele? W gąszczu dostępnych na rynku materiałów, od prostych pianek po zaawansowane maty, kluczem do sukcesu okazuje się dopasowanie podkładu nie tylko do budżetu, ale przede wszystkim do warunków panujących na podłożu oraz oczekiwań mieszkańców. Z naszego analitycznego punktu widzenia, podchodząc do tematu bez ogródek, śmiało możemy stwierdzić, że najbardziej efektywne parametry w zakresie termoizolacji osiągają materiały takie jak podkład z polistyrenu ekstrudowanego (XPS) oraz nowoczesne maty kwarcowe, deklasując pod tym względem tradycyjne, tanie pianki. To właśnie te materiały stanowią rdzeń rozwiązania dla tych, którzy ponad wszystko cenią sobie realną, odczuwalną izolację termiczną. Wybór wydaje się więc pozornie prosty, ale diabeł tkwi w szczegółach – warunki podłoża, ogrzewanie podłogowe czy poziom wymaganego wyciszenia potrafią znacząco zmienić reguły gry. Czy jesteś gotów odkryć, który z nich skrywa tajemnicę twojego komfortu?
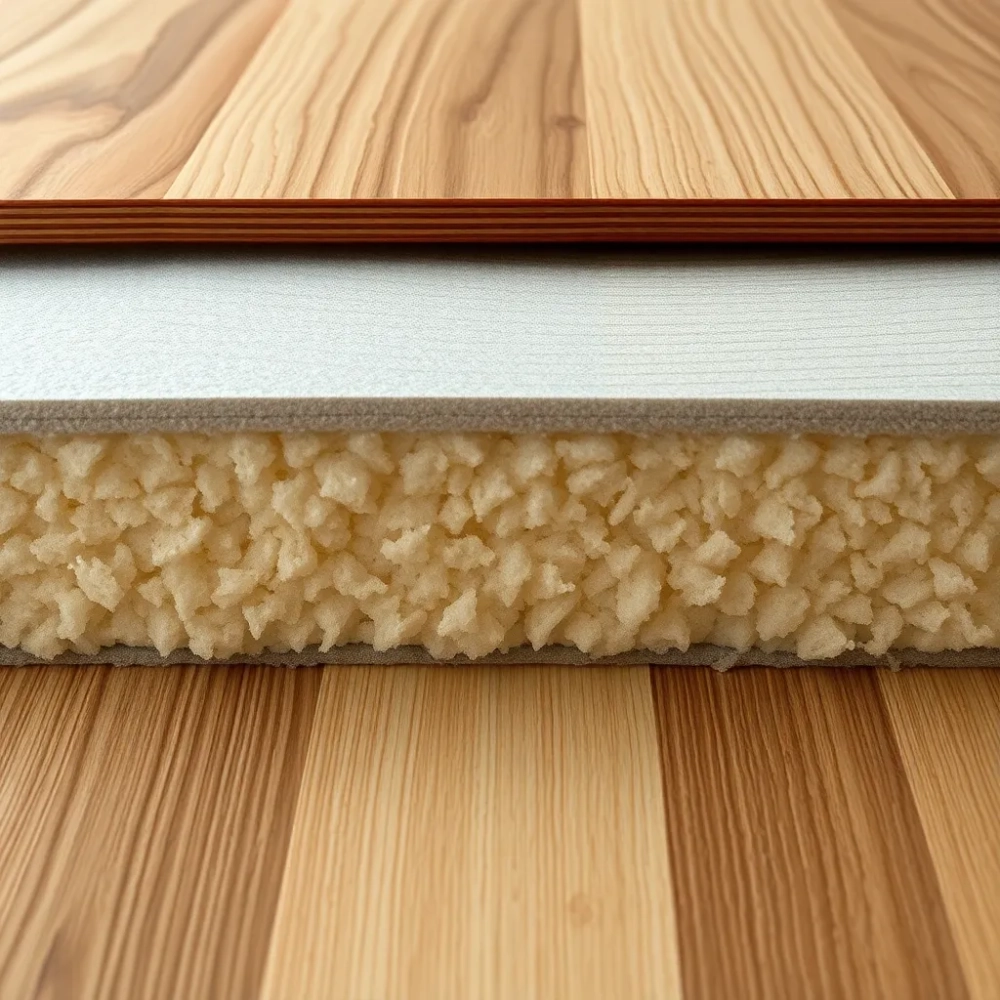
Aby rzucić nieco więcej światła na parametry kluczowych materiałów stosowanych pod panele, przyjrzyjmy się danym technicznym. Poniższa tabela zestawia wybrane właściwości popularnych podkładów, co pomoże zrozumieć, dlaczego niektóre materiały przodują w kwestii izolacji termicznej, a inne lepiej radzą sobie z dźwiękiem czy wilgocią.
Typ materiału | Współczynnik przewodzenia ciepła λ [W/(m·K)] | Wskaźnik redukcji dźwięków uderzeniowych ∆Lw [dB] | Odporność na ściskanie LCP [kPa] | Odporność na wilgoć |
---|---|---|---|---|
Pianka polietylenowa (PE) | ~0.045 - 0.055 | ~17 - 19 | ~10 - 20 | Średnia (zależnie od struktury) |
Polistyren ekstrudowany (XPS) | ~0.030 - 0.035 | ~19 - 21 | ~200 - 400+ | Wysoka |
Korek naturalny | ~0.040 - 0.050 | ~18 - 20 | ~60 - 100 | Umiarkowana (wchłania, ale oddaje) |
Mata kwarcowa | ~0.035 - 0.040 | ~20 - 22 (często więcej) | ~400+ | Wysoka (często zintegrowana bariera) |
Ekopłyta (włókno drzewne/karton) | ~0.045 - 0.050 | ~18 - 19 | ~50 - 80 | Niska (silnie wchłania wilgoć) |
Analizując powyższe dane, nietrudno zauważyć, że wartości współczynnika przewodzenia ciepła λ stanowią kluczowy wyznacznik potencjału termoizolacyjnego danego materiału – im niższa ta wartość, tym lepiej. Materiały takie jak XPS i mata kwarcowa wyraźnie wyróżniają się na tle konkurencji, oferując najniższe wartości λ, co przekłada się na minimalne straty ciepła w dół, kierując je w stronę pomieszczenia, a nie nieogrzewanej kondygnacji poniżej. To konkretna, mierzalna różnica, która może wpłynąć na komfort użytkowania podłogi, zwłaszcza w chłodniejszych miesiącach, oraz realnie obniżyć rachunki za ogrzewanie w dłuższej perspektywie.
Podkład Pod Panele A Warunki Podłoża (Piwnica, Grunt)
Wybór odpowiedniego podkładu pod panele to nie jest gra w zgadywanie, zwłaszcza gdy mowa o specyficznych warunkach podłoża, takich jak te panujące bezpośrednio nad piwnicą czy gruntem. Tutaj nie wystarczy "cokolwiek", tu trzeba myśleć strategicznie i, bądźmy szczerzy, patrzeć przyszłościowo, aby uniknąć kosztownych błędów w niedalekiej przyszłości; bagatelizowanie tego aspektu to jak budowanie domu na piasku, co wcześniej czy później skończy się katastrofą.
Gdy pod naszą przyszłą podłogą z paneli znajduje się nieogrzewana piwnica lub, co gorsza, zaledwie izolacja od gruntu, priorytetem numer jeden staje się nie tylko odpowiednie podparcie dla systemu click, ale przede wszystkim maksymalizacja izolacji termicznej i, co absolutnie kluczowe, stuprocentowa ochrona przed wilgocią; to jak mur obronny, który musi powstrzymać atak zimna i mokradeł.
W takich warunkach, materiały o słabej odporności na wilgoć, takie jak popularna i ekonomiczna ekopłyta wykonana z włókien drzewnych czy tektury, są w zasadzie zdyskwalifikowane na starcie – niczym zawodnik bez kondycji na maratonie, po prostu nie wytrzymają próby czasu i specyficznych warunków. Nawet jeśli początkowo wydają się wystarczające, ich tendencja do wchłaniania wody z powietrza czy podłoża sprawi, że w krótkim czasie stracą swoje właściwości i, co gorsza, staną się pożywką dla pleśni, dewastując panele od spodu. Widziałem takie przypadki, w których podłoga po dwóch latach nad piwnicą dosłownie "kwitła" od wilgoci i zagrzybienia, a właściciel musiał zrywać całą inwestycję.
Równie ryzykownym wyborem w kontekście wilgoci i termoizolacji okazuje się najtańsza tekstura falista czy popularna pianka polietylenowa, które charakteryzują się bardzo niską gęstością i otwartą lub półotwartą strukturą komórkową, co czyni je łatwo przepuszczalnymi dla pary wodnej. Ich współczynnik przewodzenia ciepła (λ) często przekracza 0.050 W/(m·K), co w przypadku zimnego podłoża oznacza znaczące straty ciepła z pomieszczenia, sprawiając, że podłoga pozostaje nieprzyjemnie chłodna; to jak wkładanie dziurawego swetra na mróz.
Decydując się na podłogę nad piwnicą lub gruntem, konieczne jest zastosowanie podkładu o doskonałej izolacji termicznej (niski λ) oraz bardzo wysokiej, wręcz absolutnej odporności na wilgoć; musimy postawić na materiał, który stworzy szczelną barierę i jednocześnie nie pozwoli ciepłu uciekać w dół. Materiały o strukturze zamkniętokomórkowej, które nie wchłaniają wody, wydają się tutaj jedyną sensowną opcją, stanowiąc pierwszą linię obrony. Grubość materiału także ma znaczenie, im grubiej tym cieplej, ale nie bezgranicznie, gdyż musimy utrzymać stabilność całej konstrukcji podłogi i nie przekraczać limitów tolerancji systemów click. Optymalna grubość często oscyluje w granicach 5-9 mm dla XPS w takich zastosowaniach, oferując realne podniesienie oporu cieplnego podłogi o wartość rzędu 0.15 - 0.25 m²K/W. To może nie brzmieć dramatycznie, ale w skali całego roku i przy dużym metrażu, robi odczuwalną różnicę zarówno w komforcie, jak i portfelu.
Polistyren ekstrudowany (XPS) jawi się jako jeden z głównych kandydatów do zastosowania w takich trudnych warunkach; jego zamkniętokomórkowa struktura gwarantuje minimalną absorpcję wody, a niski współczynnik λ (ok. 0.030-0.035 W/(m·K)) zapewnia solidną izolację termiczną. Dostępne na rynku płyty XPS, często o wymiarach 120x60 cm lub 100x50 cm i grubości od 3 mm do 9 mm (choć do piwnic warto celować w grubsze), są relatywnie sztywne (LCP 200-400+ kPa), co dodatkowo stabilizuje podłogę i redukuje ryzyko łamania się zamków paneli. Cena XPS waha się typowo od 15 do 35 PLN/m² w zależności od grubości i producenta, co czyni go atrakcyjnym cenowo rozwiązaniem biorąc pod uwagę oferowane korzyści.
Alternatywą o znakomitych parametrach, choć zazwyczaj droższą, jest mata kwarcowa, która często posiada zintegrowaną barierę przeciwwilgociową; to kompletne rozwiązanie typu "wszystko w jednym", eliminujące potrzebę układania dodatkowej folii paroizolacyjnej, co upraszcza montaż. Mata kwarcowa, wykonana z mieszanki mineralnej z polimerami (np. PUR), oferuje nie tylko świetne właściwości termiczne (λ rzędu 0.035-0.040 W/(m·K)), ale także niezrównaną sztywność (LCP powyżej 400 kPa), co jest kluczowe przy niwelowaniu drobnych nierówności podłoża. Koszt maty kwarcowej zazwyczaj wynosi od 40 do nawet 80 PLN/m², co jest inwestycją, ale patrząc na jej wszechstronność (izolacja, sztywność, wilgoć, akustyka – często oferuje świetną redukcję dźwięków uderzeniowych ∆Lw > 20 dB), może być uzasadniona. Mata kwarcowa o grubości 3mm może dać podobny opór cieplny jak 5mm XPS, co warto brać pod uwagę przy limitowanej przestrzeni. Pamiętajmy, że szczelne połączenie arkuszy materiału izolacyjnego i zabezpieczenie dylatacji na obwodzie pomieszczenia jest równie ważne co sam materiał – mostki termiczne i akustyczne oraz nieszczelności w barierze paroizolacyjnej potrafią zniweczyć efekty najlepszej izolacji.
A co z naturalnym korkiem, często wymienianym jako materiał pro-ekologiczny? W przypadku podłoży o podwyższonej wilgotności, takich jak piwnica czy grunt, korek ekspandowany (zwykle o λ rzędu 0.040-0.050 W/(m·K) i LCP rzędu 60-100 kPa) bywa rekomendowany jako "sprawdzony naturalny podkład", jednakże ma on ograniczoną odporność na wilgoć w porównaniu do XPS czy maty kwarcowej; korek potrafi absorbować wilgoć z powietrza i oddawać ją, co w suchym środowisku jest zaletą (regulacja mikroklimatu), ale w piwnicy może stać się problemem. Jego struktura komórkowa, choć porowata, nie jest tak hermetyczna jak zamknięte komórki XPS, co sprawia, że nie stanowi tak niezawodnej bariery dla pary wodnej napierającej od dołu, chyba że zastosuje się dodatkową, skuteczną folię paroizolacyjną o wysokim współczynniku oporu dyfuzyjnego Sd (> 100 m). Grubość korka pod panele waha się zwykle od 2 do 5 mm, a jego cena to zazwyczaj 15-30 PLN/m²; warto jednak być świadomym jego ograniczeń wilgotnościowych w kontekście specyficznych podłoży, aby uniknąć rozczarowania. Właściwy wybór podkładu nad chłodnym lub wilgotnym podłożem to podjęcie decyzji, która na lata zdefiniuje komfort użytkowania podłogi i zabezpieczy inwestycję przed destrukcyjnym wpływem czynników zewnętrznych. Ignorowanie tej wiedzy to zaproszenie do problemów.
Podkład Pod Panele A Ogrzewanie Podłogowe
Projektowanie podłogi z paneli laminowanych czy winylowych (LVT), gdy pod nią ma funkcjonować ogrzewanie podłogowe, to sztuka wymagająca precyzji i zrozumienia fizyki; tutaj liczy się każdy milimetr i każdy współczynnik, a błąd w wyborze podkładu może drastycznie obniżyć efektywność całego systemu grzewczego lub, co gorsza, doprowadzić do przegrzewania materiału paneli i ich trwałego uszkodzenia. Niektórzy myślą: "aby było ciepło, musi być gruby podkład", co w przypadku ogrzewania podłogowego jest dramatycznie błędnym założeniem i często kończy się marnowaniem energii i pieniędzy.
Fundamentalną zasadą przy podkładach pod panele nad ogrzewaniem podłogowym jest minimalizacja oporu cieplnego całej warstwy podłogi; chcemy, aby ciepło generowane w rurach lub przewodach grzewczych jak najszybciej i jak najskuteczniej przenikało do pomieszczenia, a nie było "więzione" pod panelami. Dlatego całkowity opór cieplny R (wyrażany w m²K/W) sumy panel + podkład nie powinien przekraczać wartości około 0.15 m²K/W; ta wartość jest często maksymalną dopuszczalną przez producentów paneli przy systemach ogrzewania podłogowego. Wartość oporu cieplnego R dla panelu laminowanego 8mm wynosi zazwyczaj ok. 0.05 - 0.07 m²K/W, co oznacza, że na podkład pozostaje nam margines R rzędu 0.08 - 0.10 m²K/W.
Materiały charakteryzujące się bardzo niskim współczynnikiem przewodzenia ciepła (niskim λ), choć pożądane dla tradycyjnej izolacji termicznej "w dół", stają się problemem w przypadku ogrzewania podłogowego, ponieważ stawiają duży opór dla przepływu ciepła "w górę", do pomieszczenia. Z tego powodu gruby korek (λ ok. 0.040-0.050 W/(m·K), ale R rośnie z grubością) jest generalnie odradzany; jeśli już musimy zastosować korek, to jedynie w najcieńszej dostępnej wersji, np. 2 mm, co daje opór cieplny R rzędu (0.002 m / 0.045 W/(m·K)) ≈ 0.044 m²K/W – wartość, która mieści się jeszcze w dopuszczalnych normach, ale wciąż jest stosunkowo wysoka w porównaniu do dedykowanych rozwiązań. Grubości powyżej 2 mm dla korka szybko przekroczą dopuszczalny opór cieplny.
Co zatem wybrać? Idealny podkład pod ogrzewanie podłogowe musi mieć niski opór cieplny (wysokie λ), jednocześnie zachowując niezbędną wytrzymałość na ściskanie (LCP), aby chronić zamki paneli przed deformacją spowodowaną rozszerzalnością termiczną. Grubość podkładu nie powinna generalnie przekraczać 3 mm, aby zminimalizować opór cieplny i zachować stabilność konstrukcji; to jest absolutna, nieprzekraczalna granica dla większości systemów, choć niektórzy producenci dopuszczają specyficzne materiały o grubości do 5 mm, ale z ekstremalnie niskim oporem. Na przykład, podkład o grubości 3mm i współczynniku λ = 0.045 W/(m·K) ma opór cieplny R = (0.003 m / 0.045 W/(m·K)) ≈ 0.067 m²K/W, co w połączeniu z panelem daje sumaryczny opór około 0.12-0.14 m²K/W – jest to w normie, ale blisko górnej granicy. Natomiast podkład o grubości 3mm i λ = 0.030 W/(m·K) miałby opór R = (0.003 m / 0.030 W/(m·K)) = 0.100 m²K/W, co jest zdecydowanie za dużo.
Materiałem, który charakteryzuje się niskim oporem cieplnym i jest często stosowany pod ogrzewanie, jest cienka, np. 1.5 mm, pianka polietylenowa lub specjalistyczne maty polietylenowe ze strukturą falistą (λ wysokie ok. 0.055 W/(m·K)). Opór cieplny takiej pianki 1.5mm wynosi R = (0.0015 m / 0.055 W/(m·K)) ≈ 0.027 m²K/W. Tak niski opór cieplny sprzyja przenikaniu ciepła do pomieszczenia i sprawdza się w sytuacji bardzo ograniczonego budżetu. Musimy jednak pamiętać o ich słabej odporności na ściskanie (LCP 10-20 kPa), co w dłuższej perspektywie może prowadzić do uszkodzeń zamków paneli, oraz o braku jakiejkolwiek bariery przeciwwilgociowej, co wymaga dodatkowego użycia folii paroizolacyjnej. "Czujesz to ciepło? Fajnie. A za rok będziesz czuł 'klik-klik' i szukał rozchodzących się desek, bo na podkładzie oszczędziłeś grosze" – taka historia to niestety norma.
Bardziej zaawansowane i godne polecenia rozwiązania to specjalne maty kwarcowe lub podkłady XPS dedykowane pod ogrzewanie podłogowe; charakteryzują się one wysokim współczynnikiem przewodzenia ciepła (czyli niskim oporem termicznym jak na swoją grubość, np. 3mm mata kwarcowa o λ = 0.035 W/(m·K) ma R=0.086 m²K/W, a niektóre specjalne maty do ogrzewania mają λ nawet 0.07 W/(m·K), dając R=0.043 m²K/W dla 3mm!), znakomitą odpornością na ściskanie (LCP 400+ kPa), która radzi sobie z naprężeniami termicznymi, oraz często posiadają zintegrowaną barierę przeciwwilgociową, co jest olbrzymim plusem. Na przykład, mata kwarcowa typu 15DB o grubości 3 mm i oporze cieplnym około 0.045 - 0.050 m²K/W jest świetnym, kompleksowym rozwiązaniem, łączącym optymalne przewodnictwo cieplne z wytrzymałością i ochroną przeciwwilgociową, kosztującym zwykle w przedziale 40-70 PLN/m². Dostępne są też cienkie (np. 1.6 mm) podkłady XPS ze zintegrowaną folią, oferujące bardzo niski opór termiczny rzędu 0.03 m²K/W i LCP 200+ kPa za około 25-40 PLN/m². Takie rozwiązania zapewniają, że ciepło dotrze tam, gdzie ma dotrzeć – do twojego pokoju, a nie zostanie "po drodze" stłumione przez niewłaściwie dobrany materiał, a podłoga pozostanie stabilna przez lata. Odpowiedni podkład pod ogrzewanie podłogowe to inwestycja w efektywność systemu grzewczego i trwałość podłogi.
Znaczenie Izolacji Przeciwwilgociowej Pod Panele
Ignorowanie kwestii izolacji przeciwwilgociowej pod panelami laminowanymi to proszenie się o kłopoty, i to wcale nie małe. Panel laminowany, choć na wierzchu twardy i odporny na ścieranie, w swojej rdzeniowej warstwie z płyty HDF (High Density Fibreboard) jest niezwykle wrażliwy na wilgoć; jej przenikanie, czy to w postaci pary wodnej z podłoża, czy rozlanego płynu, może prowadzić do puchnięcia, wypaczania, a w efekcie trwałego uszkodzenia paneli. Zabezpieczenie podłogi przed wilgocią jest absolutnym fundamentem trwałości i estetyki na lata, a zaniedbanie tego etapu to jak malowanie obrazu na podartej płótnie – wysiłek na nic.
Problem wilgoci staje się palący w pomieszczeniach, gdzie posadzka znajduje się bezpośrednio nad gruntem lub nieocieploną, potencjalnie wilgotną piwnicą; w takich miejscach zjawisko podciągania kapilarnego wody z gruntu czy naturalne odparowywanie wilgoci z betonu jest czymś absolutnie realnym, co trzeba bezwzględnie zneutralizować. Nowa wylewka betonowa schnie nawet miesiąc na każdy centymetr grubości, wydzielając olbrzymie ilości wody – kładzenie paneli bez odpowiedniego odczekania i zabezpieczenia to czyste szaleństwo; w takiej sytuacji miernik wilgotności betonu jest twoim najlepszym przyjacielem.
Standardową barierę przeciwwilgociową pod panele laminowane, układaną bezpośrednio na wylewce przed położeniem podkładu i paneli, stanowi folia polietylenowa (PE) o grubości co najmniej 0.2 mm (200 mikronów); ważne, aby miała ona odpowiednio wysoki współczynnik oporu dyfuzyjnego Sd (często powyżej 70 m), co gwarantuje skuteczne zablokowanie pary wodnej. Kluczem jest dokładne ułożenie folii z zakładem minimum 20 cm na łączeniach i wywinięciem na ściany na wysokość listwy przypodłogowej; każde niedociągnięcie, każda dziurka to potencjalna ścieżka dla wilgoci. Koszt takiej folii to zaledwie 1-3 PLN/m², co czyni ją niezwykle opłacalną inwestycją w bezpieczeństwo podłogi.
Niektóre rodzaje podkładów, zwłaszcza te przeznaczone do trudnych warunków lub pod ogrzewanie podłogowe, posiadają już zintegrowaną barierę przeciwwilgociową – to eleganckie i efektywne rozwiązanie, eliminujące dodatkowy etap montażu folii; typowe przykłady to zaawansowane maty kwarcowe czy wybrane podkłady XPS, np. mata kwarcowa typu 15DB ze zintegrowaną barierą lub produkt typu MEISTER. MEISTER ze zintegrowaną barierą przeciw wilgoci jest przykładem kompleksowego podkładu, który w jednej warstwie łączy właściwości tłumiące dźwięki (do 25 dB, odgłos kroków do 19dB) z doskonałą izolacją przeciwwilgociową dzięki zastosowaniu mieszanki mineralnej PUR ze zintegrowaną taśmą aluminiową do szczelnego łączenia; takie rozwiązania minimalizują ryzyko błędu montażowego i zapewniają solidne zabezpieczenie, choć ich cena (często 40-80 PLN/m²) jest odpowiednio wyższa. To trochę jak system all-inclusive w hotelu – płacisz więcej, ale masz wszystko pod kontrolą bez dodatkowych kłopotów.
Materiały, które nie zapewniają własnej izolacji przeciwwilgociowej i wymagają bezwzględnie użycia dodatkowej folii, to większość pianek polietylenowych, ekopłyta (charakteryzująca się co prawda chłonnością, ale nie jest to kontrolowane pochłanianie wilgoci, raczej destrukcyjne nasiąkanie), korek naturalny (szczególnie w wersjach niewoskowanych), a także najprostsza tekstura falista. Ich niska odporność na wilgoć wynika z porowatej struktury lub braku szczelności, co sprawia, że para wodna łatwo przez nie przenika do paneli, o czym wspominaliśmy wcześniej w kontekście podłoża typu piwnica/grunt. Układanie tych materiałów bezpośrednio na betonie czy innym podłożu, z którego może emanować wilgoć, bez odpowiedniej warstwy paroizolacyjnej, to po prostu akt sabotażu na własnej podłodze.
Podsumowując, odporność na wilgoć podkładu jest nie tylko ważnym, ale wręcz fundamentalnym aspektem, który należy wziąć pod uwagę, dokonując wyboru podkładu pod panele; nawet najlepszy podkład termiczny czy akustyczny nie uratuje podłogi przed zniszczeniem, jeśli wilgoć wedrze się od spodu. Koszt zabezpieczenia przeciwwilgociowego, czy to przez folię PE (ok. 1-3 PLN/m²), czy przez wybór podkładu ze zintegrowaną barierą (które same w sobie są droższe, ale koszt dodatkowej folii jest w nie "wliczony"), jest znikomy w porównaniu z potencjalnymi kosztami wymiany całej podłogi; to polisa ubezpieczeniowa dla twoich paneli, której absolutnie nie wolno pomijać. Pamiętajmy, że wilgoć to cichy zabójca podłóg – działa powoli, niezauważalnie, a efekty jej działania są często opłakane. Szczególną uwagę należy zwrócić na wilgotność resztkową wylewki betonowej (<2% dla wylewki cementowej, <0.5% dla anhydrytowej), co można zmierzyć higrometrem CM lub metodą karbidową; przed położeniem paneli, poziom wilgoci musi być poniżej dopuszczalnych wartości. Używanie popularnych, tanich testerów "paluszkowych" jest niewystarczające, a wręcz mylące – to narzędzia pomocnicze, nie zastępują profesjonalnego pomiaru. Nie bądź bohaterem na skróty – zainwestuj w spokój i trwałość. Pamiętajmy, że dobrze wykonana izolacja przeciwwilgociowa to absolutna podstawa każdej trwałej podłogi z paneli.
Termiczna Czy Akustyczna? Wybór Izolacji Pod Panele
Wybór odpowiedniego podkładu pod panele to często dylemat, który sprowadza się do pytania: czego tak naprawdę oczekuję od tej podłogi – przede wszystkim ciepła pod stopami czy błogiej ciszy? Prawda jest taka, że podkład pod panele to wielofunkcyjny element, pełniący jednocześnie role izolacji termicznej, akustycznej i, co równie ważne, wyrównującej drobne nierówności podłoża i zwiększającej trwałość samego panelu poprzez poprawę parametru LCP (Load Compression Property - odporność na ściskanie); mądry wybór to kompromis szyty na miarę potrzeb konkretnego wnętrza. Nie istnieje jedno "najlepsze" rozwiązanie dla wszystkich, choć niektóre materiały wyraźnie przodują w poszczególnych kategoriach, a rzadko kiedy jeden produkt jest absolutnie najlepszy we wszystkim.
Jeśli głównym problemem w twoim wnętrzu jest przenikanie chłodu od dołu – typowy scenariusz dla parterów nad piwnicami, mieszkań na dole kamienic czy po prostu domów z niedostateczną izolacją fundamentów – wtedy na pierwszy plan wysuwa się parametr izolacyjności termicznej, mierzony współczynnikiem λ; im niższa jego wartość, tym lepiej podkład "blokuje" ucieczkę ciepła. W tej kategorii bezapelacyjnie królują materiały o strukturze zamkniętokomórkowej, takie jak polistyren ekstrudowany (XPS) o niskim λ (np. 0.030 W/(m·K)) lub dedykowane maty kwarcowe (np. 0.035 W/(m·K)); to one dostarczą odczuwalne ciepło pod stopami, zwiększając komfort użytkowania pomieszczenia, zwłaszcza w strefach, gdzie spędza się dużo czasu w pozycji siedzącej lub leżącej. Grubsza warstwa (np. 5-9 mm dla XPS) w pomieszczeniach bez ogrzewania podłogowego jeszcze bardziej poprawi ten efekt, zwiększając opór cieplny (R = grubość / λ). Pomyśl o tym jak o grubym swetrze w zimny dzień – λ to rodzaj materiału, a grubość to... no, grubość swetra.
Jednak równie często palącą potrzebą w nowoczesnych mieszkaniach, zwłaszcza w budownictwie wielorodzinnym, jest redukcja hałasu. Mówimy tu o dwóch rodzajach dźwięków: dźwięki powietrzne (rozmowy, muzyka, TV), które panel laminowany generalnie słabo tłumi sam w sobie, oraz dźwięki uderzeniowe (odgłos kroków, spadających przedmiotów, przesuwanych mebli), które przenoszą się przez konstrukcję podłogi do pomieszczenia poniżej – to właśnie te drugie są prawdziwą zmorą sąsiadów z dołu. Rola podkładu w tej kwestii jest nie do przecenienia – to on amortyzuje uderzenia i pochłania część energii akustycznej; parametr opisujący tę zdolność to wskaźnik redukcji dźwięków uderzeniowych ∆Lw (dB). Im wyższa jego wartość, tym lepsze wyciszenie. Panuje powszechne mylne przekonanie, że grubość podkładu automatycznie oznacza lepszą izolację akustyczną – niestety, to nie grubość jest tu kluczowa, a struktura i materiał podkładu. Widziałem wiele podłóg z grubą, ale kiepskiej jakości pianką, które rezonowały przy każdym kroku jak bęben.
Na rynku dostępne są podkłady o bardzo zróżnicowanych parametrach akustycznych. Najsłabsze wyniki w zakresie tłumienia dźwięków uderzeniowych (< 19 dB) osiągają najtańsze rozwiązania – wspomniana już tekstura falista, cienkie pianki polietylenowe oraz ekopłyta. Choć bywają atrakcyjne cenowo (często poniżej 10 PLN/m²), ich LCP jest niskie (10-80 kPa), co prowadzi do odkształceń pod obciążeniem i skrzypienia paneli, a izolacja akustyczna jest, mówiąc delikatnie, symboliczna; kupując taki podkład, "oszczędzasz" na rachunkach za ogrzewanie (słaba termika w dół) i... fundujesz sobie i sąsiadom niezłe akustyczne widowisko. Należy też pamiętać, że nawet 3-4 mm taniej pianki PE ma często gorsze właściwości akustyczne niż 1.5 mm lepszego materiału. Prawdziwa akustyczna izolacja pod panele zaczyna się od materiałów, które skutecznie absorbują i tłumią drgania.
Znacznie lepiej od dźwięku odbitego (tego, co słyszymy w pomieszczeniu) i uderzeniowego (tego, co słyszą sąsiedzi) radzą sobie materiały o bardziej zaawansowanej strukturze: korek naturalny (∆Lw typowo 18-20 dB), grubsze warianty podkładu pod panele XPS (np. 5mm XPS potrafi osiągnąć ∆Lw rzędu 19-21 dB, a 9mm nawet 22-23 dB, a co ważne, XPS dobrze redukuje dźwięki odbite w pomieszczeniu, dzięki czemu pokój staje się "cichszy" w odbiorze) oraz, co najważniejsze, maty kwarcowe. Maty kwarcowe, zwłaszcza te grubsze (np. 3 mm i więcej), należą do czołówki w kwestii izolacji akustycznej, często osiągając ∆Lw na poziomie 20-22 dB, a dedykowane produkty, takie jak typ MEISTER 25 DB, są w stanie zredukować poziom hałasu w pomieszczeniu do 31%, a odgłos kroków (dźwięki uderzeniowe) do imponujących 19 dB – to jest wartość mierzonego hałasu PRZENIKAJĄCEGO DO SĄSIADÓW Z DOŁU! Mówimy tu o realnym zmniejszeniu głośności o połowę lub więcej w stosunku do taniej pianki. Cena korka to ok. 15-30 PLN/m², XPS 15-35 PLN/m², a mat kwarcowych i dedykowanych produktów jak MEISTER 25 DB to często 40-80 PLN/m² - inwestycja w komfort swój i sąsiadów.
Produkty takie jak MEISTER 25 DB o grubości ok. 3 mm, wykonane z mieszanki mineralnej PUR (poliuretanu i minerałów) ze zintegrowaną barierą przeciw wilgoci i taśmą aluminiową, to przykład kompleksowego podejścia; łączą wysoką redukcję dźwięków uderzeniowych (∆Lw do 25 dB, odgłos kroków do 19dB) ze znakomitą sztywnością (bardzo wysokie LCP), która chroni zamki paneli i wyrównuje podłoże, a także dobrą izolacją termiczną jak na swoją grubość. LCP, parametr opisujący zdolność materiału do zachowania grubości pod obciążeniem, jest kluczowy zwłaszcza w przypadku systemów "click" w panelach laminowanych i LVT – niski LCP (< 100 kPa) oznacza, że podkład będzie się uginał w miejscach nacisku, prowadząc do "pływania" podłogi, skrzypienia, a nawet łamania się zamków, co z kolei może powodować powstawanie szczelin i w konsekwencji niszczyć panele, również przez wnikanie brudu i wilgoci. Produkty z wysokim LCP (> 200-400 kPa, jak XPS czy maty kwarcowe) minimalizują to ryzyko. Cienkie pianki mają LCP rzędu 10-20 kPa – są katastrofą dla stabilności podłogi.
Przy wyborze podkładu, konieczne jest przeanalizowanie specyfiki pomieszczenia: czy potrzebujesz przede wszystkim ciepła (zimne podłoże)? Czy głównym problemem jest hałas (mieszkanie w bloku)? A może zależy ci na kompleksowym rozwiązaniu łączącym izolację termiczną pod panele z doskonałą izolacją akustyczną i maksymalną trwałością posadzki? Dla pomieszczeń na piętrze z ogrzewanym stropem, izolacja termiczna nie jest priorytetem, a liczy się głównie akustyka i stabilność. W takich przypadkach często wybiera się podkłady z wysokim LCP i ∆Lw, nawet jeśli ich lambda jest wyższa; maty kwarcowe i dedykowane podkłady PUR często okazują się najlepszym, choć nie najtańszym, rozwiązaniem. Dla parteru nad nieogrzewaną piwnicą, priorytetem jest termika (niska lambda) i wilgoć (brak wchłaniania i/lub zintegrowana bariera), co kieruje nas ku XPS lub matom kwarcowym ze zintegrowaną barierą, nawet kosztem minimalnie gorszej akustyki (choć XPS czy kwarc to i tak lepsza akustyka niż tanie pianki). Balansowanie pomiędzy tymi potrzebami to istota inteligentnego wyboru. Nie daj się złapać w pułapkę pozornych oszczędności; podkład to nie gadżet, a fundament twojej podłogi, od którego zależy jej trwałość i komfort użytkowania przez wiele lat. Jego koszt to zaledwie ułamek ceny paneli czy montażu (np. 10-80 PLN/m² podkładu vs. 40-150+ PLN/m² paneli + 30-60 PLN/m² montażu), a wpływ na komfort – bezcenny. Pamiętaj: podłoga to całość – panel i podkład muszą pracować razem w harmonii.
Aby lepiej zobrazować, jak różnią się parametry materiałów, przygotowaliśmy prosty wykres przedstawiający porównanie współczynnika przewodzenia ciepła (λ) i wskaźnika redukcji dźwięków uderzeniowych (∆Lw) dla wybranych typów podkładów. Zobaczcie sami, jak konkretne wartości przekładają się na wizualne rozłożenie materiałów na osi termicznej i akustycznej. Taki wykres pozwala szybko zorientować się, który materiał leży bliżej bieguna "ciepło" (niskie λ) a który bieguna "cisza" (wysokie ∆Lw).
Jak widać na wykresie, materiały koncentrują się w różnych obszarach – niektóre leżą nisko na osi lambda (dobra termika), inne wysoko na osi delta Lw (dobra akustyka). Maty kwarcowe i specjalistyczne produkty często starają się połączyć te cechy, znajdując się w korzystnym miejscu na obu osiach; proste pianki lądują w obszarze gorszych parametrów termo i akustycznych. Pamiętaj, że jest to uproszczone porównanie, a parametry mogą się różnić w zależności od konkretnego producenta i grubości materiału, jednak wykres doskonale ilustruje ogólne tendencje i pomaga zrozumieć, że wybór podkładu to świadome zarządzanie kompromisami.