Panele podłogowe na styrodurze (XPS): Czy kłaść bezpośrednio? Poradnik 2025
Marzenie o idealnie równej, ciepłej podłodze z paneli często towarzyszy wykończeniowym zmaganiom. W głowach wielu inwestorów pojawia się wówczas kusząca perspektywa: czy można uprościć proces i układać panele bezpośrednio na styrodurze (XPS), zyskując izolację i stabilną bazę w jednym kroku? To jedna z tych kwestii, gdzie inżynierska precyzja zderza się z budowlaną improwizacją, a odpowiedź eksperta brzmi zazwyczaj stanowczo: nie zaleca się kładzenia paneli bezpośrednio na styrodur bez warstw pośrednich.
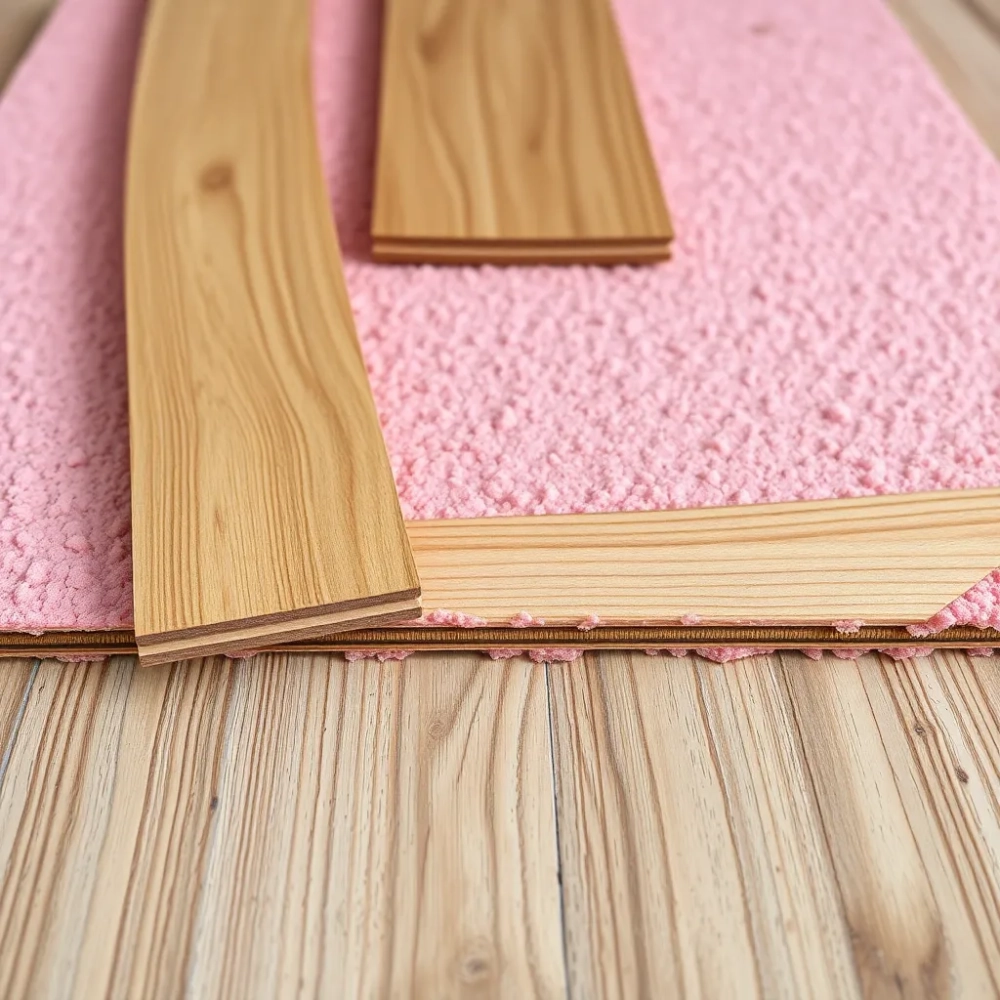
Choć styrodur XPS słynie ze swojej twardości i odporności, w kontekście posadzek z paneli laminowanych czy winylowych klik, jego powierzchnia nie jest wystarczająco przygotowana, by sprostać wyzwaniom codziennego użytkowania bez dodatkowego wsparcia. Ignorowanie tego etapu to trochę jak budowanie dachu bez więźby – konstrukcja pozornie stoi, ale czeka na pierwszą burzę. Systemy zatrzaskowe paneli wymagają idealnie równej i stabilnej podpory, która rozłoży nacisk i zaabsorbuje drobne drgania. Właśnie tutaj wkraczają na scenę kluczowe warstwy pośrednie.
Zanim zagłębimy się w zawiłości techniczne, przyjrzyjmy się kilku kluczowym parametrom materiałów izolacyjnych pod podłogi. Analiza typowych właściwości termicznych i mechanicznych pozwala zrozumieć, dlaczego dobór odpowiednich warstw ma znaczenie dla trwałości całej konstrukcji, nie tylko w przypadku zastosowania XPS, ale i w ogólnym planowaniu izolacji podłogi. Poniższe zestawienie pokazuje porównanie dwóch popularnych materiałów izolacyjnych pod posadzki:
Parametr | Standardowy styropian podłogowy (EPS 80-100) | Styrodur (XPS, typowe wartości dla podłóg) |
---|---|---|
Współczynnik przewodzenia ciepła (Lambda λ) [W/mK] | ~0.036 - 0.040 | ~0.028 - 0.034 |
Wytrzymałość na ściskanie przy 10% odkształceniu [kPa] | 80 - 100 | 300 - 700 (lub więcej dla specjalistycznych zastosowań) |
Nasiąkliwość wodą (% objętości) | Do 5% (czasem więcej) | Poniżej 1.5% |
Struktura komórek | Otwarto-komórkowa (spieniona) | Zamknięto-komórkowa (ekstrudowana) |
Jak widać w tabeli, styrodur (XPS) wyróżnia się przede wszystkim znacznie wyższą wytrzymałością na ściskanie oraz radykalnie niższą nasiąkliwością wodą w porównaniu do standardowego styropianu EPS przeznaczonego do podłóg. Choć Lambda ma również lepszy (niższy) współczynnik, to właśnie parametry mechaniczne i wilgotnościowe czynią go materiałem lepiej predysponowanym do bezpośredniego kontaktu z wilgocią podłogi i przenoszenia obciążeń użytkowych. Jednak nawet te doskonałe właściwości nie zwalniają z obowiązku stosowania warstw uzupełniających, o czym przekonamy się szczegółowo w dalszej części, skupiając się na każdym elemencie tej "podłogowej układanki".
Dlaczego warstwy pośrednie są kluczowe przy panelach na styrodurze
Postawmy sprawę jasno: ułożenie paneli laminowanych czy winylowych bezpośrednio na styrodurze, nawet tym najtwardszym, to igranie z losem. Choć XPS sam w sobie jest sztywny i odporny na odkształcenia pod dużym obciążeniem rozłożonym, jego powierzchnia rzadko kiedy bywa laboratoryjnie gładka i idealnie równa w skali mikro, która ma znaczenie dla delikatnych systemów zatrzaskowych paneli. Produkcja płyt XPS zakłada pewne tolerancje, a montaż na budowie nigdy nie gwarantuje perfekcji.
Systemy klik w panelach działają na zasadzie precyzyjnego połączenia pióra i wpustu. Aby to połączenie było trwałe i niewidoczne, oba elementy muszą idealnie do siebie pasować i mieć stabilne podparcie na całej długości. Nawet mikroskopijne nierówności na powierzchni styroduru mogą tworzyć lokalne punkty naprężeń. Wyobraźmy sobie, co dzieje się, gdy ciężki mebel lub choćby intensywny ruch pieszy skoncentruje nacisk na takim punkcie – system zatrzaskowy panela w tym miejscu może pęknąć lub się rozluźnić. Z czasem prowadzi to do powstawania szczelin i skrzypienia, które doprowadzą do szewskiej pasji nawet najbardziej stoickiego użytkownika.
Innym, często bagatelizowanym aspektem jest ochrona przed wilgocią. Mimo niskiej nasiąkliwości XPS, podłoga to miejsce narażone na kapilarny podciąg wilgoci z wylewki betonowej (nawet tej pozornie suchej) lub, w przypadku podłóg na gruncie, z ziemi. Panele, zwłaszcza laminowane, są na wilgoć bardzo wrażliwe – chłoną ją, puchną, wypaczają się. Styrodur sam w sobie nie stanowi wystarczającej bariery paroizolacyjnej, szczególnie w miejscach łączenia płyt.
Brak skutecznej bariery paroizolacyjnej między wylewką a XPS i dalej pod panelami to prosta droga do katastrofy. Wilgoć przejdzie przez złącza XPS (jeśli nie są idealnie uszczelnione), dotrze do spodu paneli, a tam, w szczelnej przestrzeni, skumuluje się. Efekt? Panele mogą się wybrzuszyć, ich krawędzie spuchnąć, a w najgorszym scenariuszu pojawi się pleśń. To nie tylko strata pieniędzy na materiały, ale też potencjalne zagrożenie dla zdrowia domowników. Widziałem nieraz podłogi z paneli, które wyglądały jakby przeszły przez powódź, tylko dlatego, że ktoś poskąpił na metrach kwadratowych folii.
Funkcja warstwy pośredniej, która ląduje bezpośrednio pod panelami, to także rozkładanie obciążeń punktowych na większą powierzchnię XPS. Chodzenie, przestawianie krzesła, upuszczenie czegoś cięższego – to wszystko generuje chwilowe, wysokie naciski na małym obszarze. Podkład elastycznie się dopasowuje i amortyzuje, transmitując na XPS łagodniejszy, bardziej rozłożony nacisk, co chroni jego powierzchnię przed punktowymi uszkodzeniami, a co za tym idzie, chroni panele.
Nie zapominajmy o komforcie akustycznym. Panele ułożone na twardej powierzchni, takiej jak styrodur, potrafią generować bardzo nieprzyjemny, głośny odgłos stukania przy każdym kroku (tzw. dźwięk uderzeniowy). Profesjonalny podkład pod panele ma za zadanie tłumić te dźwięki, sprawiając, że chodzenie po podłodze jest znacznie cichsze i przyjemniejsze, zarówno dla mieszkańców pomieszczenia, jak i osób poniżej.
Dodatkowo, warstwy pośrednie (szczególnie specjalne podkłady pod ogrzewanie podłogowe) odgrywają rolę w efektywnym rozprowadzaniu ciepła. Panele i XPS same w sobie nie są idealnymi przewodnikami cieplnymi, a podkład może pomóc równomiernie rozprowadzić ciepło z systemu grzewczego po całej powierzchni podłogi. W przypadku braku ogrzewania, odpowiedni podkład może stanowić dodatkową barierę termiczną, minimalizując ucieczkę ciepła do niższych, chłodniejszych warstw.
Pomijanie warstw pośrednich to oszczędność pozorna, która w krótkim czasie może zemścić się kosztownymi naprawami. Panel może wyglądać ładnie tuż po ułożeniu, ale bez odpowiedniego wsparcia strukturalnego i ochrony, jego żywotność zostanie drastycznie skrócona. To jak z dbaniem o kręgosłup – na co dzień nie myślimy o amortyzacji podczas chodzenia, dopóki nie zacznie boleć. Podłoga potrzebuje swojej „amortyzacji” i ochrony przed czynnikami, które powoli, ale systematycznie, niszczą jej strukturę.
Rynek budowlany jest pełen innowacji, ale niektóre zasady pozostają niezmienne. Układ warstw podłogowych pod panele jest efektem wieloletnich doświadczeń i testów. Każda warstwa ma swoje ściśle określone zadanie, a ich synergia zapewnia trwałość i komfort użytkowania. Próba pominięcia któregoś elementu jest jak usunięcie trybiku z dobrze naoliwionej maszyny – może zadziałać przez chwilę, ale awaria jest tylko kwestią czasu. Właśnie dlatego eksperci nie zalecają bezpośredniego montażu paneli na styrodurze.
Niezbędne warstwy izolacyjne i wyrównujące pod panele na XPS
Skoro wiemy już, dlaczego bezpośrednie ułożenie paneli na XPS to zły pomysł, pora przyjrzeć się, co dokładnie powinno znaleźć się między płytą styrodurową a panelami, aby podłoga służyła nam przez lata bez przykrych niespodzianek. Lista kluczowych elementów jest w zasadzie standardowa dla większości podłóg pływających układanych na izolacji termicznej lub akustycznej, z tą różnicą, że bazą jest w tym przypadku stabilny i twardy XPS.
Absolutną podstawą, kamieniem węgielnym poprawnego układu podłogi na styrodurze, jest folia paroizolacyjna. Zazwyczaj jest to folia polietylenowa (PE) o grubości minimum 0.2 mm (często spotykana jako 200 mikronów). Jej zadaniem jest całkowite zablokowanie migracji wilgoci z niższych warstw – wylewki betonowej czy nawet wilgoci szczątkowej, która może pojawić się w płycie XPS np. przez nieidealne uszczelnienie obwodowe. Wilgoć w posadzce to wróg numer jeden paneli laminowanych i winylowych.
Montaż folii paroizolacyjnej wymaga precyzji. Układa się ją na zakład co najmniej 20-30 cm, a wszelkie łączenia, a także styki folii ze ścianami, muszą być szczelnie sklejone specjalną taśmą do paroizolacji. Folia przy ścianach powinna zostać wywinięta na wysokość odpowiadającą planowanej wysokości posadzki wraz z panelami i podkładem, a jej nadmiar zostanie odcięty po zamontowaniu listew przypodłogowych. Każda nieszczelność, nawet niewielka, może w przyszłości skutkować problemami.
Nad folią paroizolacyjną, a pod samymi panelami, ląduje podkład pod panele. Jego główną funkcją jest nie tylko ochrona paneli i tłumienie dźwięków uderzeniowych, ale też wyrównanie drobnych nierówności. Mimo że XPS jest twardy, jego powierzchnia może mieć niewielkie, rzędu ułamków milimetra do 1-2 mm, lokalne odchyłki. Podkład elastycznie się do nich dopasowuje, zapewniając idealnie płaską powierzchnię dla systemu zatrzaskowego paneli. To krytyczne dla trwałości połączeń.
Na rynku dostępne są różne rodzaje podkładów, każdy o nieco innych właściwościach i przeznaczeniu. Najprostsze i najtańsze to pianki polietylenowe (PE) o grubości 2-6 mm. Oferują minimalną izolację akustyczną i termiczną, ale stanowią podstawową ochronę mechaniczną i barierę dla drobnych nierówności. Ich gęstość jest zazwyczaj niska, około 20-30 kg/m³, co sprawia, że są podatne na trwałe odkształcenia pod długotrwałym, ciężkim naciskiem.
Bardziej zaawansowane są podkłady z filcu, korka lub płyty drewnopochodnej (np. z włókna drzewnego). Płyty drewnopochodne są zazwyczaj grubsze (5-7 mm, a nawet 10 mm) i bardzo dobrze wyrównują lokalne zagłębienia na powierzchni styroduru (do 4-5 mm), a także oferują niezłą izolację akustyczną i termiczną. Ich gęstość jest znacznie wyższa, często przekraczając 200 kg/m³. Podkłady korkowe czy filcowe są droższe, ale cenione za naturalne właściwości izolacyjne i akustyczne.
Istnieją także podkłady kompozytowe, często łączące materiały mineralne lub poliuretanowe z warstwą folii (paroizolacyjnej lub paroprzepuszczalnej, w zależności od konfiguracji) lub innymi włóknami. Podkłady te charakteryzują się wysoką gęstością (powyżej 100 kg/m² w przeliczeniu na jednostkę powierzchni, a nie objętości jak przy płytach) i dobrą odpornością na ściskanie, jednocześnie skutecznie tłumiąc dźwięki. Przy wyborze podkładu należy zwrócić uwagę na jego parametr gęstości (im wyższa, tym podkład lepiej znosi obciążenia) oraz na wartość współczynnika tłumienia dźwięków uderzeniowych (im wyższa wartość w dB, tym ciszej będzie w pomieszczeniu poniżej).
Ważnym parametrem, zwłaszcza w przypadku ogrzewania podłogowego, jest opór cieplny (współczynnik R). Zarówno XPS, jak i podkład pod panele, stawiają opór przepływowi ciepła. Podkład pod panele na ogrzewanie podłogowe powinien mieć możliwie niski opór cieplny (zazwyczaj poniżej 0.05 m²K/W dla całego systemu panel+podkład), aby ciepło mogło efektywnie przenikać do pomieszczenia. Płyty XPS pod ogrzewanie podłogowe również mają specyficzne, zazwyczaj nieco wyższe, współczynniki lambda, ale wciąż lepsze niż standardowe EPS.
W praktyce najczęściej stosowany układ na styrodurze XPS to: płyta XPS jako izolacja bazowa, następnie folia paroizolacyjna 0.2 mm, a na to odpowiedni podkład pod panele dobrany w zależności od potrzeb (akustyka, wyrównanie, ogrzewanie podłogowe). Koszt tych dodatkowych warstw to zazwyczaj ułamek ceny paneli, a gwarantują one trwałość i bezproblemowe użytkowanie przez wiele lat. Pomijanie ich to oszczędzanie, które może zamienić wymarzoną podłogę w źródło frustracji.
Porównanie wybranych parametrów materiałów podłogowych
Powyższy wykres ilustruje, dlaczego XPS stanowi doskonałą bazę podłogową pod kątem nośności, znacznie przewyższając typowe podkłady. Właśnie ta różnica w parametrach wymusza zastosowanie warstwy buforującej, która jest w stanie skompensować niewielkie nierówności i dostosować się do dynamicznych obciążeń od ruchu pieszego, chroniąc jednocześnie delikatne połączenia paneli.
Zalety stosowania styroduru (XPS) jako izolacji podłogowej pod panele
Choć kładzenie paneli bezpośrednio na styrodurze jest tematem, który wymaga niuansowania i wskazania na konieczność warstw pośrednich, sam wybór styroduru (XPS) jako bazowej izolacji podłogowej pod panele jest w wielu sytuacjach decyzją przemyślaną i wysoce uzasadnioną. Inwestorzy wykańczający dom muszą zmierzyć się z wieloma decyzjami, które w późniejszym czasie skutkują komfortowym lub nie użytkowaniem pomieszczeń. Jedną z takich decyzji jest dobór materiału izolacyjnego pod podłogę.
Rynek oferuje szeroki wachlarz produktów, ale materiał, który ma sprawić, że podłoga będzie nie tylko wyglądała nieskazitelnie, ale również skutecznie izolowała termicznie i była trwała, wymaga świadomego wyboru. Często pierwsza myśl biegnie w kierunku klasycznego styropianu, który doskonale sprawdza się podczas izolacji fasady czy fundamentów. Jednak, jak już sygnalizowaliśmy wcześniej, ten materiał niekoniecznie będzie optymalnym wyborem, jeśli chodzi o obciążone i potencjalnie wilgotne warstwy podłogi.
Tutaj właśnie ujawniają się kluczowe zalety styroduru (XPS), który jest materiałem specjalnie przeznaczonym do trudniejszych zastosowań, w tym do izolacji posadzek. Czym wyróżnia się polistyren ekstrudowany (XPS) na tle tradycyjnego styropianu (EPS) i dlaczego jest wart swojej, często nieco wyższej, ceny? Odpowiedź tkwi w jego specyficznych właściwościach fizycznych i mechanicznych, wynikających z odmiennej technologii produkcji.
Jedną z najważniejszych cech styroduru jest jego znacznie większa wytrzymałość na ściskanie w porównaniu do standardowych odmian styropianu podłogowego. Podczas gdy typowy EPS 80-100 osiąga wytrzymałość rzędu 80-100 kPa przy 10% odkształceniu, płyty XPS dedykowane podłogom mają ten parametr na poziomie od 300 do nawet 700 kPa. Ta twardość gwarantuje, że izolacja nie ulegnie trwałemu odkształceniu pod ciężarem mebli, sprzętów AGD czy intensywnym ruchem pieszym. Jest to fundamentalne dla zachowania płaskości i stabilności podłogi na panele przez cały okres jej użytkowania.
Kolejnym, nie mniej istotnym parametrem, jest wyjątkowo niska nasiąkliwość wodą styroduru, sięgająca maksymalnie 1.5% objętości (zgodnie z danymi podsumowania). Dzięki zamkniętej, szczelnej strukturze komórek, XPS nie wchłania wody z otoczenia w takim stopniu jak otwartokomórkowy styropian. Jest to krytyczna zaleta w warstwach podłogi, które mogą być narażone na kontakt z wilgocią – czy to w wyniku potencjalnych drobnych wycieków, podciągania kapilarnego z gruntu na parterze, czy nawet wysokiej wilgotności w pomieszczeniach takich jak łazienka (jeśli styrodur jest stosowany w sąsiadujących obszarach). Izolacja, która nasiąka wilgocią, traci swoje właściwości termoizolacyjne, a także staje się pożywką dla rozwoju pleśni i grzybów.
XPS charakteryzuje się także lepszym (niższym) współczynnikiem przewodzenia ciepła (Lambda λ), typowo w zakresie od 0.028 do 0.034 W/mK, podczas gdy dla standardowego EPS podłogowego wartości te wahają się od 0.036 do 0.040 W/mK i więcej. Niższa Lambda oznacza, że przy tej samej grubości warstwa XPS zapewnia lepszą izolację termiczną, skuteczniej ograniczając straty ciepła do podłoża lub przez strop do niższej, nieogrzewanej kondygnacji. Pozwala to na efektywniejsze wykorzystanie energii cieplnej do ogrzewania pomieszczeń, co przekłada się na niższe rachunki za ogrzewanie. W przypadku stosowania ogrzewania podłogowego, skuteczna izolacja pod systemem grzewczym (tu: XPS) jest wręcz niezbędna, aby ciepło było kierowane w górę, do pomieszczenia, a nie marnowane na ogrzewanie warstw konstrukcyjnych podłogi.
Dodatkową zaletą styroduru jest jego dobra stabilność wymiarowa. Materiał ten w mniejszym stopniu reaguje na zmiany temperatury i wilgotności skurczem czy pęcznieniem w porównaniu do niektórych innych materiałów izolacyjnych. Ta stabilność jest ważna dla zapewnienia niezmiennej, płaskiej powierzchni pod panele przez długi czas, minimalizując ryzyko powstawania naprężeń w całej konstrukcji podłogi. Panele, jako podłoga pływająca, potrzebują solidnej i stabilnej bazy.
Podsumowując, choć ułożenie paneli bezpośrednio na XPS jest błędem konstrukcyjnym wymagającym korekty poprzez zastosowanie odpowiednich warstw pośrednich, sam XPS jest doskonałym materiałem izolacyjnym pod podłogę na panele. Jego kluczowe zalety – wyższa wytrzymałość na ściskanie, niska nasiąkliwość i korzystny współczynnik przewodzenia ciepła – czynią go idealnym wyborem wszędzie tam, gdzie podłoga jest narażona na obciążenia i potencjalną wilgoć, szczególnie na parterze budynku czy w piwnicy. To inwestycja, która przekłada się na trwałość, stabilność i efektywność energetyczną całego systemu podłogowego.