Jak zaizolować podłogę drewnianą w 2025 roku?
Czy kiedykolwiek stąpając bosą stopą po podłodze w chłodny poranek poczułeś dreszcz przechodzący przez całe ciało? Brr, samo wspomnienie przyprawia o gęsią skórkę! Ale nie martw się, mamy na to rozwiązanie. W tym artykule zgłębimy tajniki izolacji drewnianej podłogi, która jest kluczem do ciepłego i przytulnego domu. Krótko mówiąc, izolacja drewnianej podłogi polega na zastosowaniu odpowiednich materiałów i metod, aby zapobiec ucieczce ciepła przez podłogę, zapewniając komfort termiczny i oszczędności energii.
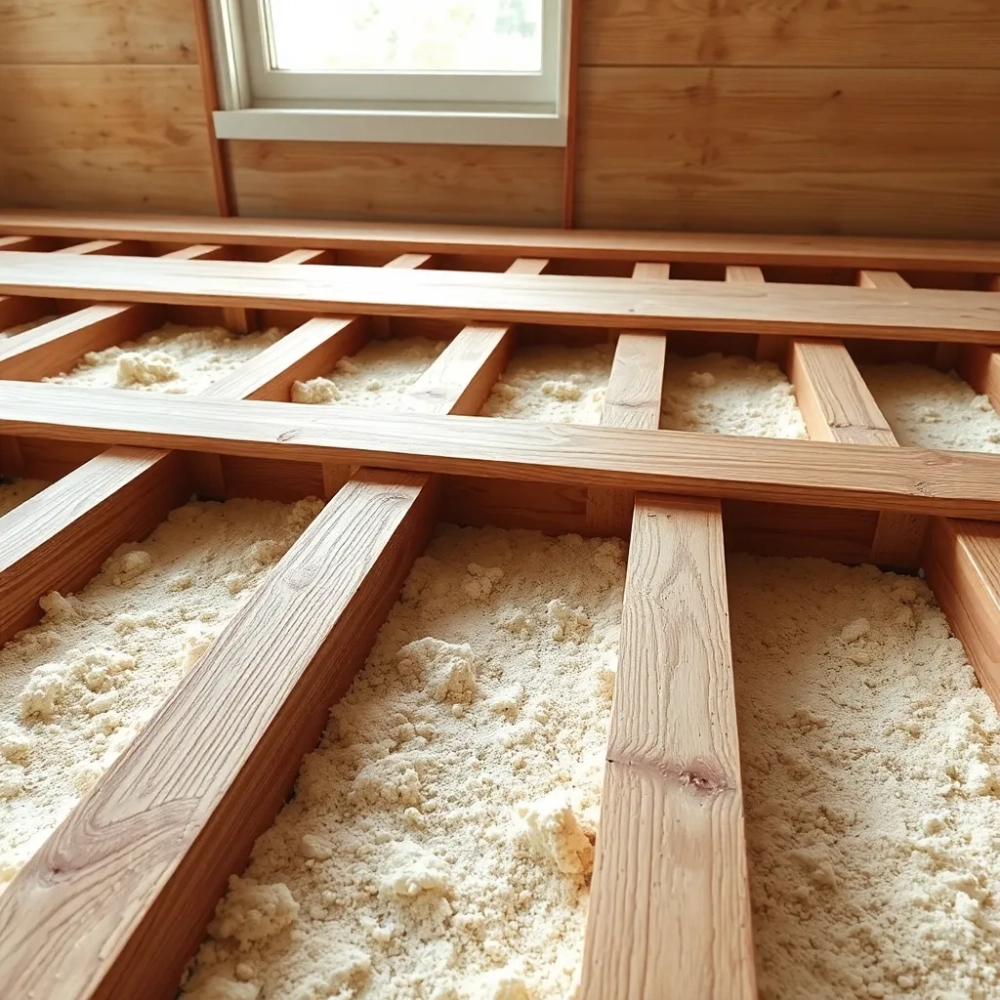
Porównanie metod izolacji drewnianej podłogi – Kluczowe parametry
Decyzja o izolacji drewnianej podłogi to krok w dobrą stronę, ale szybko pojawia się kolejne pytanie: Jak to zrobić najlepiej? Wybór metody i materiałów to klucz do sukcesu. Przyjrzyjmy się bliżej kilku popularnym rozwiązaniom.
Metoda Izolacji | Materiał Izolacyjny | Orientacyjna Cena Materiału za m² (PLN) | Współczynnik Przewodzenia Ciepła λ (W/mK) | Grubość Izolacji (mm) | Orientacyjny Czas Montażu na 10m² (godziny) | Trudność Montażu (1-łatwy, 5-trudny) | Zalecane Zastosowanie |
---|---|---|---|---|---|---|---|
Między legarami | Wełna mineralna | 20-40 | 0.035-0.045 | 100-200 | 4-8 | 2 | Podłogi na legarach, podłogi parterowe, stropy |
Między legarami | Pianka PUR | 50-80 | 0.022-0.025 | 80-150 | 6-10 | 3 | Podłogi na legarach, przestrzenie trudno dostępne |
Pod wylewkę | Płyty XPS | 40-60 | 0.030-0.035 | 50-100 | 3-6 | 2 | Podłogi z ogrzewaniem podłogowym, podłogi na gruncie |
Pod wylewkę | Styropian EPS | 15-30 | 0.038-0.042 | 50-150 | 3-6 | 1 | Podłogi na gruncie, gdzie obciążenia nie są duże |
Maty izolacyjne cienkowarstwowe | Poliuretan, folia aluminiowa | 60-120 | 0.020-0.030 (efektywna) | 5-10 | 2-4 | 1 | Renowacje, niskie przestrzenie, pod panele laminowane |
Legenda: Ceny i parametry są orientacyjne i mogą się różnić w zależności od producenta, regionu i aktualnych promocji. Czas montażu jest szacunkowy i zależy od umiejętności wykonawcy oraz specyfiki projektu. Współczynnik przewodzenia ciepła (λ) – im niższa wartość, tym lepsza izolacyjność materiału.
Ta tabela daje nam solidne podstawy do porównania różnych opcji. Widzimy, że wełna mineralna jest ekonomiczna i łatwa w montażu, ale pianka PUR oferuje lepszą izolacyjność. Płyty XPS i styropian EPS świetnie sprawdzą się pod wylewkę, a maty cienkowarstwowe są idealne do renowacji.
Przygotowanie podłogi drewnianej do izolacji: Kluczowe etapy
Zanim z impetem rzucimy się na wybór materiałów i metody izolacji, zatrzymajmy się na chwilę i przygotujmy grunt pod nasze działania – dosłownie i w przenośni. Przygotowanie podłogi drewnianej do izolacji to fundament, na którym zbudujemy sukces naszego przedsięwzięcia. Pominięcie tego etapu to jak budowa domu bez solidnych fundamentów – prędzej czy później pojawią się problemy. Jak mawiał stary cieśla, "Dobre przygotowanie to połowa roboty!". A w naszym przypadku to nawet więcej niż połowa – to gwarancja trwałości, efektywności i naszego spokoju ducha.
Ocena stanu podłogi – Detektyw w akcji
Pierwszym krokiem w naszej detektywistycznej misji jest dokładna ocena stanu istniejącej podłogi. Nie chodzi tylko o rzut oka – musimy wcielić się w rolę wnikliwego inspektora. Zaczynamy od wizualnego przeglądu – szukamy śladów wilgoci, pleśni, grzybów, uszkodzeń mechanicznych, pęknięć, szczelin czy oznak żerowania szkodników drewna. Te niepozorne znaki mogą świadczyć o poważniejszych problemach, które trzeba rozwiązać zanim przystąpimy do izolacji. Wyobraźmy sobie sytuację: Janek, nasz znajomy, postanowił zaizolować podłogę w starym domu. Z entuzjazmem zakupił materiały, ale zapomniał o inspekcji. Po kilku miesiącach od izolacji, w rogu pokoju pojawił się nieprzyjemny zapach stęchlizny. Okazało się, że pod podłogą, w miejscu niedostrzeżonej wcześniej przeciekającej rury, rozwijała się pleśń. Janek musiał demontować część podłogi, usuwać pleśń i dopiero wtedy mógł cieszyć się efektami izolacji. Lekcja? Prewencja jest tańsza i mniej pracochłonna niż naprawa!
Czyszczenie i naprawa – Warsztat majsterkowicza
Po detektywistycznej misji przechodzimy do etapu warsztatowego – czyszczenia i naprawy. Podłoga przed izolacją musi być czysta, sucha i stabilna. Usuwamy wszelkie zanieczyszczenia – kurz, piasek, resztki starej farby czy lakieru. Możemy użyć odkurzacza przemysłowego, szczotki, szpachelki. Jeśli zauważymy drobne ubytki, pęknięcia czy szczeliny, wypełniamy je odpowiednią masą szpachlową do drewna lub uszczelniaczem. W przypadku większych uszkodzeń, jak spróchniałe deski czy poluzowane legary, konieczna będzie ich wymiana lub wzmocnienie. Pamiętajmy, że izolacja ma być inwestycją na lata, więc warto zadbać o solidne podstawy. Wyobraźmy sobie, że izolujemy podłogę, a pod spodem pozostawiamy wilgotne trociny czy kurz. Z czasem, pod wpływem ciepła i wilgoci, zacznie to gnić i wydzielać nieprzyjemne zapachy. Nasza wymarzona, ciepła podłoga zamieni się w siedlisko bakterii i grzybów. Dlatego gruntowne czyszczenie to nie tylko kwestia estetyki, ale przede wszystkim higieny i trwałości izolacji.
Wyrównanie podłoża – Perfekcja pod każdym względem
Kolejnym krokiem, często pomijanym, a niezwykle istotnym, jest wyrównanie podłoża. Nawet jeśli podłoga na pierwszy rzut oka wydaje się równa, warto sprawdzić to poziomicą. Nierówności mogą utrudnić montaż izolacji, a w przyszłości powodować skrzypienie podłogi czy pękanie paneli. Drobne nierówności możemy zniwelować szpachlą lub masą samopoziomującą. W przypadku większych różnic poziomów, konieczne może być szlifowanie desek, struganie legarów, a nawet wykonanie dodatkowej warstwy wyrównującej z płyt OSB lub sklejki. Pamiętajmy, że idealnie równa powierzchnia to nie tylko estetyka, ale też lepsze przyleganie izolacji, brak mostków termicznych i równomierne rozłożenie obciążenia. Wyobraźmy sobie, że układamy izolację na nierównej podłodze. W miejscach zagłębień materiał izolacyjny będzie ściśnięty, a w miejscach wypukłości – luźny. To prowadzi do nierównomiernej izolacji, powstawania mostków termicznych i spadku efektywności całego systemu. Dlatego wyrównanie podłoża to nie luksus, a konieczność, jeśli chcemy cieszyć się ciepłą i cichą podłogą przez długie lata.
Wentylacja przestrzeni podpodłogowej – Oddychająca podłoga
Ostatnim, ale nie mniej ważnym etapem przygotowania, jest zapewnienie odpowiedniej wentylacji przestrzeni podpodłogowej. Szczególnie w starych domach z podłogami na legarach, wentylacja jest kluczowa dla uniknięcia problemów z wilgocią i grzybami. Sprawdźmy, czy w przestrzeni podpodłogowej są otwory wentylacyjne, tzw. "ślepe wywietrzniki". Jeśli ich nie ma lub są zatkane, należy je udrożnić lub wykonać nowe. Możemy również zastosować specjalne kratki wentylacyjne w listwach przypodłogowych. Pamiętajmy, że drewno jest materiałem "oddychającym" i potrzebuje cyrkulacji powietrza, aby zachować swoje właściwości i uniknąć degradacji. Izolacja, choć korzystna, może jednocześnie utrudnić naturalną wentylację, dlatego musimy zadbać o to, aby przestrzeń podpodłogowa była odpowiednio wentylowana. Wyobraźmy sobie sytuację, że szczelnie izolujemy podłogę, zamykając jednocześnie dostęp powietrza do przestrzeni podpodłogowej. Wilgoć, która naturalnie gromadzi się pod podłogą, nie będzie miała jak odparować. To idealne warunki dla rozwoju pleśni i grzybów, które mogą zniszczyć drewno i negatywnie wpłynąć na nasze zdrowie. Dlatego wentylacja to nie tylko element przygotowania, ale również element profilaktyki, który uchroni nas przed poważnymi problemami w przyszłości.
Materiały izolacyjne do drewnianej podłogi - Przegląd i wybór najlepszych opcji w 2025 roku
Świat materiałów izolacyjnych to prawdziwa dżungla możliwości. Stojąc przed wyborem, można poczuć się zagubionym jak turysta bez mapy w amazońskiej puszczy. Ale bez obaw! W tym rozdziale przemienimy się w doświadczonych przewodników i przeprowadzimy Cię przez gąszcz opcji, abyś w 2025 roku mógł wybrać materiał izolacyjny idealnie dopasowany do Twojej drewnianej podłogi. Nie będziemy owijać w wełnę mineralną – przejdziemy od razu do konkretów, analizując najpopularniejsze i najnowocześniejsze rozwiązania. Bo w końcu, jak mawiają fachowcy, "Dobrze dobrany materiał to połowa sukcesu izolacji". A my chcemy osiągnąć pełny sukces, prawda?
Wełna mineralna – Klasyka gatunku, nowa odsłona
Zacznijmy od klasyka, czyli wełny mineralnej. To materiał znany i ceniony od lat, ale wciąż ewoluujący i zaskakujący nowymi właściwościami. Wełna mineralna, zarówno szklana jak i skalna, to popularny wybór ze względu na swoją dostępność, stosunkowo niską cenę i dobre właściwości termoizolacyjne oraz akustyczne. Współczynnik przewodzenia ciepła λ dla wełny mineralnej waha się zazwyczaj w granicach 0.035-0.045 W/mK, co czyni ją konkurencyjną w porównaniu do innych materiałów. Na rynku w 2025 roku znajdziemy wełnę mineralną w różnych formach – mat, płyt, granulatu, co pozwala na dopasowanie do różnych metod izolacji i specyfiki podłogi drewnianej. Ceny wełny mineralnej zaczynają się od około 20 PLN za m² dla standardowych mat o grubości 10 cm. Ale uwaga! Na rynku pojawiają się coraz częściej "inteligentne" wełny mineralne, np. z dodatkiem grafitu lub nanotechnologii, które oferują jeszcze lepsze parametry izolacyjne przy mniejszej grubości. Takie innowacje mogą kosztować nieco więcej, ale w dłuższej perspektywie przekładają się na większe oszczędności energii i komfort. Pamiętajmy też o ekologicznym aspekcie – coraz popularniejsza staje się wełna mineralna z recyklingu, która łączy w sobie dobre właściwości izolacyjne z troską o środowisko. Wybierając wełnę mineralną w 2025 roku, warto zwrócić uwagę nie tylko na cenę, ale także na parametry techniczne, formę, ekologię i innowacje. Bo klasyka, choć cenna, wciąż ma potencjał do rozwoju.
Pianki PUR i PIR – Lekkie, ciepłe i szczelne
Jeśli szukamy materiału o wyjątkowo dobrych właściwościach termoizolacyjnych i niskiej grubości, warto zwrócić uwagę na pianki poliuretanowe (PUR) i poliizocyjanuranowe (PIR). Pianki PUR i PIR to prawdziwi mistrzowie izolacji termicznej. Współczynnik przewodzenia ciepła λ dla pianek PUR i PIR może sięgać nawet 0.022-0.025 W/mK, co oznacza, że są jednymi z najcieplejszych materiałów izolacyjnych dostępnych na rynku. Ich lekkość i łatwość montażu to kolejne atuty. Pianki PUR i PIR występują w różnych formach – płyt, natrysków, co pozwala na ich zastosowanie w różnych konfiguracjach podłóg drewnianych. Płyty PIR są zazwyczaj droższe od PUR, ale oferują lepszą odporność ogniową. Ceny płyt PUR zaczynają się od około 50 PLN za m² dla grubości 8 cm, a PIR – od 70 PLN za m². W 2025 roku możemy spodziewać się dalszego rozwoju technologii pianek PUR i PIR, szczególnie w kierunku ekologii i bezpieczeństwa. Producenci coraz częściej oferują pianki o obniżonej emisji lotnych związków organicznych (LZO) i uniepalnione w sposób bezpieczniejszy dla środowiska. Coraz popularniejsze stają się też pianki PUR i PIR z dodatkami naturalnych włókien, np. lnu czy konopi, które łączą w sobie dobre właściwości izolacyjne z ekologicznym charakterem. Wybierając pianki PUR lub PIR, warto zwrócić uwagę na ich rodzaj, grubość, parametry techniczne, certyfikaty bezpieczeństwa i ekologię. Bo ciepło i komfort mogą iść w parze z odpowiedzialnością za środowisko.
Styropian EPS i XPS – Ekonomiczny i wszechstronny
Kolejna kategoria materiałów izolacyjnych, zasługująca na uwagę, to styropian EPS (ekspandowany) i XPS (ekstrudowany). Styropian EPS i XPS to materiały znane i stosowane w izolacji od lat, charakteryzujące się dobrym stosunkiem ceny do jakości i wszechstronnością zastosowań. Styropian EPS jest tańszy, ale mniej odporny na wilgoć i uszkodzenia mechaniczne niż XPS. Współczynnik przewodzenia ciepła λ dla styropianu EPS waha się w granicach 0.038-0.042 W/mK, a dla XPS – 0.030-0.035 W/mK. Styropian EPS i XPS występują w formie płyt o różnych grubościach i gęstościach, co pozwala na dopasowanie do różnych potrzeb izolacyjnych. Ceny styropianu EPS zaczynają się od około 15 PLN za m² dla grubości 5 cm, a XPS – od 40 PLN za m². W 2025 roku na rynku dostępne będą coraz nowocześniejsze odmiany styropianu EPS i XPS, np. styropian grafitowy, który oferuje lepsze parametry izolacyjne dzięki dodatkowi grafitu. Styropian XPS z dodatkami, np. włókien celulozowych, może być bardziej ekologiczny i odporny na wilgoć. Producenci styropianu coraz częściej stawiają na recykling i zrównoważony rozwój, oferując produkty wykonane z recyklatu lub nadające się do ponownego przetworzenia. Wybierając styropian EPS lub XPS, warto rozważyć ich rodzaj, gęstość, grubość, właściwości techniczne i ekologiczne. Bo ekonomia i wszechstronność mogą iść w parze z innowacją i odpowiedzialnością.
Izolacje naturalne – Powrót do korzeni, z nową technologią
Dla osób ceniących naturalne materiały i ekologiczne rozwiązania, idealnym wyborem mogą być izolacje naturalne, takie jak wełna drzewna, celuloza, len, konopie czy korek. Izolacje naturalne to materiały coraz popularniejsze, charakteryzujące się nie tylko dobrymi właściwościami termoizolacyjnymi, ale także zdolnością do regulacji wilgoci, zdrowym mikroklimatem wnętrz i ekologicznym charakterem. Wełna drzewna, produkowana z włókien drzewnych, oferuje współczynnik przewodzenia ciepła λ na poziomie 0.036-0.040 W/mK. Celuloza, pochodząca z recyklingu makulatury, ma λ około 0.038-0.042 W/mK. Len i konopie, włókna roślinne, charakteryzują się λ w granicach 0.035-0.040 W/mK. Korek, naturalny materiał z kory dębu korkowego, ma λ około 0.037-0.040 W/mK. Izolacje naturalne występują w różnych formach – mat, płyt, granulatu, co pozwala na ich zastosowanie w różnych metodach izolacji podłóg drewnianych. Ceny izolacji naturalnych są zazwyczaj wyższe niż wełny mineralnej czy styropianu, ale warto wziąć pod uwagę ich długoterminowe korzyści zdrowotne, ekologiczne i komfortowe. W 2025 roku możemy spodziewać się dalszego rozwoju technologii izolacji naturalnych, szczególnie w kierunku zwiększenia ich dostępności, obniżenia cen i poprawy parametrów technicznych. Coraz popularniejsze stają się mieszanki izolacji naturalnych, np. wełny drzewnej z celulozą, które łączą w sobie zalety różnych materiałów. Wybierając izolacje naturalne, warto zwrócić uwagę na ich rodzaj, parametry techniczne, certyfikaty ekologiczne i pochodzenie surowców. Bo naturalne rozwiązania mogą być nie tylko ciepłe, ale i zdrowe, ekologiczne i stylowe.
Maty izolacyjne cienkowarstwowe – Cienkie, ale skuteczne
Na koniec, przyjrzyjmy się matom izolacyjnym cienkowarstwowym. To stosunkowo nowa kategoria materiałów, idealna do renowacji i miejsc o ograniczonej wysokości. Maty izolacyjne cienkowarstwowe to produkty zaawansowane technologicznie, charakteryzujące się bardzo niską grubością przy zachowaniu dobrych właściwości termoizolacyjnych. Często wykonane są z poliuretanu lub polietylenu z dodatkiem folii aluminiowej, która odbija ciepło i zwiększa efektywność izolacji. "Efektywny" współczynnik przewodzenia ciepła λ dla mat cienkowarstwowych może być porównywalny z tradycyjnymi izolacjami, pomimo znacznie mniejszej grubości – nawet 0.020-0.030 W/mK. Grubość mat cienkowarstwowych waha się zazwyczaj od 5 do 10 mm. Są łatwe w montażu, często samoprzylepne lub układane na zakładkę. Ceny mat cienkowarstwowych zaczynają się od około 60 PLN za m² dla grubości 5 mm. W 2025 roku możemy spodziewać się dalszego rozwoju mat cienkowarstwowych, szczególnie w kierunku zwiększenia ich efektywności, obniżenia ceny i rozszerzenia zastosowań. Coraz popularniejsze stają się maty cienkowarstwowe z dodatkami, np. materiałów termoakumulacyjnych, które poprawiają komfort cieplny w pomieszczeniu. Wybierając maty cienkowarstwowe, warto zwrócić uwagę na ich grubość, "efektywny" współczynnik przewodzenia ciepła, sposób montażu i dodatkowe właściwości. Bo cienka izolacja może być zaskakująco skuteczna, szczególnie tam, gdzie liczy się każdy centymetr.
Różne metody izolacji drewnianej podłogi - Którą wybrać i dlaczego?
Mając już wiedzę o materiałach izolacyjnych, pora przejść do kluczowego pytania: jaką metodę izolacji drewnianej podłogi wybrać? Odpowiedź nie jest jednoznaczna i zależy od wielu czynników – rodzaju podłogi, budżetu, oczekiwanego efektu, a nawet własnych umiejętności majsterkowicza. W tym rozdziale porównamy różne metody izolacji, analizując ich zalety, wady, koszty i stopień trudności, abyś mógł podjąć świadomą decyzję i wybrać rozwiązanie optymalne dla siebie. Nie będziemy budować zamków na piasku – skupimy się na praktycznych aspektach i realnych możliwościach. Bo w końcu, jak mawiają doświadczeni fachowcy, "Dobra metoda izolacji to taka, która pasuje do Twojej podłogi i Twoich potrzeb". A my pomożemy Ci znaleźć tę idealną parę.
Izolacja między legarami – Klasyka dla podłóg na legarach
Zacznijmy od metody klasycznej, czyli izolacji między legarami. To rozwiązanie idealne dla podłóg drewnianych na legarach, gdzie przestrzeń między legarami naturalnie tworzy "kieszenie" na materiał izolacyjny. Metoda ta polega na wypełnieniu przestrzeni między legarami materiałem izolacyjnym – najczęściej wełną mineralną, pianką PUR lub izolacją naturalną. Zaletą izolacji między legarami jest stosunkowo łatwy montaż, szczególnie przy użyciu wełny mineralnej, która jest elastyczna i łatwo dopasowuje się do kształtu przestrzeni. Koszt materiałów jest zazwyczaj umiarkowany, a efekt izolacyjny – bardzo dobry. Wadą może być konieczność demontażu podłogi, jeśli nie mamy dostępu do przestrzeni między legarami od spodu. Stopień trudności montażu oceniamy na 2-3 (w skali 1-5, gdzie 1 to łatwy, 5 to trudny). Czas montażu na 10m² to około 4-8 godzin, w zależności od rodzaju materiału i dostępu do przestrzeni między legarami. Orientacyjny koszt materiałów na 10m² to 200-400 PLN dla wełny mineralnej, 500-800 PLN dla pianki PUR, i 400-700 PLN dla izolacji naturalnej (ceny orientacyjne). Metodę izolacji między legarami polecamy szczególnie do podłóg na legarach w domach jednorodzinnych, starych kamienicach, budynkach z poddaszem nieużytkowym lub piwnicą, gdzie dostęp do przestrzeni podpodłogowej jest możliwy. Jest to rozwiązanie sprawdzone, efektywne i ekonomiczne, szczególnie w połączeniu z wełną mineralną lub izolacją naturalną.
Izolacja pod podłogą – Dla podłóg na gruncie i wylewek
Kolejna popularna metoda to izolacja pod podłogą, stosowana najczęściej w przypadku podłóg na gruncie lub pod wylewkę betonową. Polega na ułożeniu warstwy izolacji na warstwie betonu lub gruntu, a następnie wykonaniu wylewki lub ułożeniu podłogi drewnianej. Najczęściej stosowane materiały to płyty styropianowe EPS lub XPS, płyty PIR lub PUR, a także maty izolacyjne cienkowarstwowe. Zaletą izolacji pod podłogą jest wysoka efektywność termoizolacyjna, szczególnie w przypadku płyt XPS lub PIR, które charakteryzują się niskim współczynnikiem przewodzenia ciepła i odpornością na wilgoć. Metoda ta jest szczególnie polecana w przypadku podłóg z ogrzewaniem podłogowym, gdyż izolacja zapobiega ucieczce ciepła w dół. Wadą może być konieczność podniesienia poziomu podłogi, co może wpływać na wysokość pomieszczenia i konieczność dostosowania drzwi. Stopień trudności montażu oceniamy na 2-3 (w skali 1-5). Czas montażu na 10m² to około 3-6 godzin, w zależności od rodzaju materiału i podłoża. Orientacyjny koszt materiałów na 10m² to 150-300 PLN dla styropianu EPS, 400-600 PLN dla płyt XPS, i 600-1200 PLN dla płyt PIR (ceny orientacyjne). Metodę izolacji pod podłogą polecamy szczególnie do nowych domów, domów energooszczędnych, budynków z ogrzewaniem podłogowym, oraz wszędzie tam, gdzie planujemy wylewkę betonową lub nową podłogę na gruncie. Jest to rozwiązanie skuteczne, trwałe i pozwalające na osiągnięcie wysokiego komfortu cieplnego.
Izolacja na podłodze – Szybka renowacja i cienkie warstwy
Jeśli szukasz szybkiego i prostego sposobu na izolację drewnianej podłogi, bez konieczności demontażu istniejącej podłogi i dużych prac remontowych, warto rozważyć izolację na podłodze. Ta metoda polega na ułożeniu warstwy izolacji bezpośrednio na istniejącej podłodze drewnianej, a następnie przykryciu jej nową warstwą wykończeniową – np. panelami laminowanymi, deskami podłogowymi lub wykładziną. Najczęściej stosowane materiały to maty izolacyjne cienkowarstwowe, płyty korkowe lub cienkie płyty XPS. Zaletą izolacji na podłodze jest szybkość i łatwość montażu, minimalna ingerencja w istniejącą strukturę podłogi i stosunkowo niski koszt. Metoda ta jest idealna do renowacji starych podłóg, gdzie zależy nam na szybkim poprawieniu komfortu cieplnego bez dużych nakładów pracy i finansów. Wadą może być podniesienie poziomu podłogi o kilka milimetrów lub centymetrów, w zależności od grubości materiału izolacyjnego, co może wpływać na wysokość pomieszczenia i konieczność dostosowania drzwi. Stopień trudności montażu oceniamy na 1-2 (w skali 1-5). Czas montażu na 10m² to około 2-4 godzin, w zależności od rodzaju materiału i sposobu układania. Orientacyjny koszt materiałów na 10m² to 600-1200 PLN dla mat cienkowarstwowych, 300-600 PLN dla płyt korkowych, i 400-800 PLN dla cienkich płyt XPS (ceny orientacyjne). Metodę izolacji na podłodze polecamy szczególnie do renowacji mieszkań w blokach, domów z lat 70-80, gdzie zależy nam na szybkim i ekonomicznym ociepleniu podłogi, bez dużych prac remontowych. Jest to rozwiązanie praktyczne, wygodne i pozwalające na szybką poprawę komfortu cieplnego w pomieszczeniu.
Podsumowując, wybór metody izolacji drewnianej podłogi zależy od wielu czynników – rodzaju podłogi, budżetu, oczekiwań, i umiejętności. Izolacja między legarami to klasyczne i skuteczne rozwiązanie dla podłóg na legarach. Izolacja pod podłogą to idealny wybór dla nowych domów i podłóg z ogrzewaniem podłogowym. Izolacja na podłodze to szybka i prosta metoda renowacji, idealna dla mieszkań i starszych domów. Pamiętaj, że kluczem do sukcesu jest dokładna ocena stanu podłogi, dobór odpowiednich materiałów i staranny montaż. Nie bój się eksperymentować i pytać ekspertów – w końcu, ciepła podłoga to inwestycja w Twój komfort i zdrowie na lata. A jak mawiają starzy majstrzy, "Dobra izolacja to ciepłe stopy i spokojna głowa!". I tego Ci życzymy.